【食品業界とプラスチック加工技術③】製麺加工工場における異物混入防止戦略
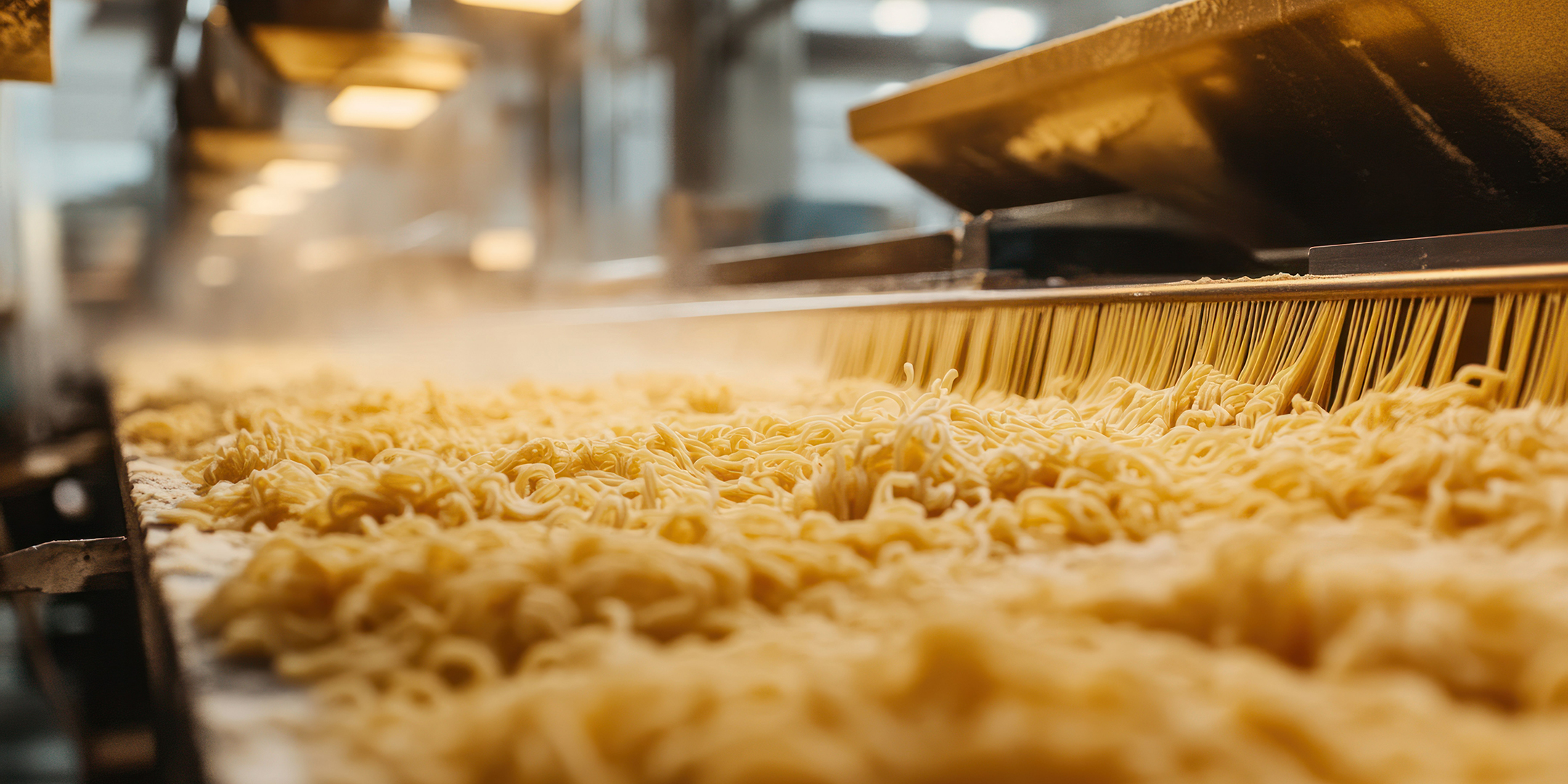
製麺加工工場では、うどん、そば、中華麺などの製品が日々大量に生産されています。しかし、その生産過程においては異物混入リスクが常に存在し、特に衛生管理や粉塵対策が欠かせない要素となっています。
特に粉塵の滞留による虫の発生リスクや異物混入の防止は、重点的に対策を講じるべき課題です。さらに、工程の切替時や洗浄作業の負担が増大し、HACCP基準への対応が厳格化されています。
本稿では、「虫発生抑制」「粉塵管理」「加熱工程衛生対策」を同時に実現する現場改善戦略の重要性に着目し、プラスチック加工技術の導入による具体的な改善策を提案していきます。
食品業界向け 異物混入対策プラスチック技術シリーズ 一覧
食品工場で求められる異物混入防止の最新トレンドと、現場ごとの課題に応じたプラスチック加工技術の具体的な活用戦略を解説するシリーズです。衛生・品質向上に貢献する現場改善策や技術ノウハウを、分野別に分かりやすくご紹介します。
- 【技術①】カット野菜工場における異物混入防止戦略
カット野菜の製造工程で発生しやすい異物混入リスクに対し、専用樹脂パーツや耐薬品性プラスチックの導入による異物混入ゼロの取り組みと現場実践例を紹介します。 - 【技術②】惣菜工場における異物混入防止戦略
複雑な設備が多い惣菜工場での異物混入対策として、洗浄性・耐久性に優れたプラスチック部品や溶接技術を活用し、衛生管理と生産性向上を両立させる方法を解説します。 - 【技術③】製麺加工工場における異物混入防止戦略(このページ)
製麺工程特有の異物混入リスクに対し、耐摩耗性や摺動性に優れたプラスチックの選定・加工ノウハウをもとに、設備の安全性・清潔性を高める具体策を紹介します。
※太字(このページ)表記が現在閲覧中の記事です。
製麺加工工場における主な異物・衛生リスクとは?
製麺工場では、粉塵の発生による虫の発生リスクや金属片、プラスチック破片の混入リスクが問題視されています。特に粉塵管理の不備から虫が発生した場合、異物クレームだけでなく工場ライン停止や製品全回収という深刻な事態に発展する可能性があります。これらのリスクを軽減するためには、発生源の特定とそれに応じた対策が必要です。
リスク種別 | 主な発生源・原因 |
虫(小麦粉害虫) | 粉塵滞留、湿気環境 |
金属片 | ミキサー・搬送設備劣化 |
プラスチック破片 | 搬送シュート・カバー破損 |
髪の毛 | 作業者由来(静電付着) |
ゴム片・ビニール片 | 手袋破損、材料袋開封ミス |
製麺加工工場では、大量の粉体を取り扱う工程が多く、粉塵の滞留や虫の発生リスクが常に存在しています。さらに、設備の老朽化や作業者のミスによっても異物混入リスクが増大し、生産ライン全体の品質管理が問われます。これらのリスクを軽減し、衛生基準を確保するためには、発生源の特定と徹底的な管理が求められます。
次章では、異物混入リスク管理の基本戦略として具体的な改善策を解説していきます。
異物混入防止・衛生対策の基本戦略
異物混入リスクを抑制するための基本戦略は、大きく発生源管理、視認性の向上、静電防止の3つに分けられます。
①発生源管理の徹底
異物混入を防ぐ第一歩は、リスクの発生源を取り除くことです。以下は異物混入リスクの抑制において最も基本的な取り組みです。
- 粉塵滞留を防止(素材・構造工夫)
滑り性の高いプラスチック素材を採用し、粉塵の蓄積を防ぎます。搬送路の形状最適化も有効です。 - 設備老朽化部材の計画的交換
劣化片の発生を防ぐため、耐摩耗性素材への交換を定期的に実施します。 - 防虫ゾーンの陽圧化・密閉構造化
防虫ゾーンの陽圧化と密閉構造の導入で虫の侵入を防止します。
粉塵の滞留防止には滑り性の高いプラスチック素材の採用が有効であり、老朽化した設備部材の計画的交換も異物発生の抑制につながります。さらに、防虫ゾーンの陽圧化や密閉構造の導入により、虫の侵入経路を遮断し、衛生管理を強化できます。
②視認性・検査精度向上
異物混入を防ぐには、粉塵や虫を早期に発見できる環境づくりが重要です。透明カバーの設置や照射検査の導入により、設備内部の状態が確認しやすくなります。これらの対策を組み合わせることで、異物の見落としを減らし、検査精度を高めることができます。
- 透明カバー化・ライト照射検査導入
透明カバーと照射設備の導入により、異物の視認性を高め、迅速な検査対応が可能になります。 - 異物・虫を早期発見できる設備設計
検査精度を高めるため、異物発生箇所に検出機能を持つ設備を設置します。
視設備内部を見やすくすることで、異物の早期発見が可能になり、検査精度の向上にもつながります。さらに、ライト照射検査との併用により、粉塵や虫の付着箇所が即座に確認できる環境を構築できます。こうした視認性強化策は、多くの場合、透明プラスチックが使われています。
③静電防止・付着防止
製麺工場内では、粉塵が静電気によって設備表面に付着しやすくなります。これを防ぐために、帯電防止プラスチックの活用が有効です。帯電防止素材を用いることで、粉塵の蓄積を防ぎ、清掃作業の負担軽減にもつながります。
- 帯電防止プラスチック活用
帯電防止素材を設備表面に使用し、粉塵の静電付着を防止します。 - 清掃性向上設計で粉塵発生源ゼロへ
清掃性を高める構造設計により、粉塵の堆積を抑え、異物混入リスクを低減します。
製麺加工工場においては、異物混入リスクを低減し、生産効率を高めるために、各工程でプラスチック加工技術が積極的に活用されています。
次章からは各工程別にプラスチック活用による改善策を詳述します。
粉混合(ミキシング)工程でのプラスチック活用
粉混合工程は、製麺工場において粉塵が最も滞留しやすい工程です。この工程では、粉塵の滞留による虫発生リスクや、攪拌装置の摩耗・腐食が異物混入の主要な原因となります。これらのリスクを軽減するために、プラスチック加工技術を駆使した改善策が有効です。
①粉塵滞留防止と清掃性向上
滑り性の高いプラスチック素材を導入することで、粉塵の蓄積を抑え、清掃作業を効率化できます。特にUHMW-PE(超高分子量ポリエチレン)は、粉体が滑りやすく、付着や滞留を防ぐ効果があります。
- 粉体流動性の向上、滞留ゼロ
滑り性の高いUHMW-PEにより粉体の流れが良くなり、滞留が防がれます。 - 清掃時間短縮、虫発生リスクの抑制
粉塵が付着しにくいため、清掃が短時間で済み、虫の発生リスクも低減されます。
②劣化・腐食リスク排除
攪拌装置や内部ガードの摩耗・腐食を防ぐには、耐摩耗性と耐薬品性を兼ね備えたプラスチック素材が有効です。POM(ポリアセタール)やUHMW-PEへの切替が推奨されます。
- 腐食片・摩耗片の発生ゼロ化
摩耗や腐食による異物発生を防止し、品質維持に貢献します。 - 設備寿命の延長
耐久性の高いプラスチック素材の導入で、交換頻度が減り、設備の稼働期間が延びます。
③静電防止で粉塵付着抑制
静電気の発生による粉塵付着を防ぐには、帯電防止素材の導入が効果的です。UHMW-PEやPVCの帯電防止タイプを選定することで、設備表面の粉塵付着を抑制できます。
- 異物発生の抑制
静電気を抑えることで、粉塵の付着を防ぎ、異物発生のリスクを軽減します。 - 清掃作業負担の軽減
粉塵が付きにくいため、清掃の頻度や時間を短縮できます。
④透明カバーで点検性向上
設備内部の視認性を確保するためには、透明PMPカバーの設置が有効です。投入・排出部のカバーを透明化することで、内部の粉塵や異物の蓄積状況を確認しやすくなります。
- 粉だまりや異物の早期発見
内部の状態が見えやすくなり、異物の発生箇所が即座に把握できます。 - ライン異常の迅速な検知
透明カバーにより、稼働中の設備異常も視覚的に確認しやすくなります。
粉体搬送・成型・乾燥工程でのプラスチック活用
粉体搬送や成型、乾燥工程は、製品の形状や品質を決定する重要なプロセスです。しかし、この工程では粉塵が飛散しやすく、異物混入や虫の侵入リスクが高まります。さらに、粉体の搬送路内に残渣が溜まると異物の発生源となり、清掃作業の負担も増大します。こうした課題に対応するためには、搬送路の密閉化や滑り性の高いプラスチック素材の活用が効果的です。視認性を高めるための透明化や異物検査設備の設置も併せて検討されます。
①搬送路の透明化・密閉化の導入
粉体搬送工程では、粉塵の飛散や虫の侵入が異物混入の原因となりやすいです。これらのリスクを抑えるために、搬送路の透明化と密閉化が有効です。
- 虫の侵入リスクの低減
密閉構造により、粉塵が飛散しにくく、虫の侵入を防ぎます。 - 異物発見率の向上
内部の可視化により、異物の早期発見が可能になります。
②滑り性の高いプラスチック素材の採用
搬送路や成型部では、粉体が滞留しやすく、異物の発生源になることが多いです。これを防ぐためには、滑り性の高いプラスチック素材の導入が効果的です。
- 清掃作業負担の軽減
滑り性のある素材により、粉塵が付きにくくなり、清掃が簡単になります。 - 異物混入の防止
粉塵が滞留せず、異物の発生源が減少します。
③ライト照射検査台の設置
粉体搬送工程では、暗所や視認性の低い箇所に異物が溜まりやすいです。これを防ぐには、照射設備の設置で視認性を高めることが効果的です。
- 異物発見率の向上
照射検査により、異物の見逃しが減少します。 - 検査作業の効率化
視認性が向上し、検査時間の短縮につながります。
茹でる・蒸す加熱工程でのプラスチック活用
茹でる・蒸すといった加熱工程では、高温環境下での異物付着や劣化が発生しやすくなります。特に食品の搬送や蒸し工程では、衛生性を保ちながら異物の侵入を防ぐことが求められます。耐熱性のあるプラスチック素材の導入により、高温環境下でも劣化を抑え、衛生管理と製品保護を両立させることが可能です。さらに、密閉型カバーの採用により、虫の侵入リスクを低減し、工程全体の衛生性を強化できます。
①耐熱プラスチック部材による劣化・腐食防止
加熱工程では、高温環境により設備の劣化や腐食が進行しやすくなります。これを防ぐために、耐熱性の高いプラスチック素材を導入します。
- 高温環境下での耐久性向上
耐熱性プラスチックの導入で、加熱工程における劣化リスクを最小限に抑えられます。 - サビ・腐食リスクのゼロ化
耐薬品性も備えているため、洗浄時の腐食も防止できます。
②茹で上げ後の異物付着防止
茹で上げ後の搬送工程では、食品が柔らかくなっているため異物が付着しやすくなります。これを防ぐために、滑り性の高いプラスチック素材の活用が有効です。
- 衛生性の保持
食品が滑りやすいため、異物の付着が防止され、衛生管理が強化されます。 - 製品破損リスクの低減
滑り性が高いため、食品がトレイやシュートで引っかかることがなく、破損リスクも軽減されます。
③蒸し工程での防虫対策
蒸し工程では、高温・高湿度環境が虫の侵入を助長しやすくなります。異物混入リスクを防ぐためには、防虫対策の徹底が必要です。
- 虫の侵入リスクの排除
密閉構造により、蒸し工程での虫の侵入を防止。 - 衛生環境の強化
プラスチックカバーにより、蒸気や食品成分の飛散も抑制されます。
④静電防止・カラー設計で異物可視化+付着防止
製麺工場内では、静電気の発生による粉塵付着や異物の見逃しが発生しやすい環境です。これを防ぐために、帯電防止素材の導入とカラー設計の工夫が有効です。
- 異物発見率の向上
異物と背景のコントラストが強調され、発見しやすくなります。 - 清掃作業負担の軽減
帯電防止素材により粉塵が付着しにくくなり、清掃時間が短縮されます。
プラスチックとステンレス304の比較
製麺工場では、長年にわたりステンレス304が主要な設備材として使用されてきました。しかし、近年では軽量で滑り性や耐薬品性に優れるプラスチック素材の導入が進んでいます。
以下の比較表では、両者の特性を「衛生性」「滑り性」「軽量性」「耐薬品性」「コスト」の観点から整理しました。プラスチック素材の活用は、異物混入防止や清掃作業の効率化において特に有効です。
比較項目 | ステンレス304 | プラスチック(UHMW-PE・PP・PMPなど) |
衛生性 | 粉塵付着・サビリスクあり | 腐食ゼロ、粉塵付着リスク低 |
滑り性 | 粉滞留しやすい | 粉滑りやすく滞留防止 |
軽量性 | 重く、清掃作業負担あり | 軽量で清掃性UP |
耐薬品性 | 洗浄剤負荷で劣化リスクあり | 強薬品耐性あり |
コスト | 初期・修繕コスト高 | 導入・更新容易、低コスト運用 |
プラスチック素材の導入は、粉塵付着やサビのリスクを低減し、衛生性や清掃性の向上が期待できます。特に耐薬品性の面では、洗浄剤による劣化リスクが少なく、長期間安定した運用が可能です。また、軽量で取り扱いやすいため、設備交換時の負担も軽減されます。コスト面でも初期費用は抑えられ、運用・更新の効率化にも寄与します。
まとめ
製麺加工工場において、粉塵や虫の発生リスクをゼロに抑え、異物混入ゼロの生産環境を構築することは、競争力を高めるための必須条件です。本稿で取り上げた改善策は、各工程の特性に応じたプラスチック加工技術の活用により、以下の5つの目標を同時に達成することを目的としています:
- 粉塵・虫発生リスクゼロ:粉混合工程では、滑り性の高いUHMW-PEの導入により、粉塵の滞留を防ぎ、清掃性を高めることで虫発生リスクを抑えます。
- 異物混入ゼロ:搬送・成型・乾燥工程では、透明カバーや密閉化により、異物の早期発見と虫の侵入防止を同時に実現します。
- 洗浄作業負担削減:帯電防止プラスチックの活用で粉塵の付着を防止し、清掃性を向上させます。ブルー色設計により異物の視認性も高まります。
- 加熱工程衛生強化:耐熱性プラスチック(PP・PPS)の採用で、高温環境でもサビや劣化片の発生を防止し、製品の衛生性を確保します。
- 生産効率最大化:各工程の最適化とプラスチック素材の活用により、製品品質の安定と生産効率の向上を図ります。
これらの対策を一貫して行うことで、「虫発生抑制」「粉塵管理」「加熱工程衛生対策」を同時に実現できる現場改善策が構築されます。
プラスチック加工技術は、衛生環境の向上だけでなく、異物混入リスクの低減や設備寿命の延長にも貢献する最適な選択肢です。これからの製麺加工現場において、効率化と安全性の両立を図るために、積極的な導入を検討することが求められます。
食品業界向け 異物混入対策プラスチック技術シリーズ 一覧
食品工場で求められる異物混入防止の最新トレンドと、現場ごとの課題に応じたプラスチック加工技術の具体的な活用戦略を解説するシリーズです。衛生・品質向上に貢献する現場改善策や技術ノウハウを、分野別に分かりやすくご紹介します。
- 【技術①】カット野菜工場における異物混入防止戦略
カット野菜の製造工程で発生しやすい異物混入リスクに対し、専用樹脂パーツや耐薬品性プラスチックの導入による異物混入ゼロの取り組みと現場実践例を紹介します。 - 【技術②】惣菜工場における異物混入防止戦略
複雑な設備が多い惣菜工場での異物混入対策として、洗浄性・耐久性に優れたプラスチック部品や溶接技術を活用し、衛生管理と生産性向上を両立させる方法を解説します。 - 【技術③】製麺加工工場における異物混入防止戦略(このページ)
製麺工程特有の異物混入リスクに対し、耐摩耗性や摺動性に優れたプラスチックの選定・加工ノウハウをもとに、設備の安全性・清潔性を高める具体策を紹介します。
※太字(このページ)表記が現在閲覧中の記事です。