【ゴムとプラスチック加工②】ゴム材料選定術:失敗事例と用途別ポイントを徹底解説
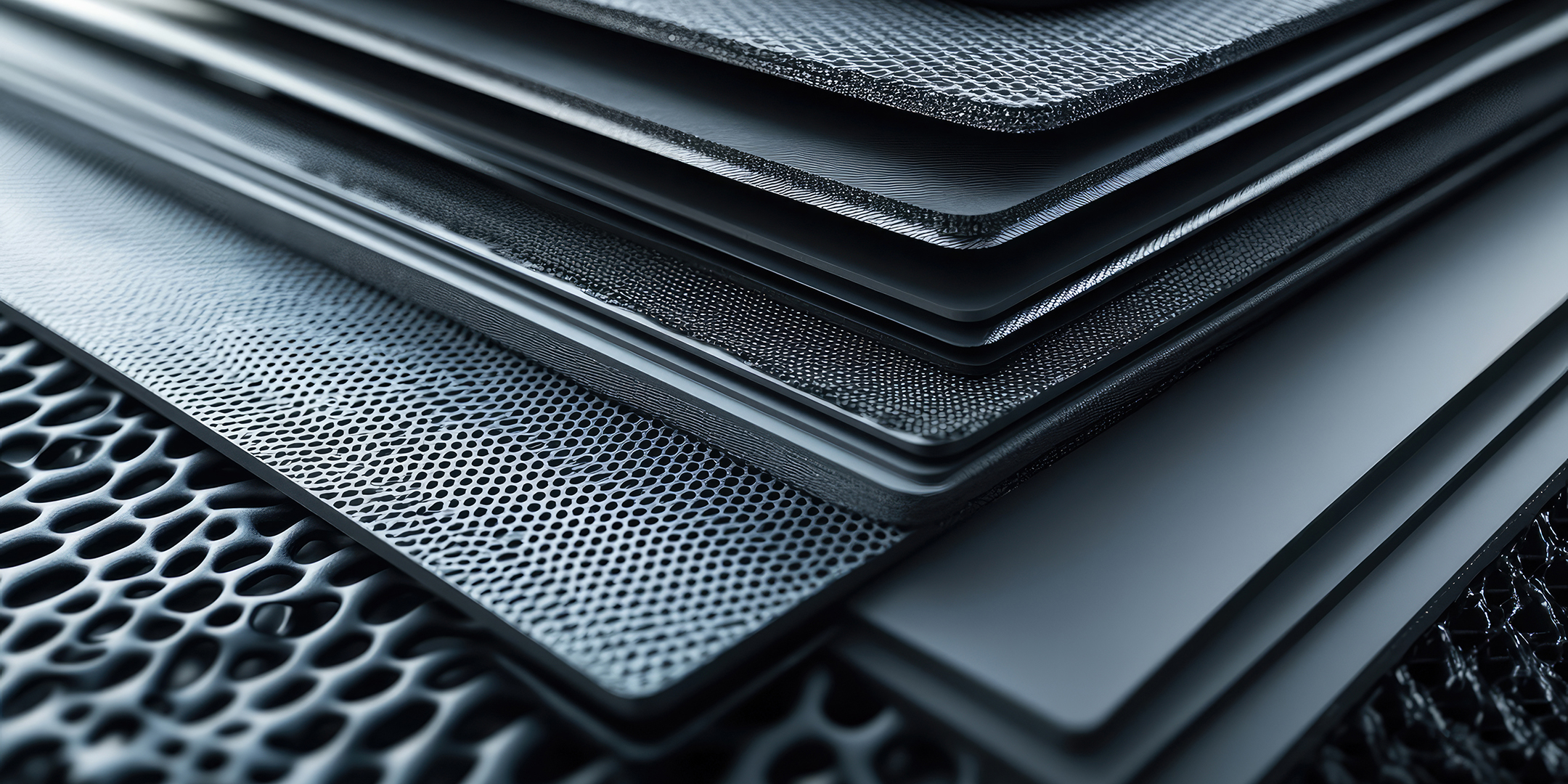
近年、プラスチック製品の高機能化や複雑化が進むなかで、プラスチック部品とゴム部品を組み合わせた構造設計が、多くの産業機器や装置で採用されるようになっています。
プラスチックの「軽量性」「加工性」「剛性」などのメリットを活かしながら、ゴムによる「密封性」「緩衝性」「振動吸収」といった機能を加えることで、製品全体の性能や耐久性、操作性を一段と高めることができるからです。
このような複合構造は、特に食品・医療・半導体・産業機械など、品質保証や安全性、クリーン性が強く求められる現場でますます需要が高まっています。一方で、複数の機能材料を適切に組み合わせるためには、単なる材料選びだけでなく「用途と環境に合った最適設計」という視点が欠かせません。
しかし、その一方で、ゴム部品の選定ミスやプラスチック材料との相性の見落としが、現場でのトラブルや装置全体の信頼性低下につながるケースも少なくありません。
「どのゴムを使えばよいのか?」という悩みは、設計担当者や現場スタッフがしばしば直面するテーマであり、見た目や硬さだけで材料を選んでしまうと、密封不良・早期劣化・異物混入といった問題を引き起こし、結果としてコストや信頼性の両面で大きな損失につながります。
本コラムでは、ゴム材料選定で起こりやすい失敗例や、プラスチック部品との組み合わせを意識した用途ごとの最適な材質選びのポイント、そしてフジワラケミカルエンジニアリングが現場で実践している実務的な判断基準とノウハウについて詳しく解説します。
ゴムとプラスチック加工シリーズ 一覧
ゴムとプラスチック部品の最適な組み合わせ設計や素材選定、Oリング溝設計、寿命管理まで、現場で役立つ知見を体系的に解説するシリーズです。構造設計からトラブル防止、長寿命化まで、プラスチック加工メーカーの視点で実践ノウハウをまとめています。
- 【ゴム×プラ①】機能性を最大化するプラスチック×ゴムの構造設計ノウハウ
ゴムとプラスチックの異素材組み合わせによる構造設計のポイントや、用途別の最適設計を解説します。 - 【ゴム×プラ②】ゴム材料選定術:失敗事例と用途別ポイントを徹底解説(このページ)
トラブル事例をもとに、用途ごとのゴム材選定と現場で使えるチェックポイントを紹介します。 - 【ゴム×プラ③】プラスチック部品のOリング溝設計と密封性向上のポイント
Oリング溝の設計ノウハウや密封性・長寿命化のための現場テクニックを解説します。 - 【ゴム×プラ④】ゴムの経年劣化と寿命管理:適切な交換タイミングとは
ゴム部品の劣化メカニズム、寿命管理、現場で役立つ予防保全のポイントを実践目線でまとめています。
※太字(このページ)表記が現在閲覧中の記事です。
なぜ選定ミスが起こるのか
現場での典型的な誤りは、「見た目が同じ」「硬さが近い」といった主観的な基準で選んでしまうことです。
特に、プラスチックとゴムを組み合わせた複合部品は年々構造が複雑化しており、適切な材料選びが一層重要になっています。
たとえばEPDMとNBRは黒色で似た質感ですが、EPDMは耐候性・耐オゾン性に優れる反面、油に弱い。逆にNBRは油に強いが紫外線や屋外環境に弱いといった特性を持っています。こうした違いを見落とすと、不具合の原因となります。
実際、設計段階では「これで十分だろう」と安易に判断されがちな場面が多々あります。しかし、使用開始後になってからトラブルが顕在化し、その都度手直しや部品交換、さらには装置全体の再設計にまで発展するケースもあります。
「なんとなく」で選んだ材質が、思わぬリスクを生むことを現場の誰もが痛感しています。
実際、以下のような選定ミスが現場トラブルにつながった事例が多く報告されています。
- 屋外装置にNBRを使い早期ひび割れ
- 食品設備に非衛生的なゴムを使用
- 高摩耗用途に低硬度ゴムを使用し部品落下事故
用途別に見る適材適所
適切なゴム選定には、「使用環境・荷重条件・接液条件・温度変化・接触するプラスチック材料」など複数の要素を同時に検討する必要があります。
たとえば食品装置では、異物混入や衛生面への配慮から食品グレードのシリコンやEPDMが選ばれやすく、洗剤・薬品の洗浄工程が頻繁な場合には耐薬品性が必須条件となります。
薬品装置では溶剤や酸・アルカリに長期間さらされることが多く、FKM(フッ素ゴム)や耐薬品性に優れたEPDMが主流です。
水処理装置や屋外機器では、EPDMの耐水性・耐オゾン性が現場の評価につながっています。
油圧装置の場合はコストと性能のバランスからNBRが多用されますが、温度や作動油の種類まで細かく条件を詰める必要があります。
用途例 | 推奨ゴム材 | 主な理由 |
---|---|---|
食品装置 | シリコン、EPDM(食品グレード) | 無毒性、高温耐性、洗剤耐性 |
薬品装置 | FKM(フッ素ゴム)、EPDM | 耐薬品性・膨潤抑制 |
水処理装置 | EPDM | 耐水性・耐オゾン性 |
油圧装置 | NBR | 耐油性・価格安定 |
屋外機器 | EPDM、CR | 耐候性・耐オゾン性 |
同じ環境下でも微妙な条件の違いによって求められる特性が大きく異なるため、現場担当者や設計者、材料メーカーとの密な連携も重要です。
ゴムの選定ミスによるトラブル事例
ゴム材料の選定ミスが実際にどのようなトラブルを招くのか、具体例を知ることでリスクの本質を理解しやすくなります。ここでは代表的な事例を取り上げます。
→ 数週間で膨潤し、弾力を失い密封不能に。
→ シール材が硬化・劣化し、1ヶ月で漏れ発生。
→ 紫外線によってひび割れ、粉吹きが発生。
いずれも「材質の思い込み」や「コスト優先」の誤選定が要因です。
特に、現場の初期導入コストを抑えるために安価な材質を選ぶケースや、「前回と同じで良いだろう」という慣例的な判断が、結果的に大きな損失や装置停止リスクを招いてしまうことも少なくありません。
こうした失敗事例から学び、「用途と条件に適した材質選定こそが全体品質とコスト最適化の両立に直結する」という視点を全社的に共有することが重要です。
ゴム選定の基本フロー 〜お客様との対話からはじまる選定プロセス〜
ゴム材の選定には「単に性能表を比較して決める」以上のプロセスが必要です。
私たちフジワラケミカルでは、お客様の使用目的や装置構造を丁寧にヒアリングしたうえで、次のような流れに沿って材質を選定しています。
- 接触する液体や温度、圧力などの確認
- 使用頻度や脱着回数、清掃の有無なども把握
- 食品衛生法、FDA、RoHSなどの対応可否を確認
- 同様の環境で使われた材質を基に候補を提示
- Oリング溝寸法、圧縮率、保持構造などとの整合性
- 実際の装置に取り付けて評価テストを実施(必要に応じて)
- 最終的な材質決定とともに設計にフィードバック
このようなフローを経ることで、単なる「材質選定」ではなく、「装置全体としての完成度」を追求しています。
設計初期段階から現場担当者とのコミュニケーションを重ね、実際の使用環境やメンテナンス方法も考慮したうえで最適な提案を行う…これが私たちの大きな強みです。
「お客様の現場課題に寄り添いながら、最適解をともに導き出す」。この対話型のプロセスが、長期的な信頼と品質確保につながっています。
フジワラケミカルの現場における判断軸(設計判断の実例と注意点)
フジワラケミカルエンジニアリングでは、ゴム単体での性能ではなく、「装置に組み込んだときの機能性」を重視して材質を選定しています。
この点は繰り返しになりますが、当社のゴム選定における最大のこだわりであり、単なる材質のスペックではなく、「実装時のパフォーマンス」こそが最も重要だと考えています。
- 接液部に薬品が使用されるかどうか、洗浄工程はあるか?
- プラスチック部品との熱膨張差により、Oリングが偏圧されないか?
- 脱着時の滑り・摩擦が装置の操作性に影響しないか?
たとえば、装置が高頻度で分解・清掃される食品製造ラインでは、ゴム部品が頻繁に着脱されるため、摩耗や変形への耐性はもちろん、組立ミスを防ぐ形状設計も不可欠です。
また、半導体や医療分野では、ごく微量の異物混入が大きな品質問題に直結するため、材質の純度や表面性状、洗浄・滅菌適性まで踏み込んだ選定が求められます。
加工現場と連携しながら、溝の形状・圧縮量・使用頻度も含めて最適化していく設計が私たちのスタンスです。
現場からの改善要望やフィードバックも随時反映し、「使いながら進化する」ものづくりの体制を築いています。
ゴム部品活用の具体提案と今後の展開
私たちは設計初期段階から「ゴム部品を活かす構造提案」を実践しています。
特にOリングは、「材質」だけでなく「どう納めるか」の設計が密封性・寿命・メンテ性を左右します。
- 外部から点検できる透明カバーの採用
- ワンタッチで取り外しできる構造設計
- Oリング保持形状を加工精度で制御し、組立ミス防止
現場では分解・清掃・メンテ性まで視野に入れた設計提案を進めています。
こうした構造提案を積み重ねてきた結果、実際の製造現場からは「作業性が大きく向上した」「清掃や点検の手間が削減できた」「トラブル発生率が減った」といった具体的な評価やご要望も数多く寄せられています。また、食品・医療・半導体など異物混入や洗浄性への要求が厳しい業界での実績も蓄積されており、設計現場とユーザー現場が連携しながら品質の底上げを図っているのが当社の特徴です。
今後は、より多様なプラスチック材料やゴム材料の組み合わせにも柔軟に対応できる設計技術を磨き、現場で得られる実証データやフィードバックを積極的に蓄積・分析していく方針です。
また、業界標準や国際規格にも即応し、さらにメンテナンスの容易さとコストダウンを両立する新たな構造提案にも力を注いでいきます。
- より多様なプラスチック材料・ゴム材料の組み合わせに対応した設計技術の強化
- 作業現場での実証データやフィードバックの蓄積・分析
- 業界標準や国際規格への柔軟な対応
- メンテナンス容易性とコストダウンの両立を実現する新たな構造提案
こうした継続的な技術革新と現場目線の実践を通じて、ゴムとプラスチックの複合部品に関するベストプラクティスを業界全体へ発信してまいります。
フジワラケミカルエンジニアリングは今後も、設計・製造・現場のすべての視点から、プラスチック構造と密接に関係するゴム部品の最適活用と、高付加価値な製品づくりを、実務現場からご提案し続けます。
ゴムとプラスチック加工シリーズ 一覧
ゴムとプラスチック部品の最適な組み合わせ設計や素材選定、Oリング溝設計、寿命管理まで、現場で役立つ知見を体系的に解説するシリーズです。構造設計からトラブル防止、長寿命化まで、プラスチック加工メーカーの視点で実践ノウハウをまとめています。
- 【ゴム×プラ①】機能性を最大化するプラスチック×ゴムの構造設計ノウハウ
ゴムとプラスチックの異素材組み合わせによる構造設計のポイントや、用途別の最適設計を解説します。 - 【ゴム×プラ②】ゴム材料選定術:失敗事例と用途別ポイントを徹底解説(このページ)
トラブル事例をもとに、用途ごとのゴム材選定と現場で使えるチェックポイントを紹介します。 - 【ゴム×プラ③】プラスチック部品のOリング溝設計と密封性向上のポイント
Oリング溝の設計ノウハウや密封性・長寿命化のための現場テクニックを解説します。 - 【ゴム×プラ④】ゴムの経年劣化と寿命管理:適切な交換タイミングとは
ゴム部品の劣化メカニズム、寿命管理、現場で役立つ予防保全のポイントを実践目線でまとめています。
※太字(このページ)表記が現在閲覧中の記事です。