【ゴムとプラスチック加工③】プラスチック部品のOリング溝設計と密封性向上のポイント
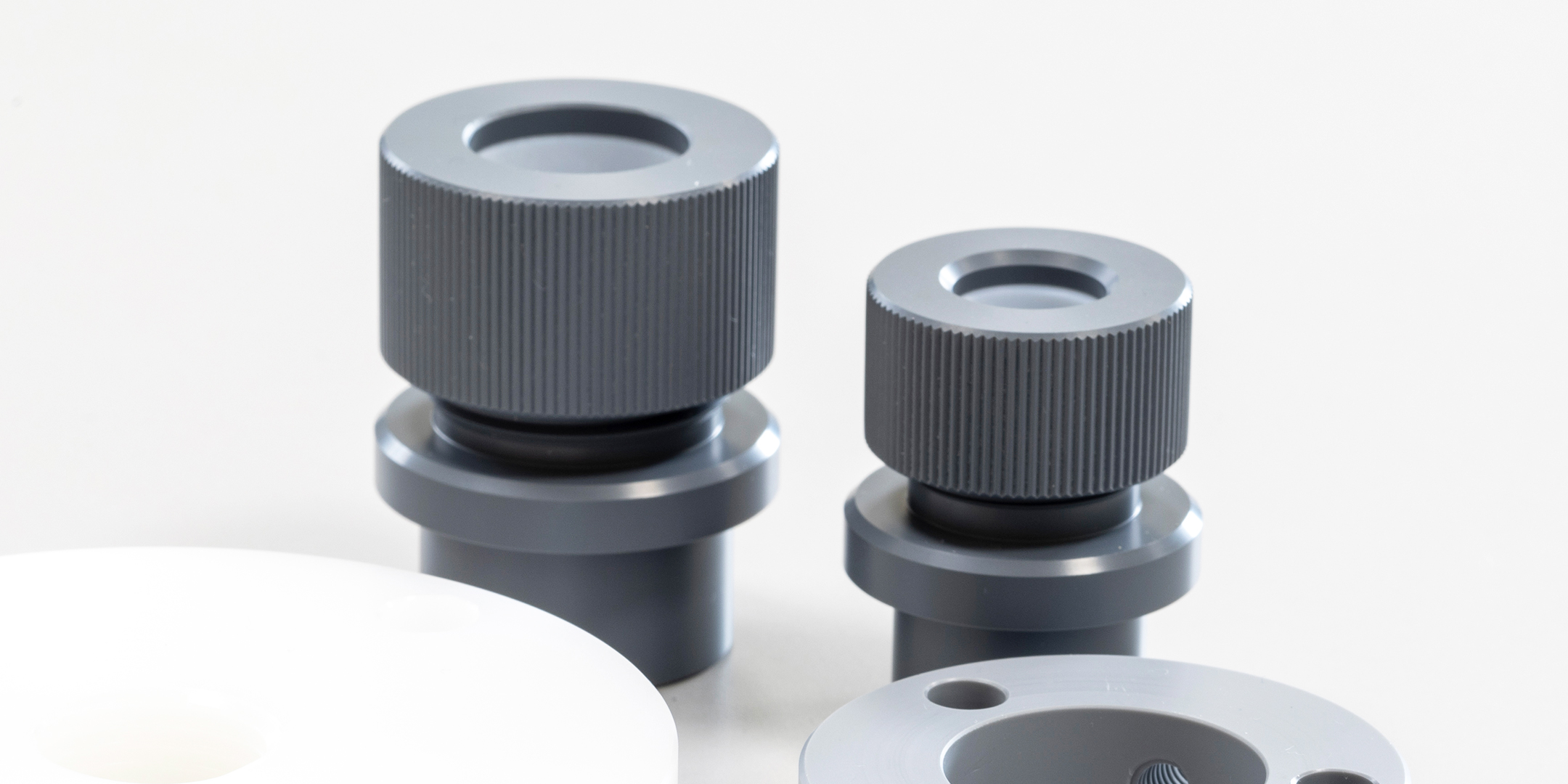
プラスチック製品におけるOリングの設計は、単なる「ゴムを挿入する」工程ではありません。溝の深さ・幅・形状・Oリングとの相性といった細部の寸法設計が、密封性能の成否を大きく左右します。とりわけ、プラスチックは金属と比べて変形しやすく、設計上の余裕や変位に弱いため、より繊細な配慮が求められます。
本コラムでは、Oリングによる密封構造の基本的な考え方から、プラスチック特有の設計上の注意点、さらにフジワラケミカルエンジニアリングが実践している加工上の工夫について詳述します。
ゴムとプラスチック加工シリーズ 一覧
ゴムとプラスチック部品の最適な組み合わせ設計や素材選定、Oリング溝設計、寿命管理まで、現場で役立つ知見を体系的に解説するシリーズです。構造設計からトラブル防止、長寿命化まで、プラスチック加工メーカーの視点で実践ノウハウをまとめています。
- 【ゴム×プラ①】機能性を最大化するプラスチック×ゴムの構造設計ノウハウ
ゴムとプラスチックの異素材組み合わせによる構造設計のポイントや、用途別の最適設計を解説します。 - 【ゴム×プラ②】ゴム材料選定術:失敗事例と用途別ポイントを徹底解説
トラブル事例をもとに、用途ごとのゴム材選定と現場で使えるチェックポイントを紹介します。 - 【ゴム×プラ③】プラスチック部品のOリング溝設計と密封性向上のポイント(このページ)
Oリング溝の設計ノウハウや密封性・長寿命化のための現場テクニックを解説します。 - 【ゴム×プラ④】ゴムの経年劣化と寿命管理:適切な交換タイミングとは
ゴム部品の劣化メカニズム、寿命管理、現場で役立つ予防保全のポイントを実践目線でまとめています。
※太字(このページ)表記が現在閲覧中の記事です。
プラスチック特有の設計留意点
Oリングの圧縮率が適正でない場合、密封性能は大きく損なわれます。過圧縮ではOリングが損傷し、逆に不足すれば漏れが発生します。ここで問題となるのが、プラスチックの弾性や熱膨張係数です。金属よりも大きく変形・収縮するプラスチックでは、環境温度の変化によって設計時の寸法が容易に狂ってしまいます。
また、切削加工品では加工時の微細な段差や表面の歪みが生じることがあり、Oリングの接触面の精度が密封性に大きく影響します。とくに複雑な溝形状や溶接による熱変形がある場合、わずかなズレが密封不良の原因となります。
当社では、こうした課題に対応するため、溝幅を若干広めに設計し、Oリングの可動域に「ゆとり」を持たせることで、加工公差や歪みによる密封不良を未然に防いでいます。
実践に基づく溝設計の工夫
当社が特に重視しているのは、「整備性」と「視認性」です。たとえば、食品用カバー部品においては、Oリングの状態を目視確認できるよう透明な保持部を設計し、必要に応じて片手で外せるツールレス構造を採用しています。
また、Oリングの磨耗やへたりがあっても即座に交換できるよう、ガイド溝をR加工で滑らかに仕上げ、装着のストレスを極限まで抑えています。さらに、試作段階で複数のゴム材・形状をテストすることで、製品リリース前に密封トラブルの芽を摘んでいます。
現場で直面する「密封トラブル」の正体
Oリングの密封トラブルは、ほんのわずかな寸法ずれや設計ミスから生じます。とくにプラスチック部品では、金属と異なる素材特性が思わぬ課題を引き起こすことも少なくありません。
現場では「なぜ漏れるのか?」「なぜ異音が出るのか?」といった問いに直面し、その多くが“溝設計の基本”や“材質との相性”に原因があると気付かされます。
次節からは、実際の現場事例を交えながら、Oリング溝設計の要点とプラスチック構造との最適な組み合わせを詳しく解説します。
Oリング溝設計の基本
Oリングの「収まり方」は、密封性能そのものを左右する最重要ポイントです。特にプラスチック部品の場合、わずかな寸法の狂いが密封不良やトラブルにつながるため、緻密な溝設計が求められます。現場では「ほんの数ミクロンの違い」が致命的な問題につながることも珍しくありません。下表に主な設計要点をまとめますが、それぞれの意味や注意点をもう一歩踏み込んで解説します。
項目 | 設計のポイント・推奨値 |
---|---|
溝の幅と深さ | Oリングが適切に圧縮される寸法設定が必要。断面の15〜30%圧縮率が目安。材料や用途によって最適な圧縮率は異なります。圧縮が不足すれば密封性が損なわれ、過剰になればOリング自体が損傷しやすくなります。 |
角部のR処理 | 溝の角が鋭角だとOリング損傷の原因。R0.2〜0.5程度の丸みを付けることが重要。シャープな角は取付け時のキズや、運転中の切れの発生リスクを高めるため、必ずR処理を施します。 |
圧縮方向の明確化 | ラジアル型(円周方向)かアキシャル型(直進方向)かによって溝形状が異なるため、圧縮方向を明確に設計する。方向性を誤ると、本来想定していた密封性能が発揮されません。 |
これらの基本を守らず、設計が不十分な場合にはさまざまなトラブルが起こります。たとえば、圧縮が足りないことでシール性が確保できなかったり、逆に圧縮しすぎてOリングが変形・破損してしまうこともあります。また、隙間が大きいとOリングが押し出される、あるいは捻じれてしまうといった問題も発生します。
- 圧縮不足による密封不良(漏れ・気密不良)
- 圧縮過多によるOリング破損や復元不良(取付け不良、再使用不可)
- 隙間が多すぎることでOリングの押し出しやねじれが発生(機器内部での異常動作や破損リスク)
これらのポイントをひとつずつ丁寧に押さえた設計を心掛けることで、Oリング本来の密封性能を最大限に引き出し、現場でのトラブルを未然に防ぐことが可能です。当社でも過去の失敗事例をもとに、設計段階から綿密な検証と寸法公差の確認を徹底しています。
材質ごとの設計留意点
Oリングの材質は、そのまま許容圧縮率や弾性特性、耐久性に直結します。見た目は似ていても、設計値を誤ると早期の劣化や密封不良を招くため、選定は慎重さが求められます。
材質 | 特徴・設計時のポイント |
---|---|
シリコン | 柔らかく密封性が高い一方、ねじれや潰れにはやや弱い。取り付け部に段差逃げなどの工夫が必要。 |
EPDM | 反発弾性が高く変形しにくい。やや大きめの圧縮でも安定してシール性能を発揮する。 |
FKM(フッ素ゴム) | 耐薬品性や耐熱性に優れるが、溝設計の精度や寸法公差に敏感。高精度な仕上げが必要。 |
Oリング材質は現場の見た目では判断しにくいため、設計段階から「材質ごとの特徴」を踏まえて寸法を決めることが不可欠です。材質選定の失敗は、密封性能だけでなくメンテナンス性や寿命にも大きく影響します。
プラスチックとの相性と加工の工夫
プラスチック部品にOリング溝を設ける場合、金属とは異なる特有の課題や設計上の工夫が必要です。特に、切削加工では材料ごとの性質や加工精度が密封性や組立性に直結するため、設計段階から細やかな配慮が求められます。以下の表に、当社が現場で重視している代表的な加工上のポイントをまとめます。
工夫・着眼点 | 内容・ポイント |
---|---|
湾曲補正の前加工 | プラスチック板の表面には微妙な湾曲が残るため、Oリング溝を設ける前に表面切削で基準面を整えます。これにより、溝の深さ精度を±0.05mm以内に保つことが可能です。 |
素材ごとの切削特性 | アクリルは欠けやすく、PPやPEは柔らかいため溝の精度が出にくい傾向があります。各素材に合わせた加工条件や工具選定が不可欠です。 |
溝の深さ精度 | 高い密封性を確保するには、Oリング溝の深さを±0.05mm以内に仕上げる必要があります。切削条件や刃物選定が精度確保のカギとなります。 |
透明性の活用 | アクリルやポリカーボネート(PC)などの透明素材を使うことで、Oリングの状態を外部から目視で確認できる設計も実現可能です。 |
加えて、組立現場やメンテナンス時の「人為的なミス」を減らす工夫も重要です。当社では以下のようなアイデアを積極的に採用し、作業効率や信頼性の向上につなげています。
- 色分けによる識別性向上
Oリング自体やその保持部品を色分けすることで、種類や位置の識別を容易にし、組み違い・入れ間違いの防止に役立てています。 - 非対称形状による組立ミス防止
Oリング溝の形状をあえて左右非対称にすることで、組立方向の間違いや逆付けのリスクを低減します。 - 表示・目印による作業支援
現場での視認性や取り付け時の迷いを減らすため、溝周辺にラベル(テプラ)やマーキングなどの目印を付け、誰でも正確に作業できる仕掛けとしています。
これらの加工上・現場対応の工夫を積み重ねることで、設計上の精度だけでなく、使いやすさやメンテナンス性、長期的な信頼性の確保にもつなげています。Oリング溝の設計は単なる寸法設定だけでなく、現場での扱いやすさや実際の使用環境まで見据えた「トータルな視点」で取り組むことが大切です。
フジワラケミカルの技術応用と構造提案
フジワラケミカルエンジニアリングでは、単にOリング溝を設計するだけでなく、装置全体の構造や運用現場での利便性までを見据えた総合的な提案を重視しています。「使いやすさ」「交換のしやすさ」「清掃性」といった現場視点の要素も密封設計の品質を大きく左右します。こうした現場での課題に応えるため、当社は以下のような具体的な技術応用や構造工夫を実践しています。
- 差し込み式構造による組立性向上
組立性を重視し、Oリングがズレないようなガイド加工を施した差し込み式構造を採用しています。 - 段差・逃げ加工による長寿命化
清掃や脱着が多い装置には、Oリングが接触するプラスチック面に段差や逃げ加工を設け、Oリングの摩耗を抑えています。 - 工具レス開閉と高変形Oリングの活用
工具を使わずに開閉できる構造設計や、柔軟性の高いシリコンOリングを使うことで、誰でも簡単に分解・交換ができるよう配慮しています。
- ゴム材質に応じた「収まり寸法」
各ゴム材料ごとに最適な寸法設定を行い、密封性・耐久性を確保します。 - 装置に求められる「分解・洗浄性」
現場での分解や洗浄作業がしやすい構造を設計段階から組み込むことで、保守性・衛生性も高めています。 - 加工性を加味した「図面上の仕掛け」
加工現場で実現可能な形状や公差管理など、実際の製造工程を見据えた図面設計で、品質・再現性を担保します。
このようにフジワラケミカルは、密封性だけでなく現場での使いやすさや長期信頼性までを一体的に考慮したトータルな技術提案を行っています。
ゴムとプラスチック加工シリーズ 一覧
ゴムとプラスチック部品の最適な組み合わせ設計や素材選定、Oリング溝設計、寿命管理まで、現場で役立つ知見を体系的に解説するシリーズです。構造設計からトラブル防止、長寿命化まで、プラスチック加工メーカーの視点で実践ノウハウをまとめています。
- 【ゴム×プラ①】機能性を最大化するプラスチック×ゴムの構造設計ノウハウ
ゴムとプラスチックの異素材組み合わせによる構造設計のポイントや、用途別の最適設計を解説します。 - 【ゴム×プラ②】ゴム材料選定術:失敗事例と用途別ポイントを徹底解説
トラブル事例をもとに、用途ごとのゴム材選定と現場で使えるチェックポイントを紹介します。 - 【ゴム×プラ③】プラスチック部品のOリング溝設計と密封性向上のポイント(このページ)
Oリング溝の設計ノウハウや密封性・長寿命化のための現場テクニックを解説します。 - 【ゴム×プラ④】ゴムの経年劣化と寿命管理:適切な交換タイミングとは
ゴム部品の劣化メカニズム、寿命管理、現場で役立つ予防保全のポイントを実践目線でまとめています。
※太字(このページ)表記が現在閲覧中の記事です。