【ゴムとプラスチック加工④】ゴムの経年劣化と寿命管理:適切な交換タイミングとは
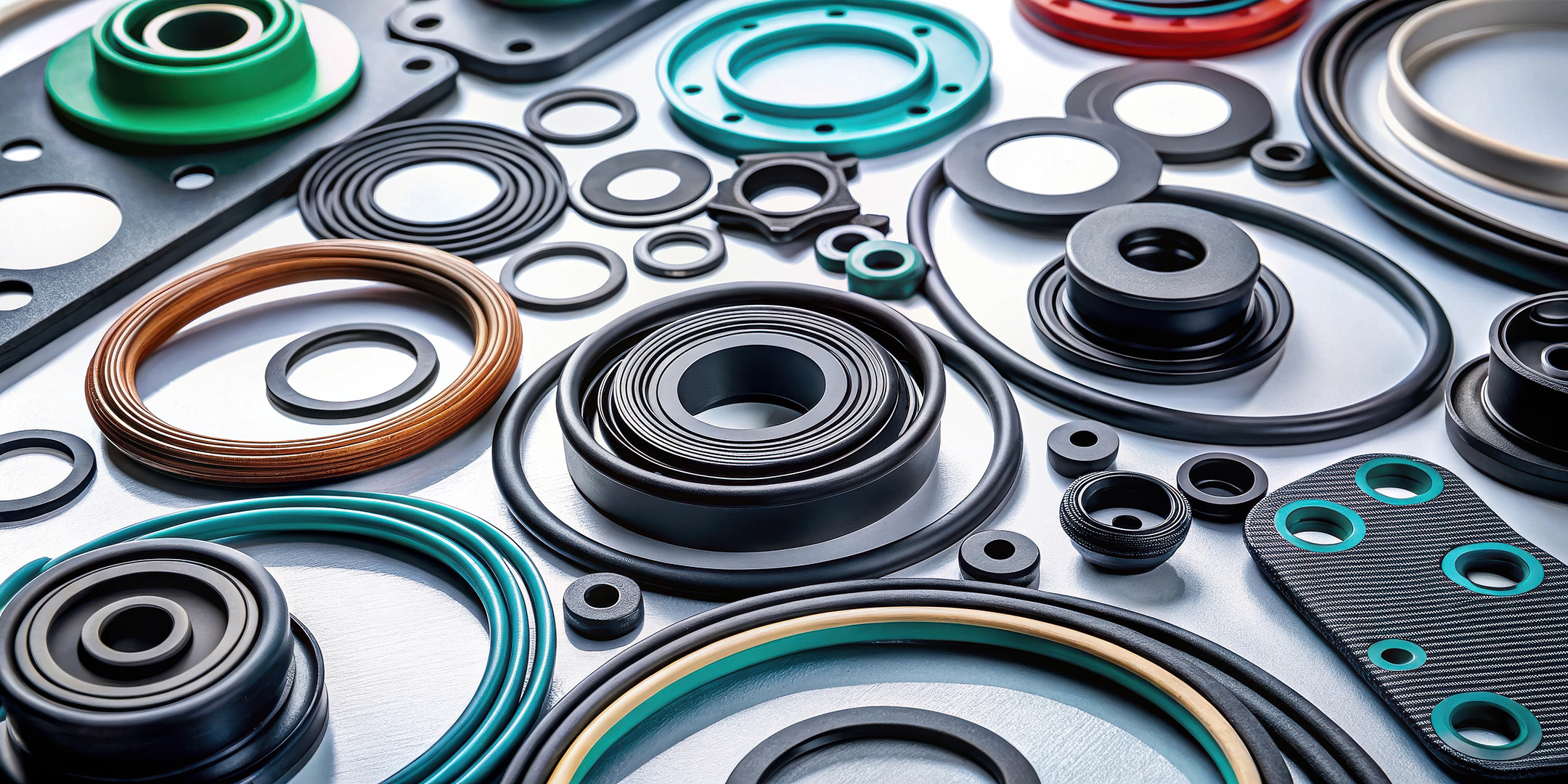
多くのプラスチック加工部品に組み込まれているゴム部品ですが、その寿命と劣化進行に着目した設計や管理ができている企業はまだ多くありません。ゴムは「使い続ければ劣化する」ことが前提の材料であり、その変化は製品トラブルの前兆であるにもかかわらず、見た目や触感では判断が難しいという特性があります。
このコラムでは、ゴム部品の経年劣化のメカニズムと寿命の考え方を解説し、プラスチック加工製品の長期信頼性を高めるための実践的な管理ポイントをご紹介します。
ゴムとプラスチック加工シリーズ 一覧
ゴムとプラスチック部品の最適な組み合わせ設計や素材選定、Oリング溝設計、寿命管理まで、現場で役立つ知見を体系的に解説するシリーズです。構造設計からトラブル防止、長寿命化まで、プラスチック加工メーカーの視点で実践ノウハウをまとめています。
- 【ゴム×プラ①】機能性を最大化するプラスチック×ゴムの構造設計ノウハウ
ゴムとプラスチックの異素材組み合わせによる構造設計のポイントや、用途別の最適設計を解説します。 - 【ゴム×プラ②】ゴム材料選定術:失敗事例と用途別ポイントを徹底解説
トラブル事例をもとに、用途ごとのゴム材選定と現場で使えるチェックポイントを紹介します。 - 【ゴム×プラ③】プラスチック部品のOリング溝設計と密封性向上のポイント
Oリング溝の設計ノウハウや密封性・長寿命化のための現場テクニックを解説します。 - 【ゴム×プラ④】ゴムの経年劣化と寿命管理:適切な交換タイミングとは(このページ)
ゴム部品の劣化メカニズム、寿命管理、現場で役立つ予防保全のポイントを実践目線でまとめています。
※太字(このページ)表記が現在閲覧中の記事です。
ゴムの劣化とは何か
ゴムは、その柔軟性や密封性などの特性から多くの工業製品や装置部品に使われていますが、「時間とともに必ず劣化していく材料」であることが最大の特徴です。新品の状態では十分な弾力や密着力を持つゴムでも、使用や保管の過程で少しずつ性能が低下し、いずれ本来の機能を発揮できなくなります。
この劣化は、材料内部の化学構造や物理的特性が徐々に変化していく現象で、原因や進行スピードは使用環境や材質、添加剤などによって大きく異なります。
ゴムの劣化が進行すると、外観の変化(ひび割れ・色あせ・粉吹き)だけでなく、目に見えない部分で弾性低下や密封性の喪失といった機能的な問題も生じます。そのため、「見た目に異常がなくても、実際には寿命が近づいている」ケースも珍しくありません。
ゴム部品の劣化は、装置の信頼性や安全性を左右する重大なリスク要因であり、いかに劣化を見逃さず適切に管理・交換できるかが、長期安定稼働のポイントとなります。
ゴム部品の寿命に影響する環境要因
ゴムの劣化は素材そのものの特性だけでなく、日々さらされる環境によっても大きく左右されます。高温や直射日光、湿度の高い場所、オゾンや薬品にさらされる環境下では、同じ材質でも劣化の進行が想定より早まることがあります。また、繰り返しの伸縮や圧縮、摩擦といった機械的な負荷が加わる部位も、短期間で性能が低下しやすくなります。
このように、「環境要因」もゴムの寿命管理では決して見逃せないポイントです。現場ごとに異なる使用条件や周囲環境を的確に把握し、そのリスクに応じた材質選びや点検・交換のタイミングを検討することが、部品の長寿命化と安定稼働につながります。
単に「ゴムの材質」だけで判断せず、実際の設置場所や運用実態も踏まえて管理を行うことが重要です。
劣化を見逃さないための現場目線
これまで述べてきたように、ゴム部品の劣化は時間の経過による化学的変化だけでなく、実際の使用環境によっても大きく左右されます。たとえば、高温や紫外線、薬品への曝露、繰り返し加わる機械的な負荷など、さまざまな要因が複雑に絡み合うことで劣化の進行速度が変わってきます。こうした複合的な影響があるため、「何年使えば必ず交換」という単純な管理が難しく、現場ではしばしば見た目や感触だけでは異常を見抜けないことが多いのが現実です。
そのため、現場では「不具合が起きて初めてゴムの劣化に気付く」「交換時期の見極めが難しい」といった課題が絶えません。
この「見逃されがちなリスク」をいかに防ぐかが、安定稼働や装置トラブル未然防止のカギとなります。
ここからは、これらの劣化要因・環境要因を踏まえたうえで、フジワラケミカルが実際の現場で重視している点検ポイントや、寿命管理のための工夫・実践ノウハウについて詳しくご紹介します。
ゴムが劣化するメカニズム
ゴムは本来、優れた柔軟性や密封性を持つ素材ですが、その分子構造の“しなやかさ”ゆえに、外部からの影響に非常に敏感です。長期間使用するうちに、さまざまな環境要因が徐々にゴム内部へ作用し、気づかぬうちに特性が損なわれていきます。
特に、以下の4つの要因は、ゴムの性能低下を加速させる代表的なものです。
- 酸化:空気中の酸素との化学反応により、ゴム分子同士の結合が変質し、弾力性が失われて硬化や割れが発生します。見た目は変わらずとも、内部ではじわじわと劣化が進んでいることが多く、突然の破断につながる場合もあります。
- 紫外線・オゾン:屋外設置や日光の当たる環境では、ゴムの表面が白っぽく変色したり、細かなひび割れ(チョーキング現象)が現れたりします。これはゴム表層の化学構造が分解されることで起き、見かけ以上に内部の劣化が進行しているサインです。
- 高温:高温下に長時間さらされると、ゴム内部の架橋構造が崩れ、柔軟性が失われます。これにより、元の弾力がなくなったり、表面がベタついたり、逆にカチカチに硬化してしまうことがあります。
- 薬品接触:用途によっては薬品や溶剤との接触が避けられません。ゴムの材質によっては膨潤、硬化、溶解といった化学変化が起き、密封性や強度が著しく損なわれる場合があります。
これらの現象は一夜にして起こるものではなく、日々の使用環境や設置条件の中でじわじわと進行していきます。
「いつの間にかシール不良や漏れが起きていた」「不具合の原因を調べたらゴム部品の劣化だった」というケースは、現場でも後を絶ちません。
劣化の兆候と見抜き方
ゴム部品の交換タイミングを適切に判断するには、現場でのきめ細かな観察が欠かせません。
劣化兆候を早期に見抜くため、以下のようなチェックポイントを日常点検に取り入れると効果的です。
劣化兆候 | 確認方法 | 判断基準 |
---|---|---|
ひび割れ(クラック) | 目視・指触診 | 表面の細かな線や亀裂、カサつきがある |
弾性低下 | 指で押す・曲げる | 元に戻らない、固く感じる |
膨潤・ベタつき | 拭いてみる | ヌルヌル感、サイズ変化あり |
色の変化・粉吹き | 目視 | 色あせ、白い粉が浮いている |
また、最近では点検の手間を減らすために、透明カバーや点検窓付きの設計も増えています。これにより工具を使わず、現場で簡単に状態確認ができ、計画的なメンテナンスにつなげやすくなります。
寿命の目安と交換管理の考え方
ゴム材の寿命は一律ではなく、設置環境や使用頻度、負荷条件によって大きく異なります。
一般的な推奨交換年数は以下のとおりですが、これはあくまで目安と考え、実際には点検や運用状況を加味した柔軟な管理が必要です。
材質 | 推奨使用年数(目安) |
---|---|
NBR | 3〜5年 |
EPDM | 5〜8年(屋内)、3年(屋外) |
シリコン | 5〜10年(紫外線に強い) |
FKM(フッ素ゴム) | 7〜10年(耐熱・耐薬品環境) |
フジワラケミカルエンジニアリングの現場では、装置納入時に「交換推奨年数」のタグを貼付し、点検時にはOリングの状態を記録・蓄積。トラブル時には「前回交換時期」をすぐに遡れる管理表を活用するなど、計画的な予防保全を実践しています。
- 装置納入時に「交換推奨年数」のタグを貼付
- 点検時にOリングの状態を記録し、トレンドを蓄積
- 万が一のトラブル時に「前回交換時期」をすぐに追跡可能にする管理表を活用
フジワラケミカルにおける劣化への先回り対策
不具合発生後の対処ではなく、「不具合そのものを起こさない」ための予防設計・管理を重視しています。
- 視認性の高い構造:透明アクリル・PCカバー越しにOリングのひび割れ・変形を定期観察
- 使用履歴に応じた交換提案:脱着頻度が高い装置では、定期メンテ時に劣化前交換を推奨
- 素材グレードの統一化:複数の装置で同じ型のゴム部品を使うことで在庫管理を簡易化し、交換漏れを防止
さらに、分解・清掃が容易な構造設計や、Oリング位置の工夫、外部からの視認性向上など、プラスチック加工と寿命管理を一体化した「現場で本当に役立つ工夫」を追求しています。
こうした現場目線の対応で、ゴムの寿命リスクを最小限に抑え、長期的な品質維持・安定稼働を実現しています。
フジワラケミカルの技術応用:プラスチック加工と寿命管理の融合
フジワラケミカルでは、ゴム部品単体の品質や寿命管理にとどまらず、プラスチック加工のノウハウを活かした「交換しやすい構造設計」や「現場での点検・メンテナンス性向上」にも力を入れています。
たとえば、Oリングの位置決めがしやすい溝形状の工夫や、着脱方向を考慮した構造設計により、分解や清掃がスムーズに行えるよう配慮。さらに、透明なプラスチック部品による外部からの観察性向上や、方向指示ラベル、色付きOリングによる交換ミス防止といったアイデアも積極的に取り入れています。
また、部品ごとに毎回寸法誤差が出にくい刃物や冶具を選定し、組立精度のバラつきを抑えることで、ゴム部品の寿命を最大限引き出す設計・加工の両面から現場を支えています。
「プラスチック加工の視点からゴムの使いやすさをデザインする」
これはゴム製品メーカーとは異なる、フジワラケミカルならではの強みです。
フジワラケミカルでは、以下のような現場視点の工夫を積み重ねています。
- 分解・清掃が簡単な構造をプラスチック加工で実現
Oリング位置を固定しやすい溝形状や着脱方向の工夫を設計に反映 - ゴム部品の視認性・アクセス性の確保
透明部品による外部観察、方向指示ラベル、色付きOリングの活用で交換ミスを防止 - ゴムの「寿命管理」を見越した加工
毎回正確に収まるよう寸法誤差の出にくい刃物や冶具を選定
これらの工夫により、「使いやすさ」と「維持管理のしやすさ」の両立を実現し、ゴム部品の長寿命化と装置全体の信頼性向上に貢献しています。
まとめ:見逃さない管理が信頼性を支える
ゴム部品は目に見えないところで装置の安全・安定稼働を支える縁の下の力持ちです。
だからこそ、日常的な点検・記録・計画的な交換管理が、装置全体の信頼性や製品品質を守るための要となります。
フジワラケミカルエンジニアリングは、素材選定から設計・加工・運用後の保守まで、一貫して現場の課題解決に取り組み続けています。
今後も、ゴムとプラスチック両視点から最適なものづくりと安心をお届けしますので、どんなことでもお気軽にご相談ください。
フジワラケミカルの強み 〜プラスチック加工とゴム技術の融合〜
本コラムシリーズでは、ゴムに関する基礎知識・選定・設計・寿命管理という流れで実務に即した情報をお届けしました。
フジワラケミカルの現場では、これらのゴム部品は単体で使われるのではなく、プラスチック加工技術と一体となって活用されています。 実際に、現場で行っている主な工夫は以下の通りです。
- 透明アクリルやPCによる点検窓+Oリング構造:Oリングの見える化と組立性の両立
- PPやPVCなどの装置部品+EPDMシール:耐薬品性と軽量性を兼ね備えた設計
- 接着できない素材にはOリングで密封性を確保:機械加工とシール構造を融合
こうした「プラスチック × ゴム」の組み合わせは、単なる素材選定にとどまらず、装置全体のメンテナンス性・信頼性・安全性を高めるための重要な仕掛けです。
フジワラケミカルでは、樹脂加工・接着・溶接・曲げといった多様なプラスチック加工に、 最適なゴム材の提案と設計協力を組み合わせ、製品そのものではなく「使いやすさ」「維持しやすさ」まで提案するものづくりを目指しています。
今後も、こうした横断的な技術融合の視点で、現場からの気づきを発信してまいります。
ゴムとプラスチック加工シリーズ 一覧
ゴムとプラスチック部品の最適な組み合わせ設計や素材選定、Oリング溝設計、寿命管理まで、現場で役立つ知見を体系的に解説するシリーズです。構造設計からトラブル防止、長寿命化まで、プラスチック加工メーカーの視点で実践ノウハウをまとめています。
- 【ゴム×プラ①】機能性を最大化するプラスチック×ゴムの構造設計ノウハウ
ゴムとプラスチックの異素材組み合わせによる構造設計のポイントや、用途別の最適設計を解説します。 - 【ゴム×プラ②】ゴム材料選定術:失敗事例と用途別ポイントを徹底解説
トラブル事例をもとに、用途ごとのゴム材選定と現場で使えるチェックポイントを紹介します。 - 【ゴム×プラ③】プラスチック部品のOリング溝設計と密封性向上のポイント
Oリング溝の設計ノウハウや密封性・長寿命化のための現場テクニックを解説します。 - 【ゴム×プラ④】ゴムの経年劣化と寿命管理:適切な交換タイミングとは(このページ)
ゴム部品の劣化メカニズム、寿命管理、現場で役立つ予防保全のポイントを実践目線でまとめています。
※太字(このページ)表記が現在閲覧中の記事です。