静電気トラブルを防ぐ!帯電防止プラスチックの実測データ活用術と寿命管理のすべて
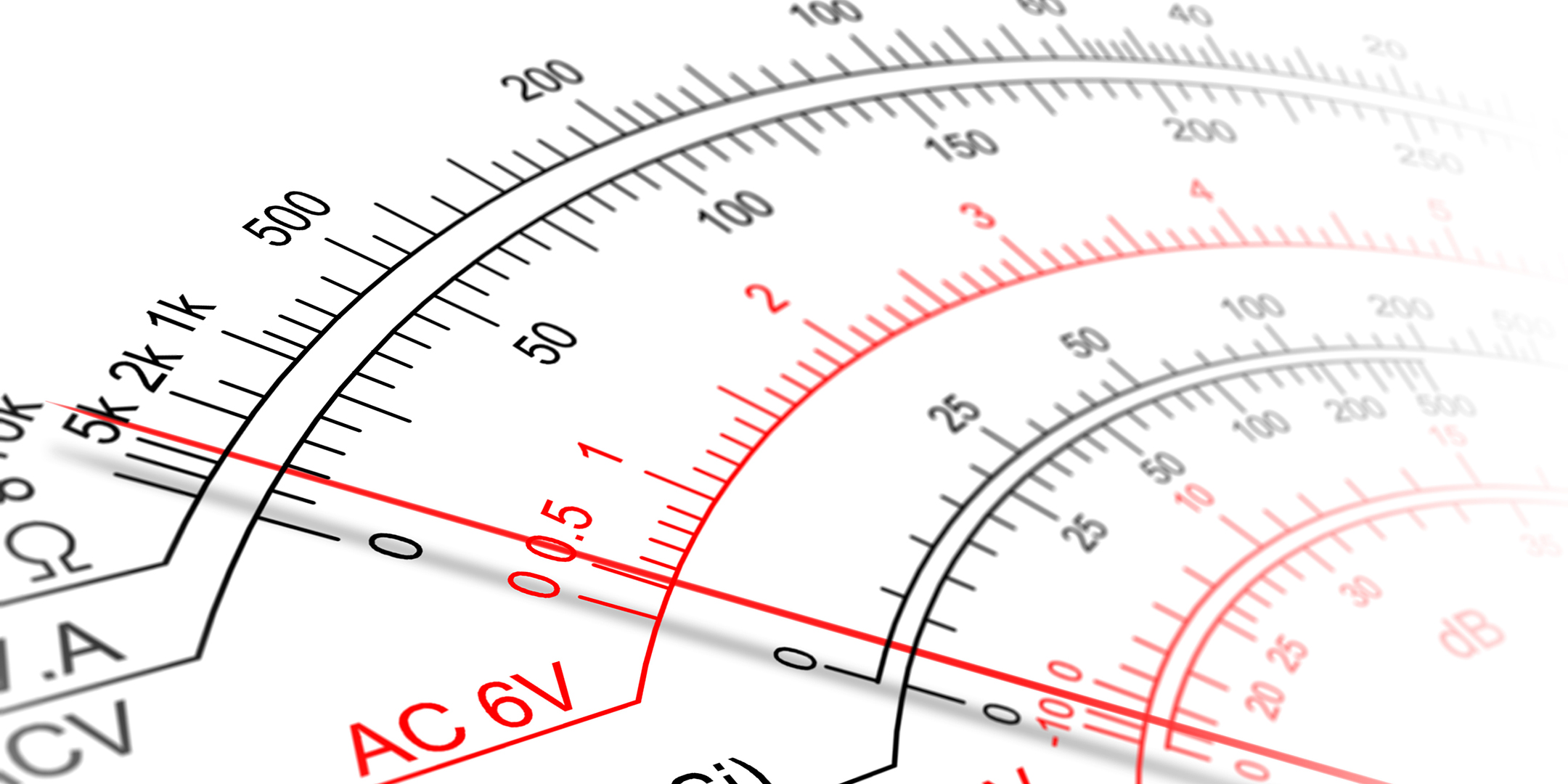
帯電防止プラスチックは、静電気対策として多くの現場で不可欠な存在です。とくに、電子部品や精密機器の製造現場、食品や医薬品の加工ラインなどでは、静電気によるトラブルや異物付着を防ぐため、帯電防止性能を持つプラスチックが広く活用されています。
しかし、その性能は永続的なものではなく、経年や環境要因で帯電防止性能が低下することが知られています。例えば、長期間の使用による摩耗やキズ、定期的な薬品洗浄、さらに紫外線や高温・多湿といった環境条件の変化は、プラスチック表面の抵抗値を徐々に変化させ、当初の帯電防止効果を損なう主な要因となります。
現場でのトラブル予防や安定稼働のためには、抵抗値の実測データに基づいたメンテナンスと寿命管理が重要です。単に「設置して終わり」ではなく、定期的な性能点検とデータの蓄積によって、帯電防止プラスチックを安全かつ有効に運用し続けることが求められています。本稿では、「各種材料の抵抗値」データを根拠に、帯電防止プラスチックの実践的な管理方法について詳しく解説します。
帯電防止プラスチック活用シリーズ 一覧
電子部品・クリーンルーム・精密機器製造現場などで求められる帯電防止プラスチックの基礎知識から、選定ポイント、実測データや寿命管理のノウハウまでを分かりやすく解説するシリーズです。
- 【帯電防止①】帯電防止プラスチックの種類・性能・導入効果:クリーンルームから電子部品まで
各種帯電防止プラスチックの特徴や用途、導入メリットを総合的に解説。静電気対策の基礎から最適素材選びのヒントまで紹介します。 - 【帯電防止②】静電気トラブルを防ぐ!帯電防止プラスチックの実測データ活用術と寿命管理のすべて(このページ)
帯電防止性能の測定・判定基準、劣化サインの見極め、現場での点検・管理フローなど、運用・保守に役立つ実践ノウハウを詳しく紹介します。
※太字(このページ)表記が現在閲覧中の記事です。
帯電防止性能の評価指標と基準値
帯電防止プラスチックの性能は、主に表面抵抗値(Ω)で評価されます。表面抵抗値は、材料表面の静電気をどれだけ効果的に逃がせるかを示す指標であり、帯電防止材の性能を「見える化」する上で最も信頼できるデータです。
実測データからは、以下の区分が実用上の目安となります。
- 帯電防止プラスチックの表面抵抗値
10⁶~10¹¹Ω:帯電防止性能が発揮される実用領域です。静電気の蓄積を抑え、現場で求められる帯電防止効果が十分に得られます。 - 絶縁体(一般プラスチック)
10¹²Ω以上:静電気が溜まりやすく、帯電防止効果はありません。埃や異物の付着、静電気障害が発生しやすくなります。
この抵抗値領域を実測で管理することが、現場の静電気トラブル予防に直結します。材料の選定や日常管理の際は、必ずこの評価基準に基づいて判断することが重要です。
実測データを活用した帯電防止プラスチックの性能点検
帯電防止プラスチックの寿命や性能劣化は、目視だけでは正確に把握できません。材料の状態を数値として「見える化」し、適切なタイミングで点検・メンテナンスを行うためには、実際に現場で抵抗値を測定することが重要です。定期的な測定・記録を通じて、性能変化の兆候をいち早く察知し、トラブルを未然に防ぐことができます。以下では、現場での測定方法や判定基準、性能劣化を示すサインについて具体的に解説します。
①抵抗値測定の進め方
現場では「スタティック・オネストメーター」等の表面抵抗計を使い、帯電防止材の実際の抵抗値を測定します。測定時には、清掃後の状態や湿度・温度にも注意を払い、できるだけ実際の使用条件に近い状態で測定することが望ましいです。
- 新品設置直後
- 半年ごと
- トラブル発生時
こうしたタイミングで定期点検を実施することで、性能の変化や劣化傾向をいち早く把握できます。
②実測値による判定例
実測した抵抗値は、その場で帯電防止プラスチックの状態を「数値」として評価できる確かな根拠となります。ここでは、実際の現場で得られたデータをもとに、どのように性能の良否や交換時期を判断するのか、具体的なケースで説明します。
- 例1:帯電防止プレート(使用初期)
実測抵抗値=10⁷Ω → 良好(帯電防止性能あり)
導入初期は、理想的な抵抗値が得られ、現場でも静電気トラブルが発生しにくい状態が保たれます。 - 例2:帯電防止プレート(使用3年目)
実測抵抗値=10¹¹Ω → 性能低下の傾向、異物付着増加も見られ、交換を検討
この段階では、目視でも異物付着が目立ったり、清掃がしにくくなる兆候が見られ始めます。
③性能劣化の要因と現場兆候
抵抗値の変化には必ず理由があります。帯電防止性能の劣化がどのような要因によって引き起こされるのか、また現場ではどのようなサインとして現れるのかを理解しておくことは、的確なメンテナンスや早期交換の判断に役立ちます。以下に、主な劣化要因と現場でよく見られる兆候をまとめます。
- 摩耗・キズの増加
摩耗部の抵抗値を実測すると、局所的に高抵抗化(例:10¹²Ω超)する場合があり、部分的な帯電防止機能の低下が起こることがあります。 - 薬品や洗剤による劣化
アルカリ・アルコール洗浄後に、抵抗値が帯電防止域から外れるケースが現場で確認されています。薬品の選定や洗浄方法にも注意が必要です。 - 紫外線・熱環境
屋外や高温箇所では劣化が早く、定期的な実測が必須となります。急激な性能低下が起きやすいため、交換サイクルを短めに設定するのが無難です。
帯電防止プラスチックの寿命管理ポイントと交換サイクル
帯電防止プラスチックの管理において、最も見落とされがちなのが「いつ交換するべきか」という具体的な寿命管理です。性能劣化が進んでからでは遅く、現場の安定運用と品質維持には、実測データに基づく計画的な管理が欠かせません。この章では、トラブルを未然に防ぐための交換サイクルの考え方や、現場で役立つ管理フローについて解説します。
①「使いっぱなし」から「予防交換」へ
実測抵抗値が10¹¹Ωを超えたら性能低下の兆候と考え、機能不全や異物付着トラブルが発生する前に計画的な交換を推奨します。現場では「まだ使えそう」と判断しがちですが、帯電防止材は「使いっぱなし」を避け、トラブルを未然に防ぐための予防的なメンテナンスが重要です。
設置から1~3年での交換が目安となりますが、これはあくまで一般的な指標です。実際には現場条件や使用頻度によって大きく左右されるため、実測データでの管理が最優先となります。
②定期点検フローの例
日常的なメンテナンスや性能管理を効果的に行うためには、現場で実践できる具体的な点検フローを確立しておくことが不可欠です。ここでは、抵抗値の測定から記録・交換判断まで、現場運用の参考となる基本的な流れを紹介します。
新品の帯電防止プラスチックを設置したタイミングで、必ず表面抵抗値を測定し、その数値を記録しておきます。これが後々の性能比較や劣化判定の「基準データ」となり、今後の管理やトラブル対応の出発点となります。
定期的に(目安として半年ごと)抵抗値を測定し、その結果を継続して記録します。こうしてデータを積み重ねていくことで、性能変化の傾向や劣化の進行具合を客観的に把握できるようになります。
実測値が許容値(例:10¹¹Ω)を超えた場合、帯電防止性能の低下が明らかです。この時点で、近い将来の交換スケジュールを計画し、現場の稼働状況や生産計画も考慮しながら、トラブルが起こる前に予防的な交換を進めます。
抵抗値の数値だけでなく、材料表面の見た目や異物の付着状況など、目視点検もあわせて実施します。清掃しにくくなった、汚れが落ちにくい、光沢や色味が変わったなどの変化は、帯電防止性能の劣化サインとなることが多いため、見逃さず記録・報告することが大切です。
こうした定期点検とデータ蓄積により、性能劣化の予兆を的確につかみ、計画的な交換や対策を講じることができます。
現場改善の実例
ここでは、帯電防止プラスチックの定期的な点検や実測データの活用が、実際にどのような現場改善につながったのか、具体的な導入事例を紹介します。数値による管理や計画的なメンテナンスが、現場でのトラブル削減や品質向上に直結することを実感できるはずです。
ケース1:食品工場の搬送カバー
設置2年で実測抵抗値が10¹¹Ωを超え、異物付着が目立つようになりました。現場では清掃の手間も増え、異物混入クレームのリスクも高まっていましたが、即時交換によりクレーム減・清掃負担軽減を実現。
このように、抵抗値と現場状況の両面から判断し、早めに対処することで品質維持と業務効率向上を同時に達成できます。
ケース2:電子部品ラインのトレー
半年ごとの抵抗値実測で変化を管理し、10¹¹Ωに達する前に交換を実施。静電破壊不良率の大幅削減につながったという実績があります。
データに基づく寿命管理を徹底することで、不良発生率の低減や安定した生産体制の確立が可能となります。
6. まとめ
帯電防止プラスチックの性能管理には、表面抵抗値の実測データを基準とした点検が不可欠です。定期的な測定・記録により帯電防止域(10⁶~10¹¹Ω)を維持できているかどうかを“見える化”し、「使いっぱなし」から「計画的な交換」へシフトすることが現場の安定運用と品質確保のカギとなります。
劣化の兆候や実測値の変化を見逃さず、最適なタイミングで交換を実施しましょう。現場においては、抵抗値という「客観的根拠」に基づいた管理体制の構築が、静電気トラブルのない安心・安全なものづくり現場につながります。
帯電防止プラスチック活用シリーズ 一覧
電子部品・クリーンルーム・精密機器製造現場などで求められる帯電防止プラスチックの基礎知識から、選定ポイント、実測データや寿命管理のノウハウまでを分かりやすく解説するシリーズです。
- 【帯電防止①】帯電防止プラスチックの種類・性能・導入効果:クリーンルームから電子部品まで
各種帯電防止プラスチックの特徴や用途、導入メリットを総合的に解説。静電気対策の基礎から最適素材選びのヒントまで紹介します。 - 【帯電防止②】静電気トラブルを防ぐ!帯電防止プラスチックの実測データ活用術と寿命管理のすべて(このページ)
帯電防止性能の測定・判定基準、劣化サインの見極め、現場での点検・管理フローなど、運用・保守に役立つ実践ノウハウを詳しく紹介します。
※太字(このページ)表記が現在閲覧中の記事です。