【プラスチック加工の基礎②】NCルーター技術による高精度プラスチック板加工の実現
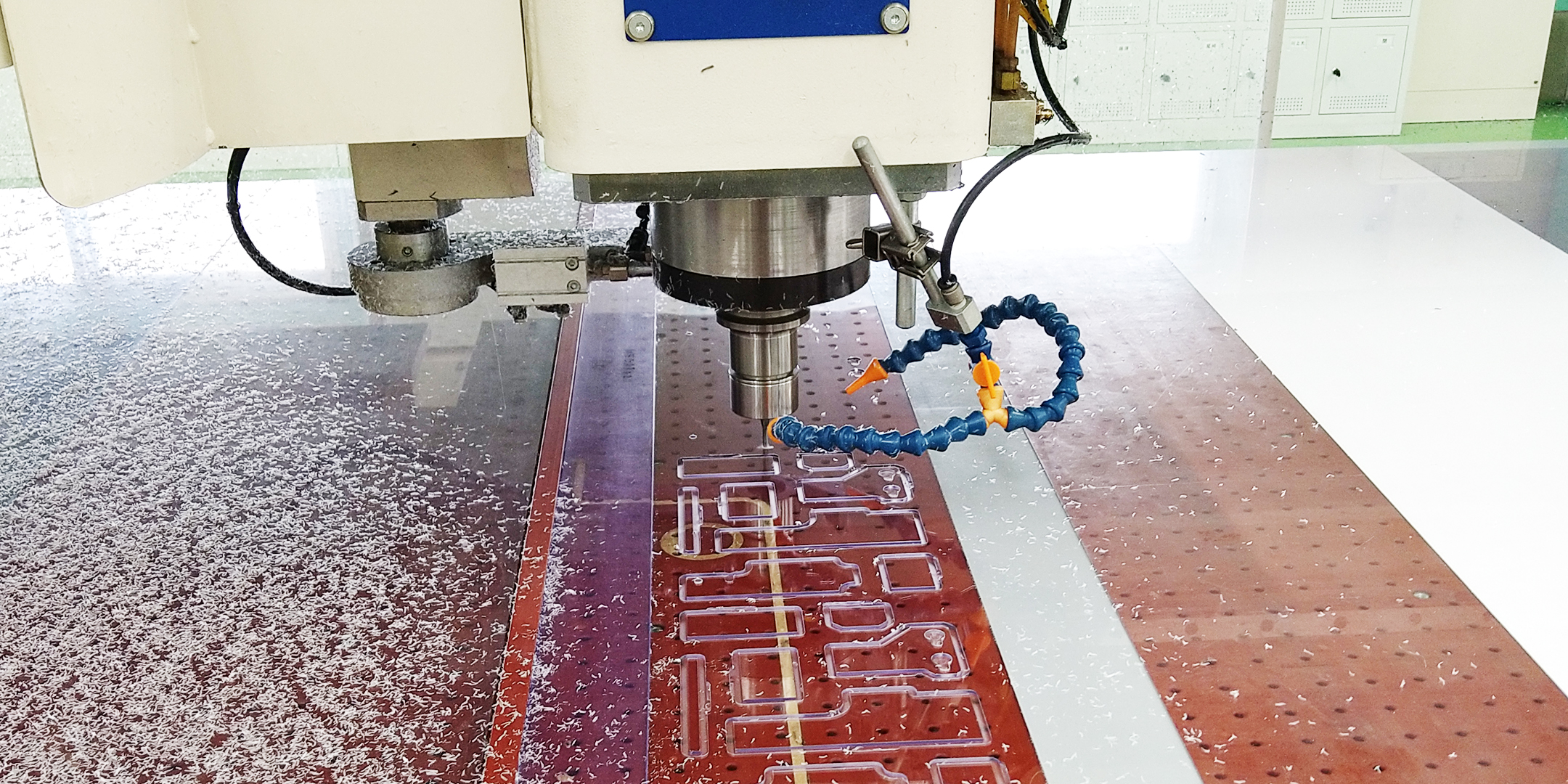
プラスチック加工では、素材ごとの特性を正確に把握し、最適な加工方法を選ぶことが極めて重要です。たとえば、金属加工で一般的なレーザー加工機は、高温のレーザービームを用いて素材を瞬時に溶融・気化させることで精密な切断を実現します。しかし、プラスチックは熱に対して非常に敏感なため、同じ手法を用いると、過度な加熱によって素材が溶けたり、焦げたり、変形したりするリスクが高まります。これにより、安定した高精度加工の実現が難しくなります。
このコラムでは、まずレーザー加工機の限界から見えてくるプラスチック加工の課題を整理します。さらに、NCルーター技術を最適な運用方法で活用することで、これらの問題がどのように解決できるかを、具体的な加工工程や品質管理のポイントを交えて解説します。最終的には、高精度なプラスチック加工を実現するための技術的アプローチとそのメリットを理解していただける内容となっています。
プラスチック加工の基礎シリーズ 一覧
プラスチック切削加工の基本から、NCルーターやマシニングセンタ、NC旋盤、木工機械の応用まで、初学者にも分かりやすくプラスチック加工の基礎を体系的に解説するシリーズです。現場の課題解決や技術選定にも役立つ実践的な内容をまとめています。
- 【基礎①】基礎からわかる!プラスチック切削加工の4つのポイント
プラスチック切削加工の基本と注意点を徹底解説。初学者にもわかりやすい入門ガイドです。 - 【基礎②】NCルーター技術による高精度プラスチック板加工の実現(このページ)
板材加工の現場改善に役立つNCルーターの活用法と事例を紹介します。 - 【基礎③】金属と何が違う?プラスチックのマシニングセンタ加工
金属加工と異なるプラスチック専用マシニング技術の要点を解説します。 - 【基礎④】プラスチックNC旋盤加工:課題解決と高品質実現の技術革新
NC旋盤ならではの課題とその解決策、高品質加工へのアプローチを詳述します。 - 【基礎⑤】木工機械活用術:柔軟で高効率なプラスチック加工の実現
木工技術の応用による多品種・小ロットのプラスチック加工事例を紹介します。
※太字(このページ)表記が現在閲覧中の記事です。
レーザー加工機の限界とプラスチック加工の課題
レーザー加工機は高温を利用して金属を切断するため、プラスチックのような熱に弱い素材では、局所的な加熱により材料が溶融・焦げ、寸法の安定性や仕上がり精度に大きな影響を及ぼします。さらに、一部のプラスチックは加熱時に有害ガスを発生させるため、作業環境の安全性も確保できません。
熱影響による変形や溶融の課題
レーザー加工による高温は、プラスチックに深刻な熱影響を及ぼします。
これらの熱影響が、レーザー加工機をプラスチック板加工に適さない理由となっています。
レーザー加工機で不可能な加工
また、プラスチック加工において、レーザー加工機は以下の加工に対して実用性が低くなります。
NCルーターの優位性:高精度加工の実現
プラスチック板加工には、NCルーターが最適な選択肢です。その理由は以下の通りです。
- 溝加工・彫刻加工:段付き加工やザグリ加工など、細かな溝加工や彫刻加工が可能です。
- 曲線カット・複雑形状加工:CAMソフトと組み合わせることで、3D形状を含む曲線や複雑なデザインの加工にも対応できます。
- タップ加工・皿モミ加工:切削工具の変更により、金属加工で求められるような精密なタップ加工や皿モミ加工も実現可能です。
- エンドミル:細かい加工や深い穴あけに適しており、精密な部品加工が可能です。
- Vビット:彫刻加工により、繊細なデザインや文字彫りが実現できます。
- ボールエンドミル:3D曲面加工により、複雑な立体形状の仕上げが可能です。
- ダイヤモンドカッター:高硬度の材料に対しても優れた切削性能を発揮し、難加工材の処理が行えます。
NCルーターの加工工程と品質管理のポイント
NCルーターを用いたプラスチック板の加工では、精度の高い切削を実現するために各工程で適切な管理が求められます。加工前の準備から仕上げまで、一貫した品質管理を行うことで、安定した製品を作ることが可能になります。以下に、各工程の概要と品質管理のポイントを説明します。
NCルーターを使用する際の基本的な加工工程と品質管理のポイントを紹介します。
加工を開始する前に、使用するプラスチック板の品質を確認し、仕様に適合していることを保証する必要があります。材質や板厚のばらつきを抑えることで、安定した加工精度を確保できます。
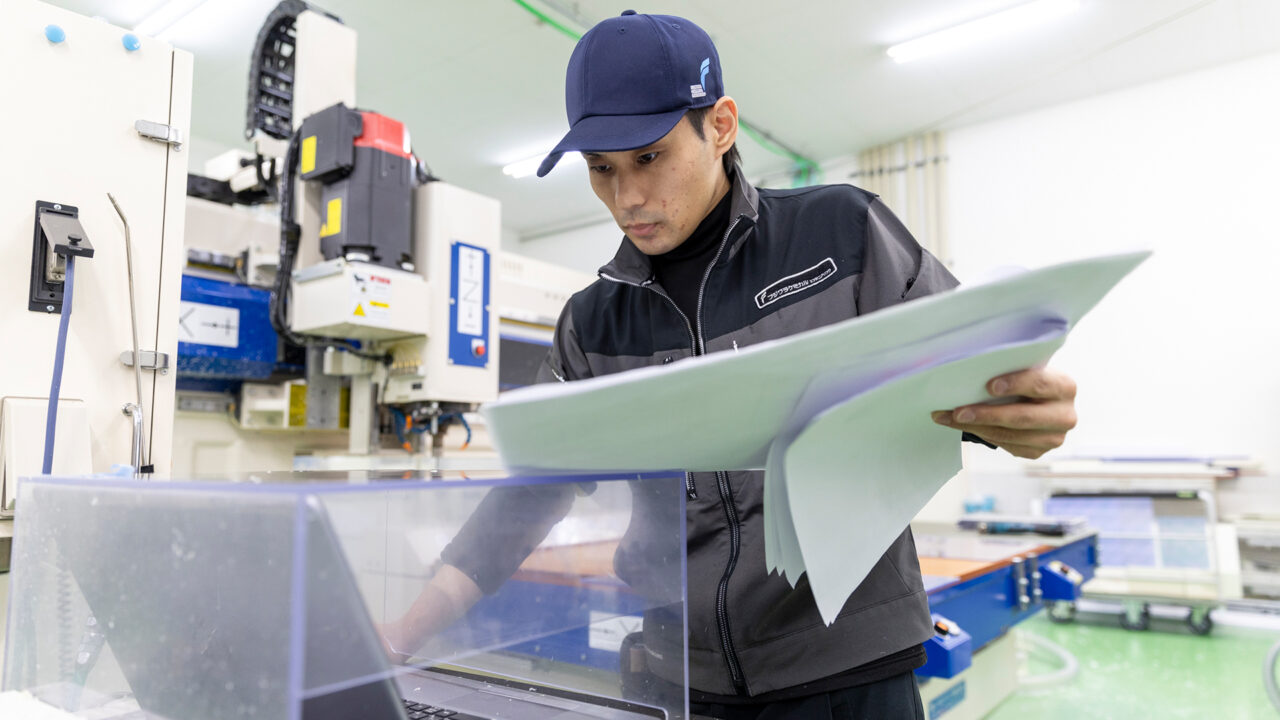
- 管理項目:使用する板材の厚みや材質が仕様に合っているかを確認。
- 管理基準:NC加工仕様書や図面と一致していること。
- 測定方法:ノギスやコンベックス、直尺を使用。
設定された加工データに基づき、NCルーターが回転工具を用いて材料を切削します。工具の種類や回転速度、送り速度を適切に設定することで、バリを抑えた高品質な仕上がりが得られます。
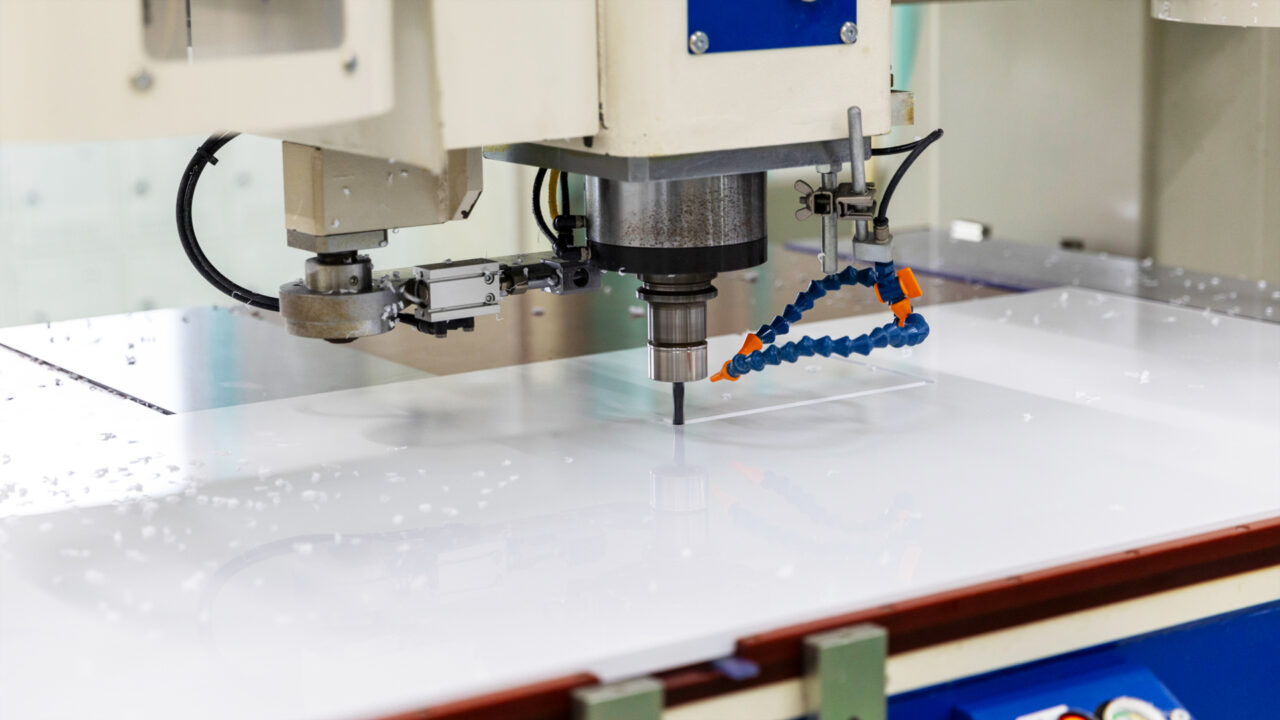
- 管理項目:切削形状が図面と一致しているか。
- 管理基準:±0.1mm以内の寸法公差。
- 測定方法:ノギス、デジタルマイクロメーターなど。公差外の部品は即時報告し、加工条件の見直しを実施。
切削加工後、バリ取りや表面仕上げを行い、最終製品としての品質を確保します。傷や欠けがないかを目視で確認し、必要に応じて追加の処理を施します。
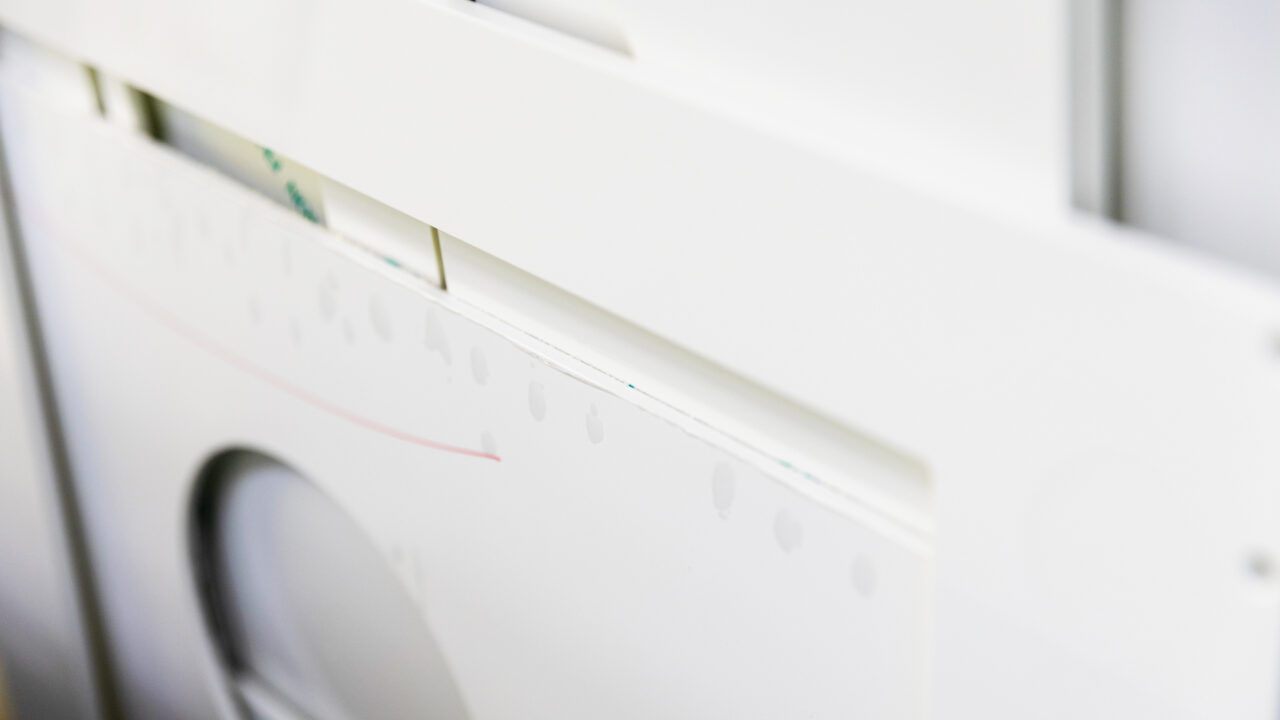
- 管理項目:バリ取りや表面の仕上がり確認。
- 管理基準:バリなし、傷や欠けのない状態。
- 測定方法:目視検査、指触確認。
NCルーター導入時に考慮すべき要点
NCルーターを導入する際には、レーザー加工機とは異なる特性を理解し、適切な運用方法を検討することが重要です。特に、材料の固定方法、切削粉の処理、切削条件の最適化、加工範囲の違いなどを考慮する必要があります。以下のポイントを押さえることで、効率的で高品質な加工が可能になります。
材料固定方法の違い
レーザー加工機では材料を固定せずに加工できますが、NCルーターでは加工中のズレを防ぐために適切な固定が必要です。主に真空吸着テーブルや両面テープを活用し、材料を安定させます。
- 真空吸着テーブルは大型の板材の固定に適していますが、貫通加工ができないため、0.2mm程度残して切削し、後でカッターで仕上げます。
- 両面テープは小型のワークの固定に適しており、専用のクランプ治具を使用せずに加工が可能です。
切削粉の処理
NCルーターでは機械的に材料を削るため、レーザー加工と異なり切削粉が大量に発生します。これを適切に処理しないと、加工精度の低下や機械の故障につながるため、以下の対策が必要です。
- 集塵装置の導入により、作業環境の清潔を保つ。
- 適切な排出経路の確保で、切削粉が機械内部に蓄積するのを防ぐ。
切削条件の最適化
材料ごとに最適な切削条件を設定することで、加工品質が向上し、工具寿命を延ばすことができます。
- 送り速度や回転数を適切に調整し、バリや変形を最小限に抑える。
- 加工対象の材質に適したツールを選定し、仕上げ精度を向上させる。
NCルーターとマシニングセンタの違い
NCルーターはマシニングセンタと異なり、使用できる刃物の本数が限られるため、ネジ加工や細かい加工は手作業になることが多くなります。
- タップ加工やザグリ加工が必要な場合は、追加の手作業が発生する。
- 工具交換の頻度が異なるため、加工プロセスの見直しが必要になる。
まとめ
プラスチック板加工では、熱影響が極力抑えられるNCルーターが主流となり、機械的な切削により高精度な仕上がりが実現されています。工具の交換によって多様な加工に対応できる点や、接合部の少ない滑らかな成形が製品の強度、美観、清掃性の向上に寄与するなど、NCルーターならではのメリットが際立ちます。
一方、レーザー加工機やマシニングセンタとの違いも明確です。例えば、材料の固定方法、切削粉の処理、仕上げ工程など、各機器にはそれぞれ固有の注意点があり、特に真空吸着テーブルを用いる場合は、貫通加工の難しさやネジ加工での手作業が必要になることも理解しておくべき重要なポイントです。
また、近年、金属加工現場でも製品の軽量化や高機能化、デザイン性向上のためにプラスチック部品の活用が進んでおり、NCルーターによる加工需要はますます高まっています。NCルーターを最大限に活用するには、各工程での品質管理と最適な条件設定を徹底することが不可欠です。これらの知識と工夫が、高品質かつ効率的なプラスチック加工を実現し、製品の競争力強化につながります。
フジワラケミカルエンジニアリングでは、お客様の仕様や用途に応じ、円筒曲げ、R曲げ、V溝曲げなど、多彩な加工に柔軟に対応できる体制を整えております。ぜひ、当社のNCルーター運用技術による高精度加工をご体験ください。
プラスチック加工の基礎シリーズ 一覧
プラスチック切削加工の基本から、NCルーターやマシニングセンタ、NC旋盤、木工機械の応用まで、初学者にも分かりやすくプラスチック加工の基礎を体系的に解説するシリーズです。現場の課題解決や技術選定にも役立つ実践的な内容をまとめています。
- 【基礎①】基礎からわかる!プラスチック切削加工の4つのポイント
プラスチック切削加工の基本と注意点を徹底解説。初学者にもわかりやすい入門ガイドです。 - 【基礎②】NCルーター技術による高精度プラスチック板加工の実現(このページ)
板材加工の現場改善に役立つNCルーターの活用法と事例を紹介します。 - 【基礎③】金属と何が違う?プラスチックのマシニングセンタ加工
金属加工と異なるプラスチック専用マシニング技術の要点を解説します。 - 【基礎④】プラスチックNC旋盤加工:課題解決と高品質実現の技術革新
NC旋盤ならではの課題とその解決策、高品質加工へのアプローチを詳述します。 - 【基礎⑤】木工機械活用術:柔軟で高効率なプラスチック加工の実現
木工技術の応用による多品種・小ロットのプラスチック加工事例を紹介します。
※太字(このページ)表記が現在閲覧中の記事です。