【ゴムとプラスチック加工①】機能性を最大化するプラスチック×ゴムの構造設計ノウハウ
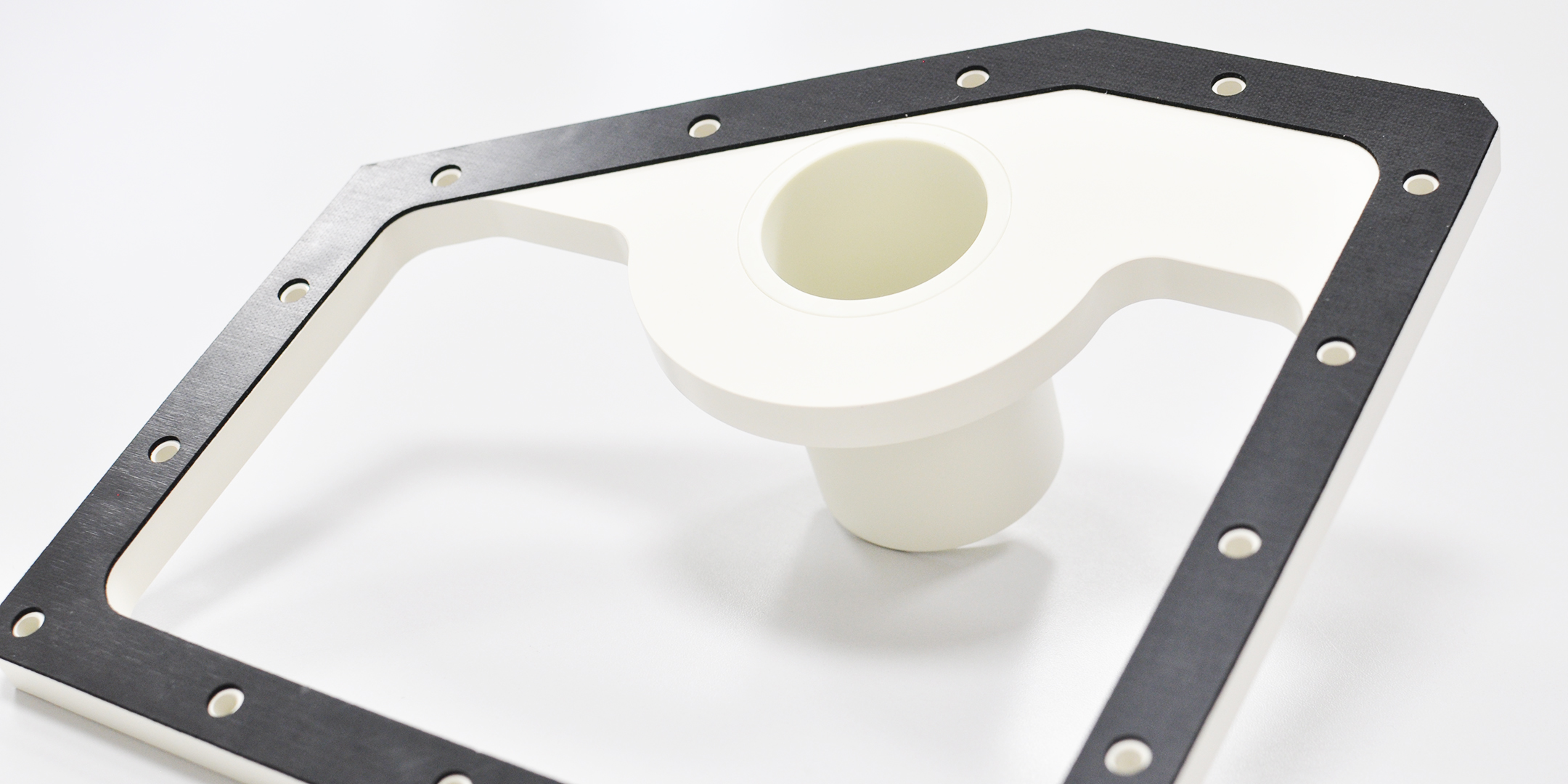
プラスチック製品が高機能化・複雑化する現代の製造現場において、それを支えるゴム材料の選定と加工技術の重要性がますます高まっています。プラスチック部品単体では実現が難しい「密封性」「緩衝性」「取り付けやすさ」などの特性を、ゴム材料が補完することで製品全体の性能や信頼性が大きく向上します。
とくに近年は、プラスチックとゴムの特性を活かした構造設計や、Oリングなどによる高い水密性を実現する設計技術が、多様な産業装置や製品において不可欠となっています。ゴムの適切な選定・設計が、水漏れ防止や衛生管理、長寿命化といった高度な現場要求に応えるカギとなっています。
特にゴムは、種類ごとに耐油性や耐薬品性、耐熱性といった異なる特性を持ちます。これらの特性をプラスチック素材との組み合わせで活用することで、装置のトラブル防止や長期間の安定稼働が実現できます。
今回は、ゴムの主要種類の特性を詳しく解説するとともに、プラスチック×ゴムの構造設計や水密設計の実務的ポイントを、プラスチック加工会社ならではの視点からご紹介します。
ゴムとプラスチック加工シリーズ 一覧
ゴムとプラスチック部品の最適な組み合わせ設計や素材選定、Oリング溝設計、寿命管理まで、現場で役立つ知見を体系的に解説するシリーズです。構造設計からトラブル防止、長寿命化まで、プラスチック加工メーカーの視点で実践ノウハウをまとめています。
- 【ゴム×プラ①】機能性を最大化するプラスチック×ゴムの構造設計ノウハウ(このページ)
ゴムとプラスチックの異素材組み合わせによる構造設計のポイントや、用途別の最適設計を解説します。 - 【ゴム×プラ②】ゴム材料選定術:失敗事例と用途別ポイントを徹底解説
トラブル事例をもとに、用途ごとのゴム材選定と現場で使えるチェックポイントを紹介します。 - 【ゴム×プラ③】プラスチック部品のOリング溝設計と密封性向上のポイント
Oリング溝の設計ノウハウや密封性・長寿命化のための現場テクニックを解説します。 - 【ゴム×プラ④】ゴムの経年劣化と寿命管理:適切な交換タイミングとは
ゴム部品の劣化メカニズム、寿命管理、現場で役立つ予防保全のポイントを実践目線でまとめています。
※太字(このページ)表記が現在閲覧中の記事です。
ゴム材料がプラスチック製品にもたらす効果
ゴム材料を適切に活用することで、プラスチック製品の弱点を補い、密封性や耐衝撃性、柔軟な取り付け性などの付加価値を加えることができます。とくに、プラスチック単体では難しい「密封構造」や「脱着性」「衛生対応」などの実現において、ゴムは重要な役割を果たします。
ただし、ゴムにはNBR・EPDM・シリコンゴム・フッ素ゴム(FKM)など多様な種類があり、それぞれ得意とする分野や特徴が異なります。製品の用途や使用環境に応じて、最適なゴム材料を選定することが、性能や信頼性を大きく左右します。適切な選定を誤ると、密封不良や劣化、メンテナンス性の低下といったトラブルの原因となるため、材料選びは極めて重要な工程です。
フジワラケミカルエンジニアリングでは、プラスチック加工技術を基軸に、耐熱性・耐薬品性・加工性などの要求特性を十分に考慮した上で、ゴム部品を単なる付属品ではなく「構造の一部」として設計段階から適切に選定・最適化することを重視しています。こうしたアプローチによって、視認性・密封性・メンテナンス性といった様々な現場ニーズに柔軟に対応しています。
記事後半では、プラスチック×ゴムの現場で活きる設計・加工の工夫や具体例も詳しく解説します。
ゴム材料選定の基礎と考え方
ゴム材料を選ぶ際には、単にプラスチック部品との「素材の相性」だけでなく、使用環境や求められる機能、コストや加工性といった多角的な視点からの検討が不可欠です。
まず重要なのは、使用環境の把握です。温度条件(常温、高温、低温)、湿度、薬品の有無、設置場所が屋内か屋外かなど、現場ごとにゴムが置かれる環境が大きく異なります。例えば、高温環境で使用する場合はシリコンゴム、薬品に晒される場合はフッ素ゴム(FKM)やEPDMなど、環境に適した材質選びが必要です。
次に、必要性能の明確化が重要です。ゴム部品には密封性、耐摩耗性、絶縁性、柔軟性、復元性など、多様な機能が求められます。Oリングであれば「気密性」や「圧縮変形に対する耐久性」、パッキンであれば「長期耐久性」や「薬品耐性」といった、目的ごとの必要機能を整理したうえで、性能面で不足のない材質を選びます。
さらに、加工性やコスト・量産性も実際の選定においては無視できません。たとえば同じ耐熱性があっても、成形方法によっては納期やコストに大きな差が出る場合があります。量産性が重視される場合には、安定供給やコストパフォーマンスも重要な判断軸です。
また、プラスチックとの組み合わせによる注意点も見逃せません。たとえば、アクリルやポリカーボネートなどの透明樹脂を使う場合には、ゴムとの密着性や加工精度が特に重要になります。フッ素樹脂(PTFE)やPOM(ポリアセタール)のように滑りやすい素材の場合は、気密性や摩耗への配慮が不可欠です。こうした異種材料との組み合わせでは、実際の現場でテストを行い、最適な仕様を見極めることが推奨されます。
このように、「使う環境」「求める機能」「コスト・加工性」「異種素材との相性」という複数の観点から総合的に判断することが、失敗しないゴム材料選定の基本です。
- 使用環境(温度、湿度、薬品、屋内外など)を正確に把握する
- 必要な機能(密封性、耐摩耗性、柔軟性など)を明確にする
- 加工方法やコスト、量産性も事前に検討する
- プラスチック素材との密着性や摩耗への配慮が必要か確認する
- 実際の現場条件でテスト・検証を行う
- 各ゴム種の特性・長所短所を整理し、最適な組み合わせを選定する
よく使われるゴムの種類と特徴
ゴム素材は一見どれも似たように見えますが、実際にはそれぞれ明確な特性の違いがあります。その違いを理解し、適材適所で使用することが、装置の安定稼働と長寿命に直結します。
たとえば、油圧装置にEPDMを使用すると、膨潤して破損する恐れがあります。反対に、水処理装置にNBRを使えば、長期間の耐久性が得られないこともあります。このように、「正しい材質選定」は、密封不良や事故を未然に防ぐ第一歩です。
ゴム種 | 特徴 | 主な用途例 |
---|---|---|
NBR(ニトリル) | 耐油性に優れるが耐候性はやや弱い | 油圧装置、一般機械 |
EPDM | 耐候性・耐水性・耐アルカリ性に優れる | 屋外装置、水処理関連 |
シリコン | 高温耐性・柔軟性・無毒性 | 食品・医療分野、スチーム環境 |
FKM(フッ素ゴム) | 耐熱・耐薬品・耐油性が非常に高い | 化学装置、クリーン装置 |
CR(クロロプレン) | バランス型。耐候性・耐油性・難燃性を持つ | 汎用機器、電気絶縁用途 |
天然ゴム | 摩擦係数が高く伸びが良いが、耐薬品性・耐候性に劣る | 振動吸収、ローラーなど |
ゴム選定で重要なポイント
実際の現場でゴム材料を選定する際には、カタログスペックや理論だけでは判断できない「実務的な注意点」が数多く存在します。ここでは、現場でよくある選定ミスや、見落としがちな具体的な観点を詳しく紹介します。
たとえば、油圧装置にEPDM(耐油性が低いゴム)を使用してしまい、ゴムが膨潤して破損したというトラブルは現場で非常によく見られます。逆に、水処理装置でNBR(耐油性は高いが耐水性や耐薬品性は低め)を使い、長期的な耐久性に問題が生じたケースもあります。高温域でシリコン以外のゴムを選び、短期間で硬化やひび割れが起こるなど、適材適所を誤ることで重大な機械トラブルにつながります。
また、食品・医療分野では衛生基準や法規制(例:FDA適合、食品衛生法適合など)を満たすことが必須条件となります。これらを軽視して一般グレードのゴムを使ってしまうと、納入後にNGとなり大きな手戻りやクレームにつながる恐れがあります。
実際の選定時には、以下の観点を漏れなくチェックすることが肝心です。
- 使用温度範囲(常温、高温、低温)
- 接触する液体や気体の種類(油、水、薬品、溶剤など)
- 摩耗や繰返し圧縮、動的な変形の有無
- 屋内外の設置場所(紫外線・オゾンへの曝露有無)
- 法規制や衛生基準(FDA、食品衛生法、RoHS等)
選定ミスが起きると、たとえば以下のような問題が発生します。
- 油に弱いEPDMを使ってOリングが膨潤・破損
- 高温域でシリコン以外のゴムが硬化・ひび割れ
- 食品装置に非衛生グレードのゴムを使用し、納入先でNGに
- 滑りやすい素材(PTFE・POMなど)と組み合わせて気密不良や摩耗加速が発生
こうした失敗を防ぐためには、材質ごとの物理特性・化学的耐性をよく理解し、現場の使用条件を細かくヒアリング・確認することが重要です。特に新しい装置設計や異種素材との組み合わせを行う場合は、試作・検証のプロセスを省略しないことが成功のポイントです。
「わかったつもり」の選定ではなく、「現場に根差した材料選び」を徹底することで、長期的な装置の信頼性と安全性が担保されます。
機能性を高めるプラスチック×ゴムの構造設計
プラスチックとゴムの組み合わせは、単なる素材の選択を超え、設計段階から両者を最適に融合することで大きな機能向上につながります。フジワラケミカルエンジニアリングでは、下記のような構造設計によって、単独素材では得られない価値を生み出しています。
- 衛生性を追求した一体型設計
食品・医療機器では、異物混入リスクや洗浄性を重視し、食品適合グレードのゴムとプラスチックを一体化。段差や隙間を極力なくすことで、異物や汚れの蓄積を防止し、衛生管理やメンテナンス性を向上しています。 - 脱着性・交換性を考慮した構造設計
Oリングやパッキンなどゴム部品を用いることで、装置の定期点検や部品交換時に「分解・再組立てが簡単」「消耗部品の交換が容易」といったメリットを実現。製品の長寿命化やユーザーの負担軽減にもつながっています。 - プラスチック部品とゴムの最適配置
密封・緩衝・絶縁など部位ごとの用途に合わせてゴムの配置を最適化。必要最小限の使用でコストや重量のバランスもとり、設計自由度と経済性の両立を図っています。
こうした構造設計ノウハウは、「量産性」や「コストダウン」「特殊環境対応」など多様な現場課題の解決にもつながっています。
プラスチックとゴムによる水密設計
水や液体の漏れを確実に防ぐ「水密構造」は、プラスチックとゴムの設計・加工技術の真価が問われる分野です。当社では透明樹脂(アクリル・ポリカーボネート等)とOリングを組み合わせた水密設計で、多様な現場ニーズに対応しています。
- Oリング溝の高精度加工
透明窓やカバー部にOリング溝を微細公差で加工し、気密性・水密性と視認性を両立。ゴム材の選定から加工法まで一貫管理し、漏れ・劣化・視界不良などのリスクを最小化します。 - 溶接・接着を用いない密封設計
耐薬品性や熱変形の懸念から溶接・接着が難しい場面でも、Oリング等のゴム部品で機械的に着脱できる密封構造を採用。装置メンテナンス性や現場交換作業の効率化にも寄与しています。 - 現場ニーズに合わせた材料・寸法最適化
耐薬品性・耐熱性など使用環境や洗浄頻度に応じて、ゴム種(例:FKM、EPDM等)・断面寸法・圧縮率を設計段階で最適化。現場ヒアリングや実地検証を重ねて、信頼性の高い水密構造を実現しています。
これらの取り組みにより、製品の信頼性向上だけでなく、ユーザー現場の作業効率や長期的なコスト低減にも大きく貢献しています。
まとめ
プラスチックとゴムのハイブリッド設計は、単なる部材の組み合わせにとどまらず、「機能性」「衛生性」「耐久性」など装置全体のパフォーマンスを根本から底上げする要素です。
フジワラケミカルエンジニアリングは、長年にわたり透明樹脂加工とゴム活用の現場経験を蓄積し、食品・医療・産業用装置など多様な分野で“最適解”を提案してきました。
今後も、お客様のニーズや現場課題に応じて、設計・選定・加工まで一貫したサポートを行い、「信頼性」と「現場の使いやすさ」を両立するプラスチック×ゴム技術を追求してまいります。
ゴムとプラスチック加工シリーズ 一覧
ゴムとプラスチック部品の最適な組み合わせ設計や素材選定、Oリング溝設計、寿命管理まで、現場で役立つ知見を体系的に解説するシリーズです。構造設計からトラブル防止、長寿命化まで、プラスチック加工メーカーの視点で実践ノウハウをまとめています。
- 【ゴム×プラ①】機能性を最大化するプラスチック×ゴムの構造設計ノウハウ(このページ)
ゴムとプラスチックの異素材組み合わせによる構造設計のポイントや、用途別の最適設計を解説します。 - 【ゴム×プラ②】ゴム材料選定術:失敗事例と用途別ポイントを徹底解説
トラブル事例をもとに、用途ごとのゴム材選定と現場で使えるチェックポイントを紹介します。 - 【ゴム×プラ③】プラスチック部品のOリング溝設計と密封性向上のポイント
Oリング溝の設計ノウハウや密封性・長寿命化のための現場テクニックを解説します。 - 【ゴム×プラ④】ゴムの経年劣化と寿命管理:適切な交換タイミングとは
ゴム部品の劣化メカニズム、寿命管理、現場で役立つ予防保全のポイントを実践目線でまとめています。
※太字(このページ)表記が現在閲覧中の記事です。