進化するPP溶接技術と大型構造物への挑戦:プラスチック溶接で円筒タンクやシンクに対応
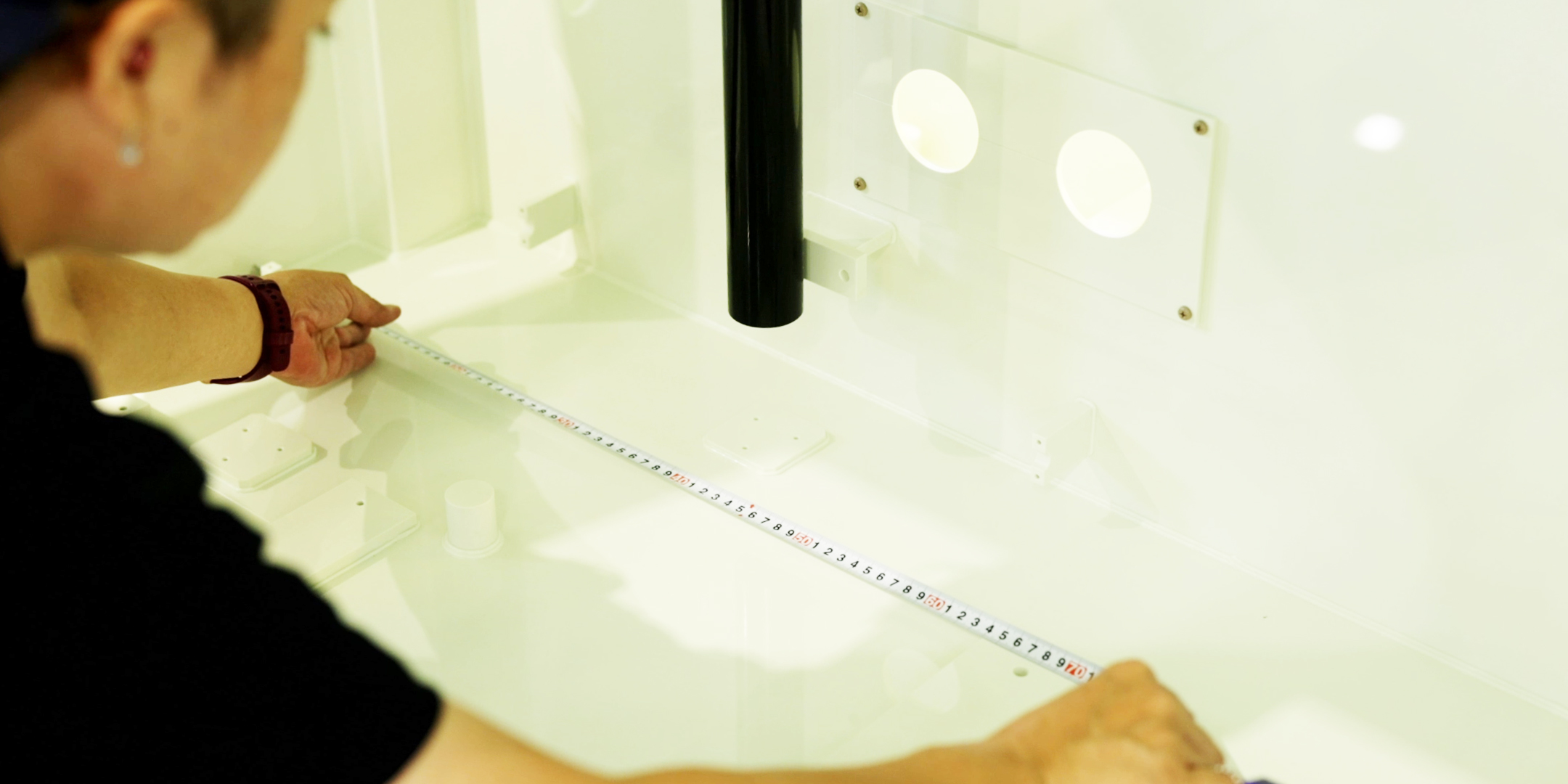
ポリプロピレン(PP)は、軽量で加工性に優れ、耐薬品性にも秀でた熱可塑性樹脂であり、化学・医薬・食品・水処理など多岐にわたる分野で利用されています。特に薬液タンクやシンクなどの大型構造物においては、金属よりもコストパフォーマンスと耐蝕性を兼ね備えたPPが選ばれる機会が増えています。
こうした樹脂構造物の製作において重要なのが、信頼性の高い溶接技術です。接合部の品質は装置全体の安全性・耐久性を大きく左右するため、適切な溶接法の選択と施工ノウハウの蓄積が不可欠です。本コラムでは、PP溶接の基礎特性から、大型製品製作における技術的課題と対策、さらには検査・品質保証まで、体系的に解説します。
ポリプロピレンの特性と溶接適性
ポリプロピレン(PP)は、以下のような性質を持つ樹脂です。
- 比重: 約0.91(プラスチック中でも非常に軽量)
- 耐薬品性: 酸・アルカリ・多くの溶剤に強い
- 熱変形温度: 約100℃前後(長期安定性)
- 吸水性: 極めて低く、湿気の影響を受けにくい
これらの特性により、PPはタンクやシンク、配管などの構造体に多用されます。さらに熱可塑性樹脂として、熱と圧力を加えることで分子間の再結合が可能であるため、溶接による強固な接合が可能です。
当社では、以下の2種類の溶接手法を中心に取り扱っています:
溶接法 | 特徴 | 適用例 |
---|---|---|
プラスチック溶接 | 熱風により母材と溶接棒を同時に加熱・軟化させて接合する手法。手作業による柔軟性があり、配管や小型構造の施工に適している。 | 仮付け、細部の修正、現場作業 |
半自動溶接 | 溶融したPP樹脂をノズルから押し出しながら圧着していく方法。厚板や長尺の溶接に向いており、安定した溶接強度が得られる。 | タンクの外周接合部、長距離継手 |
※加熱板溶接は、非常に高い接合強度を得られる工法ではありますが、当社では設備や運用体制の都合上、現在は取り扱っておりません。
大型構造物における溶接技術の課題と対応策
PP製の円筒タンクや角型シンクなど、容量や設置条件に応じて多様なサイズで設計される大型構造物の製作においては、以下のような技術課題への対応が特に重要となります。
①熱歪みと変形
PPは熱膨張率が高いため、加熱溶接による局所的な膨張・収縮により板材が反る、ねじれるなどの問題が発生しやすくなります。
- 仮付け溶接で位置ズレを防止
- 溶接順序を工夫し、左右・上下のバランスを取る
- 一定温度範囲内で溶接速度・圧力を最適化
②接合面の処理とフィット精度
高強度な溶接には、接合部の前処理が極めて重要です。不純物や酸化膜が存在すると、分子間の融合が阻害されます。
- アセトン洗浄やスクレーピングによる酸化除去
- 角部の面取りや開先加工
- 均一な押圧が得られる治具の使用
③製作環境の安定性と品質確保
当社では、PPタンクやシンクなどの溶接構造物はすべて社内で一貫して製作しており、完成後に出荷して現地での設置作業は別業者により行われています。
そのため、製作時点での品質安定化が極めて重要であり、外気温や湿度、作業者の技能差によるばらつきを抑えるための環境づくりと工程管理に注力しています。
- 空調管理された工場内での一貫溶接施工
- 加熱温度・押出量・溶接速度などのパラメータの標準化と記録管理
- 作業員への技術指導および溶接手順の標準化(SOP化)
溶接構造と設計の工夫
PP構造物の設計において、溶接による力の集中を回避する工夫も重要です。たとえば円筒タンクの場合、以下のような点に留意します。
- 底板と胴体部の接合部に補強リブを追加し、歪みを分散
- 溶接応力が一点に集中しないよう、段差や急角度を避ける
- 排液口や取付口は、広めの溶接面積を確保する構造に
また、使用する薬液の特性や容量に応じて、適切な板厚を選定することも重要です。耐薬品性、剛性、安全係数を加味した設計が求められます。
品質管理と検査技術
当社では、ISO9001:2015の運用に準じた品質管理体制のもとで、PP製構造物の製作を行っています。製作工程ごとの記録管理、出荷前検査の実施、溶接作業者の技能評価などを通じて、常に一定レベル以上の品質確保に努めています。
溶接後の品質確認については、以下の検査を組み合わせて実施しています。
①寸法検査
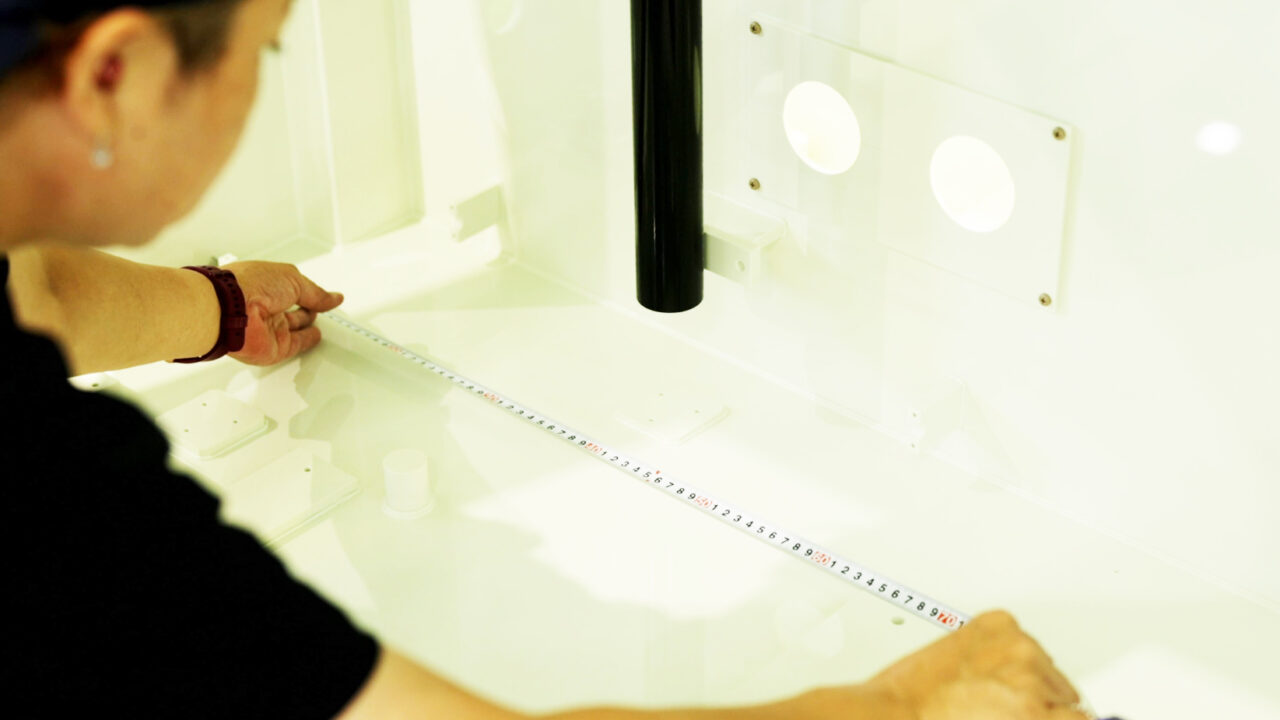
図面との照合により、タンク本体の高さ、直径、接続口の位置などを確認し、施工誤差が許容範囲内であることを確認します。必要に応じてゲージやスケール、ノギスなどを使用し、測定記録を残します。
②外観検査
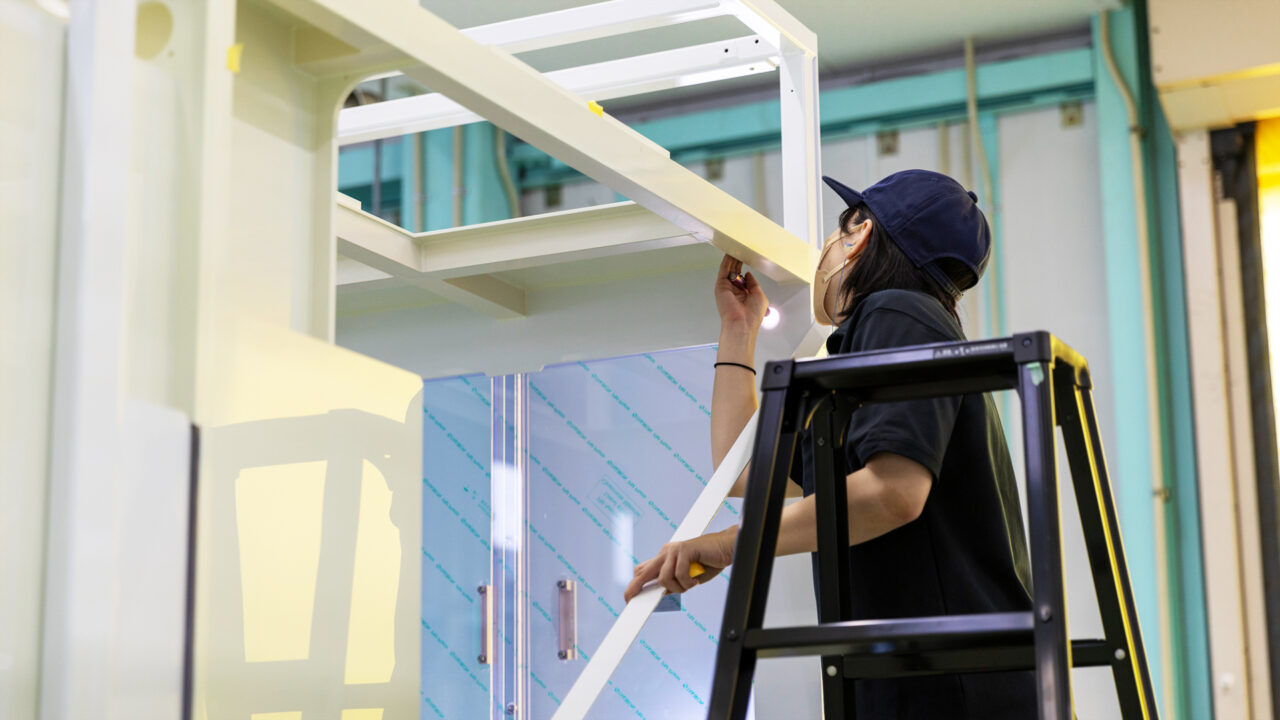
溶接ビードの形状や表面仕上げ状態を目視により確認します。以下のような不具合の有無をチェックします。
- 焼け過ぎ、冷え過ぎ、気泡
- クラック(割れ)
- 異物の巻き込み
- 表面の波打ちや反り
社内基準に基づいて合否を判定し、記録として保管します。
③リーク検査(漏れ試験)
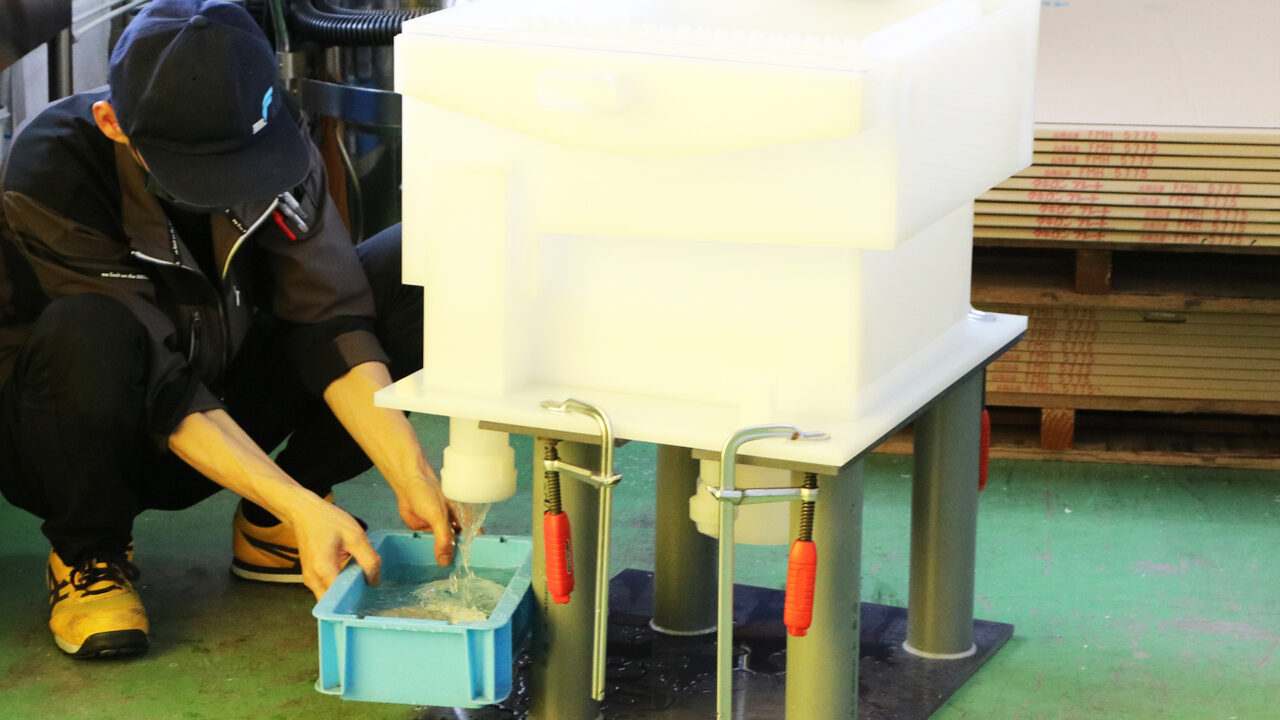
接液部の漏れがないことを確認するために、以下の方法でリーク検査を行います。
- 水張り試験: 製品内部に一定量の水を満たし、静置した後に外部への漏れを確認。主にシンクや槽に適用。
- エアリークテスター試験: 空気圧をかけ、圧力の保持状況を確認する方法。構造物や配管に対して高精度な漏れ検査が可能です。
これらの検査結果は、製品ごとに記録・管理され、必要に応じてお客様へ提出できる体制を整えています。
今後の展望と応用分野
PP溶接技術は、従来のタンク・配管にとどまらず、以下のような分野での展開が期待されています。
- 医薬・化粧品: 衛生性の高い薬液槽、洗浄設備、クリーンルーム対応機器
- 食品製造: 洗浄槽、仕込み槽、排液タンクなどで金属代替として注目
- 再生可能エネルギー: 軽量で絶縁性が高いため、電解槽やバッテリー関連部材にも応用
- 海外市場: 欧州のREACH規制や米国FDA対応を視野に入れた素材選定と溶接技術の輸出
また近年では、再生PP材やバイオPPの活用が進んでおり、溶接条件の再設定や設備対応も課題として浮上しています。
おわりに
PP溶接は、プラスチック製装置の安全性・耐久性を左右する極めて重要なプロセスです。中~大型構造物では、溶接技術そのものの精度が最終製品の信頼性に直結します。
私たちは、プラスチック溶接と半自動溶接を中心に、構造、工程、検査の3点を重視しながら、「安全」「確実」「高品質」な接合を提供しています。今後も現場と設計の連携を深め、幅広い業界に貢献できるプラスチック溶接技術を磨き続けています。