【食品業界とプラスチック加工技術①】カット野菜工場における異物混入防止戦略
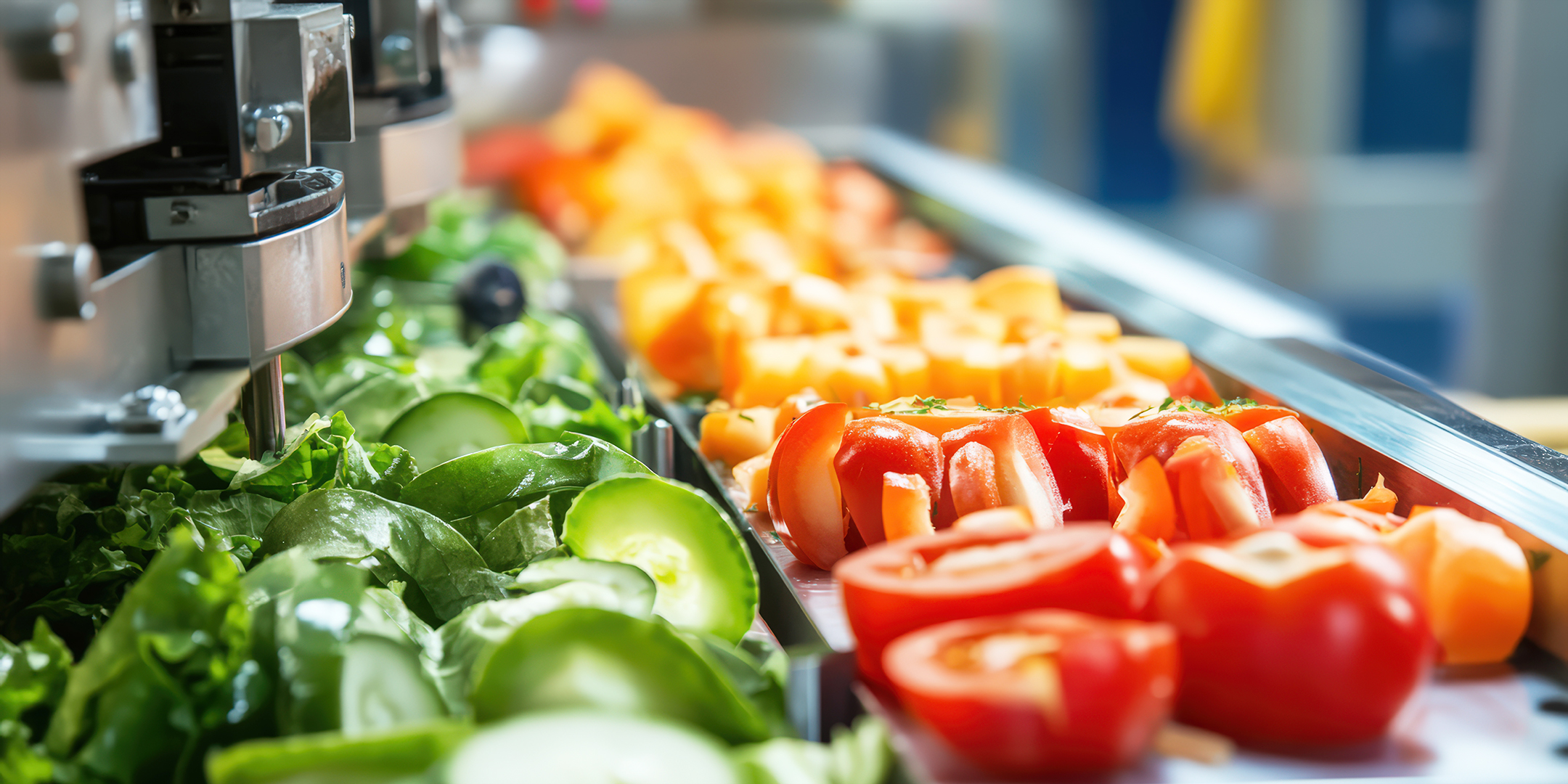
カット野菜製品は「手軽に利用できる」「衛生管理された商品である」というイメージで消費者に広く支持されています。手間をかけずに使える便利さから、家庭のみならず業務用としても多くの需要があります。しかし、こうした需要の高まりとともに、製造現場では多くの課題が顕在化しています。
特にカット野菜業界における最大の課題は、「異物混入リスク」です。品質トラブルが発生すると、企業ブランドへのダメージは計り知れず、その影響は長期にわたります。さらに、歩留まりの低下や洗浄作業の負担増加といった問題もあり、安全で効率的な製造プロセスが求められています。
本稿では、「虫・土・髪の毛・プラスチック破片リスクをゼロにする現場改善戦略」というテーマのもと、カット野菜工場における異物混入リスクを徹底的に分析します。そして、プラスチック加工技術を活用した具体的な対策を提案し、改善の方向性を示します。
食品業界向け 異物混入対策プラスチック技術シリーズ 一覧
食品工場で求められる異物混入防止の最新トレンドと、現場ごとの課題に応じたプラスチック加工技術の具体的な活用戦略を解説するシリーズです。衛生・品質向上に貢献する現場改善策や技術ノウハウを、分野別に分かりやすくご紹介します。
- 【技術①】カット野菜工場における異物混入防止戦略(このページ)
カット野菜の製造工程で発生しやすい異物混入リスクに対し、専用樹脂パーツや耐薬品性プラスチックの導入による異物混入ゼロの取り組みと現場実践例を紹介します。 - 【技術②】惣菜工場における異物混入防止戦略
複雑な設備が多い惣菜工場での異物混入対策として、洗浄性・耐久性に優れたプラスチック部品や溶接技術を活用し、衛生管理と生産性向上を両立させる方法を解説します。 - 【技術③】製麺加工工場における異物混入防止戦略
製麺工程特有の異物混入リスクに対し、耐摩耗性や摺動性に優れたプラスチックの選定・加工ノウハウをもとに、設備の安全性・清潔性を高める具体策を紹介します。
※太字(このページ)表記が現在閲覧中の記事です。
カット野菜のメリットと製造リスク
カット野菜製品の最大のメリットは、その「手軽さ」と「衛生管理が行き届いている」という点にあります。加工済みのため、調理時間を大幅に短縮できるだけでなく、安全性が確保されているため、消費者や食品業界から広く支持を集めています。
一方で、製造現場では以下のようなリスクが常に存在します。
- 異物混入リスク
- 歩留まり低下問題
- 洗浄・衛生管理負担の増大
特に異物混入リスクは、企業ブランドを傷つけるだけでなく、リコールやクレーム対応といったコスト面でも大きな負担となります。こうした課題に対応するためには、徹底的なリスク分析と改善策の導入が不可欠です。
カット野菜工場における異物混入リスクの実態
カット野菜の製造工程には、多くの異物混入リスクが潜んでいます。以下は、その主なリスク要因と発生源です。
異物種別 | 主な発生源・原因 |
虫(昆虫類) | 畑からの付着、洗浄不足 |
土・砂利 | 根菜・葉物の付着残り |
プラスチック破片 | 設備劣化、パーツ破損 |
髪の毛 | 作業者由来、静電吸着 |
ビニール破片 | 手袋破れ、袋開封時の切断片 |
これらの異物が混入する主な場面として、洗浄工程、カット工程、搬送・袋詰め工程が挙げられます。各工程でのリスクを見極め、それぞれに対応する防止策を講じることが重要です。
主な発生ポイントとリスク場面
カット野菜工場内の各工程には、それぞれ異物混入リスクが潜んでいます。以下は主な工程別のリスク場面です。
- 洗浄工程:虫・土残留
根菜類の泥や葉物に付着した虫が、洗浄不足により残留するリスクがあります。 - カット工程:設備破片・包丁殺菌庫劣化片
カッターや包丁の刃の劣化、殺菌庫の樹脂部品の破損によるプラスチック破片の混入が考えられます。 - 搬送・袋詰め工程:髪の毛・ビニール片混入
搬送中や袋詰め時に作業者の髪の毛が静電気で吸着したり、袋の開封時にビニール片が混入するリスクが存在します。
これらのリスクは、製品の出荷前に完全に排除しなければなりません。異物混入を防ぐためには、「現場で起きているリスク」+「未然防止技術」の両面から対策を講じることが求められます。
異物混入防止の基本アプローチ
異物混入を防ぐためには、発生源対策、視認性向上、付着防止という3つの観点からアプローチする必要があります。
発生源対策(未然に防ぐ)
異物混入をゼロに近づけるためには、異物が発生する根本原因を除去することが重要です。以下は、その具体例です。
- 設備部材は高耐久・劣化しにくいプラスチックに変更
- 作業用品(手袋・帽子)は破れにくい素材限定
- 材料袋開封専用ツール使用(カッター禁止)
視認性向上(発見しやすくする)
異物が万が一混入した場合でも、迅速に発見できる体制を整える必要があります。
- 透明カバー・透明パイプ化
- ライト照射検査システム導入
付着防止(静電気対策)
静電気が原因で髪の毛やほこりが付着するケースが多いため、帯電防止素材を積極活用します。
- 帯電防止素材活用
- エアシャワー・湿度管理強化
プラスチック加工技術を活用した異物防止策
異物混入を防ぐためには、単なる防止策だけでなく、その効果を明確に測定できる仕組みを構築することが重要です。本章では、「透明化技術」「ライト透過設計」「帯電防止処理」「カラー設計」の4つの技術を、対策と効果の両面から解説します。
透明化技術による内部視認性向上
異物混入を未然に防ぐためには、工程内の状態をリアルタイムで確認できる「透明化技術」が有効です。特に洗浄ラインや搬送ラインでは、異物や汚れの確認を迅速に行うために、透明樹脂の活用が推奨されます。
- 排水ラインに透明PVCパイプを採用
汚れの付着状態や異物の残留を可視化 - 洗浄タンクカバーに透明PMP(ポリメチルペンテン)を使用
タンク内部の洗浄状態を目視で確認
異物が混入していないかを簡単に検査可能
- 残渣・汚れ・虫の付着を迅速に発見できる
- 洗浄残しが確認しやすく、定期洗浄の判断が確実になる
- 汚れや残渣の可視化により、虫の発生リスクを早期に発見・防止
- 異物の早期発見により、ライン停止や製品ロスを最小限に抑えられる
ライト透過設計で虫・異物検出率アップ
葉物野菜や細かいカット品の検査では、異物が見逃されるケースが多発します。これを防ぐためには、ライト透過設計が有効です。異物を影として浮き上がらせることで、微細な異物でも検出しやすくなります。
- 葉物野菜検査台に乳白色UHMW-PEカバーを設置
光の透過率が調整された乳白色素材を使用し、異物が「影」として浮き上がる構造 - テーブル下にLEDライトを配置
均一な光源を確保し、虫・異物の輪郭がより鮮明に映し出される
- 異物目視検査の精度が飛躍的に向上
- 小さな虫や髪の毛、ビニール片などの微細な異物を早期に検出可能
- 作業者の負担軽減と検査効率の向上
帯電防止処理による髪の毛・ほこり付着防止
カット野菜の製造現場では、静電気による髪の毛やほこりの付着が異物混入の大きな原因の一つです。特に搬送ラインや袋詰め工程では、樹脂製品が帯電しやすく、異物を吸着しやすい環境が整ってしまうため、この問題を解決するための帯電防止処理が求められます。
- 帯電防止UHMW-PE(超高分子量ポリエチレン)を採用
滑り性を維持しつつ、帯電防止効果を発揮する素材 - 帯電防止PVC(ポリ塩化ビニル)を加工して搬送路を覆う
帯電抑制により、異物の吸着を最小限に抑制 - 静電吸着による髪の毛・ビニール片付着を防ぐ
静電気の発生を抑え、作業者の髪の毛やほこりの飛散を防止
- 静電吸着による髪の毛やほこりの付着を大幅に減少
- 搬送中の異物混入リスクを軽減し、最終検査工程での異物発見率を向上
- プラスチック製搬送路の帯電防止効果により、異物吸着の発生を抑止
- 作業者の静電気帯電防止により、手袋や衣類からの異物落下を防止
- 袋詰め工程でのビニール片の静電吸着を抑え、品質事故を予防
カラー設計による異物発見率向上
異物を検出しやすくするための効果的な手法の一つが「カラー設計」です。異物が目立ちやすい色の背景を設定することで、微細な異物でも視覚的に発見しやすくなります。食品工場では、青色や緑色のトレイや搬送シュートがよく採用されており、白色手袋片や黒色髪の毛などと強くコントラストを取ることで異物の早期発見を狙います。
- ブルー樹脂トレイの導入
白色手袋片やビニール片などが目立ちやすく、視認性を向上 - ブルー搬送シュートの設置
黒色髪の毛や透明ビニール片とのコントラストを強調 - 検査台の色を青色または緑色に統一
目視検査時の異物発見率を向上させる色彩設計
- 異物(白色:手袋片、黒色:髪の毛、透明:ビニール片等)と背景色のコントラストが強調されることで、異物発見率が向上
- 手袋片や髪の毛、ビニール片などの小さな異物も、背景色と対照的になることで早期に検出可能
- 視覚的な負担が軽減され、作業者の検査効率がアップ
- 異物検出の見逃しリスクが低減し、異物混入クレームの発生を抑止
洗浄・清掃作業の効率化と安全性向上
異物混入防止策の中でも、洗浄・清掃工程の改善は欠かせません。汚れが溜まりやすい箇所や清掃が困難な構造を改善し、作業効率を高めることで異物の残留リスクを抑制します。ここでは、滑り性の高いプラスチック素材を活用した対策を紹介します。
- UHMW-PEライニングの採用
搬送路やシュート部分に滑り性の高いUHMW-PEを設置し、汚れの付着を防止 - 鏡面仕上げによる洗浄性向上
汚れが付着しにくい平滑な表面仕上げを採用 - 着脱式カバーの設計
分解・洗浄が簡単にできるよう、取り外し可能なカバーを設置 - 排水ラインの透明化
透明PVCパイプで内部の汚れの確認を容易にし、洗浄残しを防ぐ
- 洗浄時間が短縮され、作業効率が向上
- 汚れや異物の付着を抑制し、洗浄残しリスクの低減
- 着脱式カバーにより、清掃作業の手間を削減し、作業者負担が軽減
- 排水ラインの透明化により、虫の発生リスクを早期に発見・防止
プラスチックとステンレス304の性能比較
異物混入対策として導入されるプラスチック素材には、従来のステンレス304との明確な性能差があります。ここでは、それぞれの衛生性・滑り性・耐薬品性などを比較し、異物混入防止の観点から見た有効性を評価します。
比較項目 | ステンレス304 | プラスチック(UHMW-PE・PPなど) |
衛生性 | 赤錆・ピンホール腐食リスクあり | 腐食ゼロ、衛生長期安定 |
滑り性 | 血液・水で滑りやすい | 滑り性安定、清掃しやすい |
軽量性 | 重い | 軽量、作業負担軽減 |
耐薬品性 | 酸・塩分負荷で劣化リスクあり | 強薬品にも耐久性あり |
コスト | 高い導入・メンテナンス費用 | 初期投資低+更新容易 |
プラスチック素材は、ステンレスに比べて軽量で耐薬品性に優れており、清掃性やコスト面でも有利です。特に異物混入リスクの抑制と作業効率の向上を同時に実現できる点が強みです。
プラスチック導入時の注意点
異物混入防止策としてプラスチック素材を導入する際には、異物混入リスクの低減だけでなく、新たなリスクの発生を防ぐための適切な素材選定と設計が求められます。以下のポイントを重点的に考慮することが重要です。
- 食品衛生法(厚労省規格)適合素材の選定
食品接触面に使用する樹脂は必ず認証取得済みのものを選定
認証がない素材は異物混入リスクを高める可能性がある - 耐熱性・耐薬品性の確保
洗浄工程や加熱工程に適した素材(例:PMP、PP、UHMW-PE)を選定
耐薬品性が不十分な場合、洗浄時に劣化し破片が混入するリスクがある - 抗菌加工グレードの積極活用
汚れの付着防止や菌の繁殖抑制に有効
ただし、抗菌加工のみで衛生環境が維持できるわけではなく、定期的な洗浄と組み合わせることが必須 - 洗浄性を考慮した設計
平滑な表面仕上げを採用し、汚れの付着を防止
着脱可能なカバーを設計し、分解洗浄が容易な構造にする
まとめ
カット野菜工場における異物混入防止策として、プラスチック技術の活用は非常に有効です。具体的な対策としては、以下の点が挙げられます。
- 透明化技術による内部視認性の向上:異物の早期発見
- ライト透過設計の導入:微細異物の検出率向上
- 帯電防止処理の活用:髪の毛・ほこりの付着防止
- カラー設計による視認性向上:異物の背景色とのコントラストを強調
- 洗浄工程の効率化:滑り性素材の導入と分解洗浄設計
- 素材の適正選定:食品衛生基準への適合と耐薬品性・耐熱性の確保
これらの技術を総合的に導入することで、異物混入のリスクを大幅に低減させることが可能です。
透明化、ライト透過、帯電防止、カラー設計といった先端加工技術を駆使し、工場全体の異物リスクをゼロに近づけることで、以下の効果が期待されます。
- 異物混入ゼロ:透明化技術やライト透過設計の導入により、異物の発見精度が飛躍的に向上
- 歩留まり最大化:異物の早期発見と異物混入リスクの抑制により、不良品の発生を最小限に抑える
- 洗浄性強化:滑り性の高い素材や着脱式カバーの導入で、洗浄工程の効率化と洗浄残しリスクの防止
- クレームリスクの最小化:異物検査の精度向上により、クレーム発生率が低減
- 異物発見率の向上:目視検査の精度向上によって、微細な異物も見逃さない
- 清掃作業の効率化:分解洗浄が容易な設計により、作業時間を短縮
- 製品の品質安定化:異物混入防止策の徹底により、品質基準を安定化
- 作業者の負担軽減:帯電防止処理やカラー設計の導入で、視覚的負担や異物吸着リスクが軽減
- 生産性の向上:異物検査の効率化と異物混入防止の徹底により、ライン稼働率が向上
- コストの最適化:洗浄頻度の削減と異物混入クレームの減少により、トータルコストが削減される
異物混入ゼロを目指すためには、各工程のリスクを徹底的に洗い出し、適切なプラスチック素材と加工技術を選定・導入することが不可欠です。
これからのカット野菜工場においては、これらの対策が品質基準の向上と生産効率の最大化に直結するでしょう。
食品業界向け 異物混入対策プラスチック技術シリーズ 一覧
食品工場で求められる異物混入防止の最新トレンドと、現場ごとの課題に応じたプラスチック加工技術の具体的な活用戦略を解説するシリーズです。衛生・品質向上に貢献する現場改善策や技術ノウハウを、分野別に分かりやすくご紹介します。
- 【技術①】カット野菜工場における異物混入防止戦略(このページ)
カット野菜の製造工程で発生しやすい異物混入リスクに対し、専用樹脂パーツや耐薬品性プラスチックの導入による異物混入ゼロの取り組みと現場実践例を紹介します。 - 【技術②】惣菜工場における異物混入防止戦略
複雑な設備が多い惣菜工場での異物混入対策として、洗浄性・耐久性に優れたプラスチック部品や溶接技術を活用し、衛生管理と生産性向上を両立させる方法を解説します。 - 【技術③】製麺加工工場における異物混入防止戦略
製麺工程特有の異物混入リスクに対し、耐摩耗性や摺動性に優れたプラスチックの選定・加工ノウハウをもとに、設備の安全性・清潔性を高める具体策を紹介します。
※太字(このページ)表記が現在閲覧中の記事です。