【プラスチック加工の基礎①】基礎からわかる!プラスチック切削加工の4つのポイント
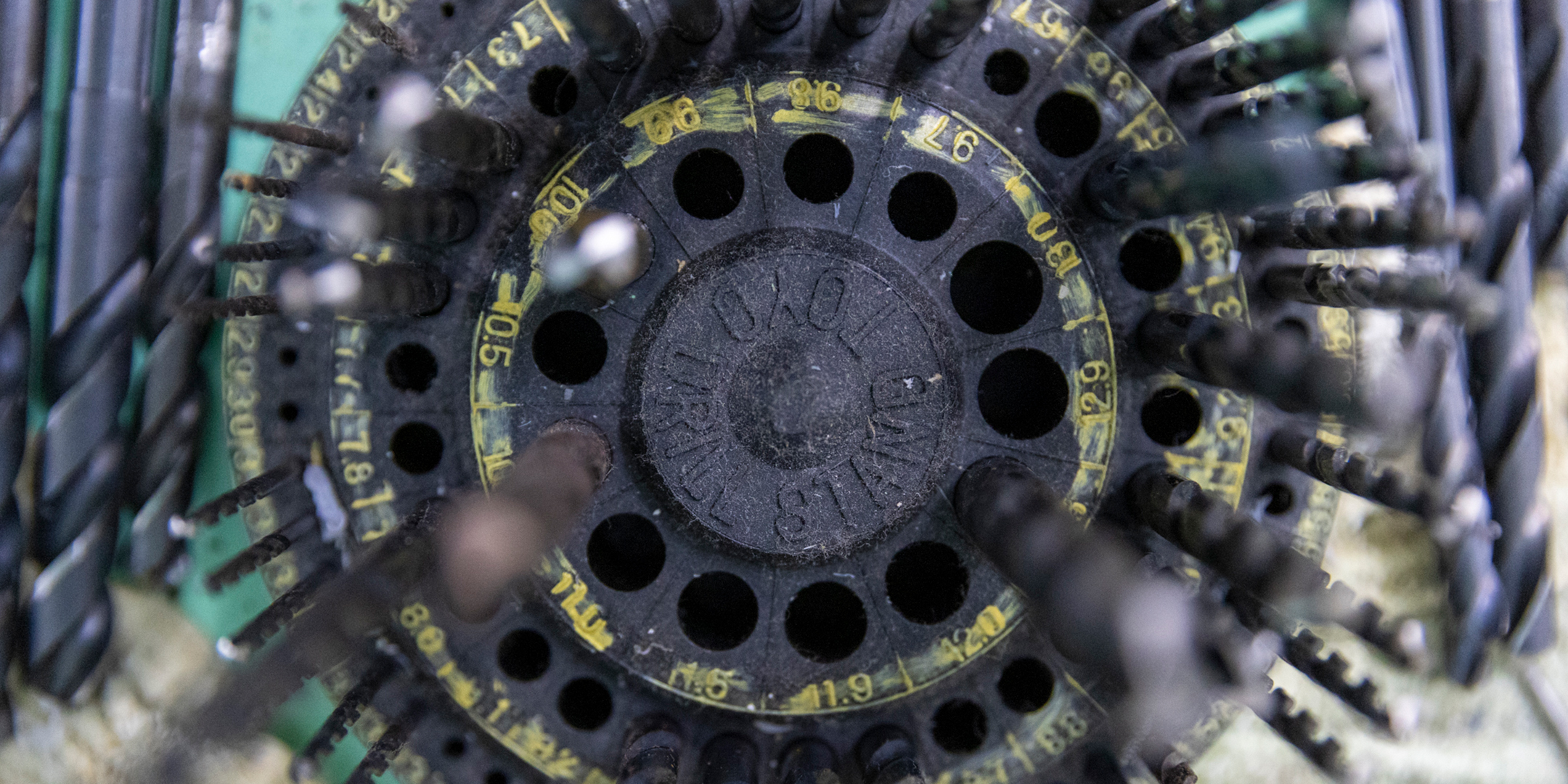
近年、装置や製品の軽量化、電気絶縁性、耐薬品性、非磁性化といった特性を求めて、金属部品から樹脂部品への置き換えが進んでいます。特に、医療機器や半導体製造装置、食品製造装置、分析機器といった分野では、部品の軽量化や高機能化に対するニーズが高まっており、プラスチック素材の採用が増加傾向にあります。
また、部品単体としての性能だけでなく、加工コストや納期対応の観点からも、樹脂は非常に有効な選択肢となっています。金属に比べて材料価格が安価な場合も多く、切削速度を上げやすいため、量産性にも優れています。加えて、表面処理や後加工の工程が不要なケースもあり、トータルでの加工時間短縮にも貢献します。
このような背景のもと、金属加工を主業とするメーカーや加工業者の中でも、プラスチック加工への関心が高まりつつあります。フジワラケミカルエンジニアリングでは、長年にわたり多種多様なプラスチック素材を扱い、切削加工に特化したノウハウを積み重ねてきました。中でも塩化ビニル(PVC)の切削加工においては、業界トップクラスの実績を誇り、半導体装置向けの精密部品の製作を多数手がけています。
プラスチック加工の基礎シリーズ 一覧
プラスチック切削加工の基本から、NCルーターやマシニングセンタ、NC旋盤、木工機械の応用まで、初学者にも分かりやすくプラスチック加工の基礎を体系的に解説するシリーズです。現場の課題解決や技術選定にも役立つ実践的な内容をまとめています。
- 【基礎①】基礎からわかる!プラスチック切削加工の4つのポイント(このページ)
プラスチック切削加工の基本と注意点を徹底解説。初学者にもわかりやすい入門ガイドです。 - 【基礎②】NCルーター技術による高精度プラスチック板加工の実現
板材加工の現場改善に役立つNCルーターの活用法と事例を紹介します。 - 【基礎③】金属と何が違う?プラスチックのマシニングセンタ加工
金属加工と異なるプラスチック専用マシニング技術の要点を解説します。 - 【基礎④】プラスチックNC旋盤加工:課題解決と高品質実現の技術革新
NC旋盤ならではの課題とその解決策、高品質加工へのアプローチを詳述します。 - 【基礎⑤】木工機械活用術:柔軟で高効率なプラスチック加工の実現
木工技術の応用による多品種・小ロットのプラスチック加工事例を紹介します。
※太字(このページ)表記が現在閲覧中の記事です。
①プラスチック加工と金属加工との共通点と相違点
プラスチックの切削加工は、使用する工作機械や加工プログラム、段取りの考え方など、多くの面で金属加工と共通しています。そのため、アルミニウムや真鍮などの非鉄金属を加工してきた経験があれば、一定の応用が可能です。実際、弊社でも金属加工の経験を持つ技術者が、スムーズに樹脂加工に対応しているケースが多く見られます。
しかし、プラスチックは金属とはまったく異なる物理特性を持っており、同じ感覚で加工を行うと、思わぬ不良や品質トラブルにつながることがあります。最大の違いは、熱伝導性と剛性の低さに起因する「熱溶着」や「変形」「反り」といった現象です。
例えば、切削時に発生した熱が工具先端や加工面にとどまり、プラスチックが軟化・融着してしまうと、工具に巻き付き、寸法精度の低下や表面粗さの悪化につながります。さらに、加工中の応力や保持方法によっては、部品が加工後に歪んだり、内部応力が解放されて反りが生じる場合もあります。
このような特性に対応するためには、適切な切削条件の設定だけでなく、素材ごとの熱特性・吸湿性・剛性などの理解が不可欠です。フジワラケミカルエンジニアリングでは、樹脂素材の特性を熟知した上で、最適な加工条件・工具選定・保持方法を設計し、安定した品質の確保を実現しています。
- 使用する工作機械、加工プログラム、段取りの考え方など、多くの面で金属加工と同様のアプローチが可能
- 非鉄金属(アルミニウム、真鍮など)の加工経験があれば、その知識を樹脂加工に応用できる
- 金属加工の経験を持つ技術者がスムーズに樹脂加工へ移行可能なケースが多い
- プラスチックは金属と比べ、物理特性が大きく異なる(熱伝導性と剛性の低さ)
- 切削時に発生した熱が工具先端や加工面に留まりやすく、「熱溶着」が発生しやすい
- 熱の蓄積により、プラスチックが軟化・融着して工具に巻き付き、寸法精度や表面仕上げに影響を及ぼす可能性がある
- 加工中の応力や保持方法の違いにより、部品が加工後に歪んだり、反りが生じる場合がある
- 適切な切削条件の設定や、素材ごとの熱特性、吸湿性、剛性の理解が不可欠である
②材料別の特徴と加工しやすさ(用途別に分類)
プラスチック素材は、機械的特性や使用環境に応じて大きく2つに分類されます。ひとつは、耐熱性・機械強度・寸法安定性に優れた「エンジニアリングプラスチック」、もうひとつは、コストパフォーマンスや加工性の良さが特徴の「一般プラスチック」です。以下に、代表的な素材とフジワラの対応実績を示します。
エンジニアリングプラスチック(高機能素材)
材料 | 特徴 | フジワラの対応力 | 主な用途 | |
---|---|---|---|---|
POM(ジュラコン) | 高剛性・耐摩耗性・寸法安定性 | ◎ | 高精度加工対応可 | ギア、摺動部品、機構部材 |
PEEK | 高耐熱(約250℃)・高強度・耐薬品性 | ◎ | 微細部品も対応実績あり | 半導体装置部品、医療部品 |
MCナイロン | 自己潤滑性・耐摩耗性 | ◎ | 長尺・大型部品加工可 | ブッシュ、搬送部品、ガイドローラー |
UHMW-PE | 衝撃吸収・低摩擦・耐薬品性 | 〇 | 切削条件と工具設計で対応 | 滑り材、衝撃吸収パッド |
一般プラスチック(汎用素材)
材料 | 特徴 | フジワラの対応力 | 主な用途 | |
---|---|---|---|---|
PVC(塩化ビニル) | 耐薬品性・絶縁性・加工性 | ◎ | 得意分野。半導体装置向けに多数製作中 | 洗浄装置、薬液配管部品、電気絶縁部品 |
PP(ポリプロピレン) | 軽量・耐薬品性・吸水性が低い | 〇 | 保持工夫で安定加工可能 | 医療用構成部品、タンク周辺部品 |
アクリル | 高透明性・表面美観 | 〇 | 光沢仕上げ・研磨も対応可 | カバー、表示板、光学部材 |
これらの素材ごとに、切削条件・工具形状・保持方法などが大きく異なるため、経験とノウハウが要求されます。
フジワラケミカルエンジニアリングでは、数多くの加工実績をもとに、素材特性に応じた最適な加工条件をデータベース化し、高い再現性と品質安定性を実現しています。
③加工条件と刃物選定の基本
プラスチック加工では、「熱」と「変形」のリスクを最小限に抑えるため、加工条件と工具選定が非常に重要です。ここでは、基本的な考え方をご紹介します。
- 回転数:9,000rpm以上の高速回転が理想。低回転では切削熱が工具にこもりやすく、溶着の原因となる。
- 送り速度:素材ごとに最適な送り速度を設定。速すぎるとバリ、遅すぎると熱蓄積が起きやすい。
- 切り込み量:浅めに設定し、必要に応じて複数回に分けて加工。特に薄物や精密部品では効果的。
- 冷却方法:ミストクーラント、エアブロー、無冷却(ドライ)を使い分け。素材ごとの反応を確認。
- 刃物:超硬エンドミル(2~3枚刃)が基本。切れ味の鋭い工具を使用し、コーティングは素材によって選択。
また、刃物の摩耗が製品精度に直結するため、刃物交換タイミングや摩耗限界の管理も重要な品質管理項目となります。当社では、これらの条件を自社基準として標準化し、オペレーター間でのばらつきを最小限に抑えています。
④樹脂加工導入時の注意点とアドバイス
金属加工から樹脂加工へ移行する際には、単に機械や工具を変えるだけでは対応できない「素材特性の壁」が存在します。以下のようなポイントに特に注意が必要です。
- 保持方法の工夫:柔らかい樹脂を金属と同じチャッキングで固定すると、変形や破損の原因に。専用のゴムパッドや真空チャックを活用。
- 静電気対策:切粉が静電気で付着しやすく、切削効率や品質に影響。帯電防止装置やエアブローで対策。
- 吸水と寸法変化:PA(ナイロン)などの吸湿性のある素材では、加工後に寸法が変化する可能性。納品時の寸法保証に注意。
- 表面仕上げと見た目:バリや白化が生じやすい素材では、最終工程での面取り・仕上げ処理も品質に直結。
フジワラケミカルエンジニアリングでは、こうした注意点を踏まえ、設計段階からの技術提案や試作支援も積極的に行っております。樹脂加工初心者の方にも安心してご相談いただける体制を整えております。
まとめ:プラスチック加工の精度は、知見と経験が支える
プラスチック切削加工は、一見すると金属加工と似ているようで、実は全く異なるノウハウと技術が求められる分野です。樹脂ごとの特性に対する深い理解と、それに対応する加工技術・設備・管理体制があって初めて、高品質な部品が実現できます。
フジワラケミカルエンジニアリングは、PVCをはじめとする多種多様なプラスチックの加工に対応し、特に半導体装置向けの高精度部品製造において豊富な実績を有しています。これまで蓄積してきたノウハウをもとに、お客様のご要望に合わせた最適なご提案と、高品質な製品づくりをお約束いたします。
金属から樹脂への素材変更や、複雑形状の精密樹脂部品の加工をご検討の際は、ぜひフジワラケミカルエンジニアリングまでお問い合わせください。
プラスチック加工の基礎シリーズ 一覧
プラスチック切削加工の基本から、NCルーターやマシニングセンタ、NC旋盤、木工機械の応用まで、初学者にも分かりやすくプラスチック加工の基礎を体系的に解説するシリーズです。現場の課題解決や技術選定にも役立つ実践的な内容をまとめています。
- 【基礎①】基礎からわかる!プラスチック切削加工の4つのポイント(このページ)
プラスチック切削加工の基本と注意点を徹底解説。初学者にもわかりやすい入門ガイドです。 - 【基礎②】NCルーター技術による高精度プラスチック板加工の実現
板材加工の現場改善に役立つNCルーターの活用法と事例を紹介します。 - 【基礎③】金属と何が違う?プラスチックのマシニングセンタ加工
金属加工と異なるプラスチック専用マシニング技術の要点を解説します。 - 【基礎④】プラスチックNC旋盤加工:課題解決と高品質実現の技術革新
NC旋盤ならではの課題とその解決策、高品質加工へのアプローチを詳述します。 - 【基礎⑤】木工機械活用術:柔軟で高効率なプラスチック加工の実現
木工技術の応用による多品種・小ロットのプラスチック加工事例を紹介します。
※太字(このページ)表記が現在閲覧中の記事です。