プラスチック加工会社として「自由設計」を支えるフジワラケミカル式ハイブリッド技術
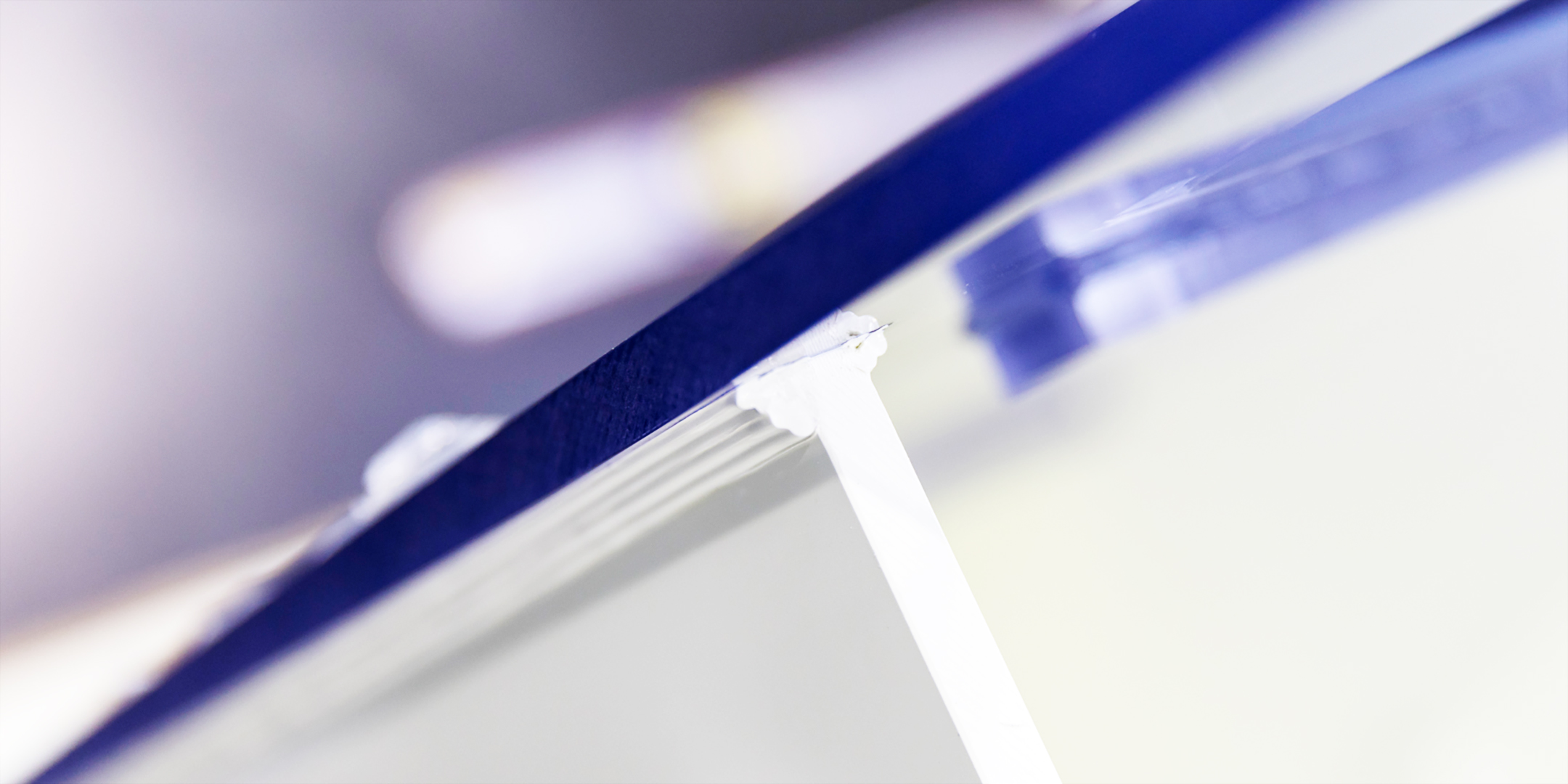
フジワラケミカルエンジニアリングは、プラスチック加工会社として、設計自由度の高い製品づくりを支えるために、複数の加工技術を組み合わせた「ハイブリッド体制」を構築・運用しています。
本コラムでは、当社が実際に取り組んでいる加工工程や設備運用の工夫を紹介し、「図面どおり」にとどまらず、「設計意図そのものを形にする」ための技術と現場力について、技術解説ページで紹介してきた内容を再編集するかたちでまとめています。
軽さ・強度・密閉性・洗浄性・短納期対応など、現代の装置産業に求められる部品性能は年々高度化・多様化しており、従来の金属加工では限界を迎える場面も増えています。これらの課題に対し、私たちはエンジニアリングプラスチックの特性を熟知し、7つの加工技術を有機的に連携させることで、構造設計・加工・組み立てまでを一貫して支援しています。
NCルーター、マシニングセンタ、NC旋盤、木工機械、熱曲げ、溶接といった加工設備の特性を最大限に活かすだけでなく、試作・量産の切り替えや品質保証、さらに組み立て工程を含めた総合対応力こそが、当社が提供する「自由設計」の土台です。
この記事では、それぞれの加工技術の特徴と組み合わせ方、さらに社内連携による工程全体の最適設計について、具体的な事例や運用ポイントを交えて紹介します。
序章:求められる「複合性能」と金属の限界

装置産業の最前線である半導体製造装置、医療用機器、食品充填システムなどでは、年々その部品性能に対する要求が複雑さを増しています。軽量であること、薬液に耐えること、磁気を帯びないこと、そして清潔であること。それぞれが単体でも高度な技術を要する中で、それらすべてを「同時に」満たすことが求められています。
金属材料は長くその要請に応えてきましたが、今まさに限界を迎えつつあります。設計自由度の制約、重量による構造負荷、そして素材コストや加工性の問題といった課題が浮き彫りになってきました。こうした背景から、今再び「エンジニアリングプラスチック」が脚光を浴びています。
しかし、プラスチックも決して万能ではありません。熱伝導率の低さから生じる熱溶着や反り、精密寸法の再現性、溶接強度への懸念など、課題は多く存在します。これらの課題をどう乗り越えるかが、真の実用化の鍵を握ります。
フジワラケミカルエンジニアリングでは、7つの技術分野を連携させたハイブリッド型の加工体制によって、こうした課題を現場から一つずつ解決してきました。
本稿では、当社が公開している技術解説ページの内容をもとに、現在当社が提案する「樹脂加工のあるべき姿」について、技術コラムとして再構成しています。
- 切削加工
刃物を用いて素材を削り、所定の形状に整える加工方法。寸法精度や表面仕上げに優れています。 - NCルーター加工
数値制御(NC)によって刃物の動きを制御し、主に板材を高速・高精度に切削する加工法。複雑形状にも対応可能です。 - マシニングセンタ加工
工具交換機能を備えた多機能な切削機械を用い、穴あけ・削り・溝加工などを一台でこなす高効率な加工技術です。 - NC旋盤加工
回転する素材に刃物を当てて加工する方法で、円筒形状やネジなどの精密部品の製作に適しています。 - 木工機械加工
本来木材用に使われる切削機械を樹脂加工に応用。コスト効率が高く、柔らかいプラスチック素材に最適です。 - 曲げ加工
熱や力を加えて板材や棒材を曲げる加工方法。継ぎ目のない立体形状を実現でき、強度や洗浄性にも優れます。 - 溶接加工
複数の樹脂部品を熱で溶かして接合する加工法。強固かつ気密性の高い一体構造を形成できます。
1. 切削の土台を支える「4点制御」
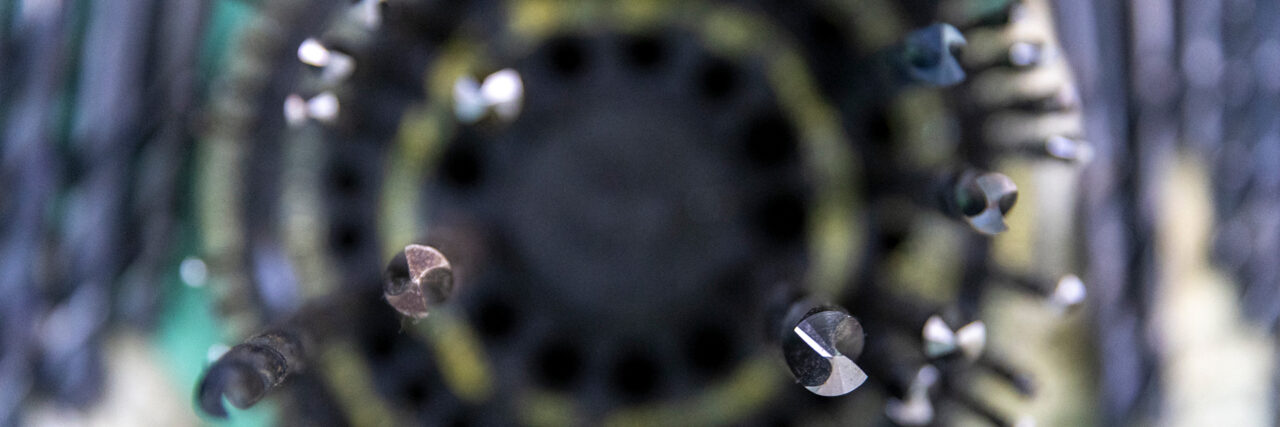
プラスチック加工の出発点は、素材ごとの性質を見極めたうえで、最適な切削条件を確立することにあります。金属と比べて、樹脂は熱伝導性が低く、柔らかく変形しやすいため、金属加工の常識がそのままでは通用しません。特に、寸法精度、加工後の洗浄性、部品の寿命に直結する「初期の加工精度」を安定化させることが最も重要な課題となります。
当社では、以下の4点を切削条件の設計指針として定めています。
- 熱管理:刃先温度を120℃以下に抑え、過熱による溶融やバリの発生を防ぎます。
- 保持治具:真空チャックと低圧クランプの併用によって、樹脂を傷つけず、安定した固定を実現します。
- 工具材質:超硬+DLCコーティングを採用し、摩耗耐性と低摩擦性を両立させています。
- 切削油:洗浄しやすさに優れた水溶性クーラントを選定しています。
これらを組み合わせることで、「バリが出にくい」「歪みにくい」「洗浄しやすい」といった安定した加工環境を再現し、すべての工程の基盤を築いています。
微細なバリは、最終製品の使用環境や洗浄工程において異物として問題視されることがあり、製品の信頼性や安全性に直結します。そのため、切削段階からバリの発生を抑制する設計が不可欠です。こうした背景から、当社では切削段階から最終使用環境を見据えた工程設計を徹底しています。
さらに、素材の熱変形挙動を加工前にシミュレーションし、加工条件やクランプ圧、工具の回転数を事前にセットアップしています。これにより、試作レスで安定した初品精度を実現できる体制を整えています。
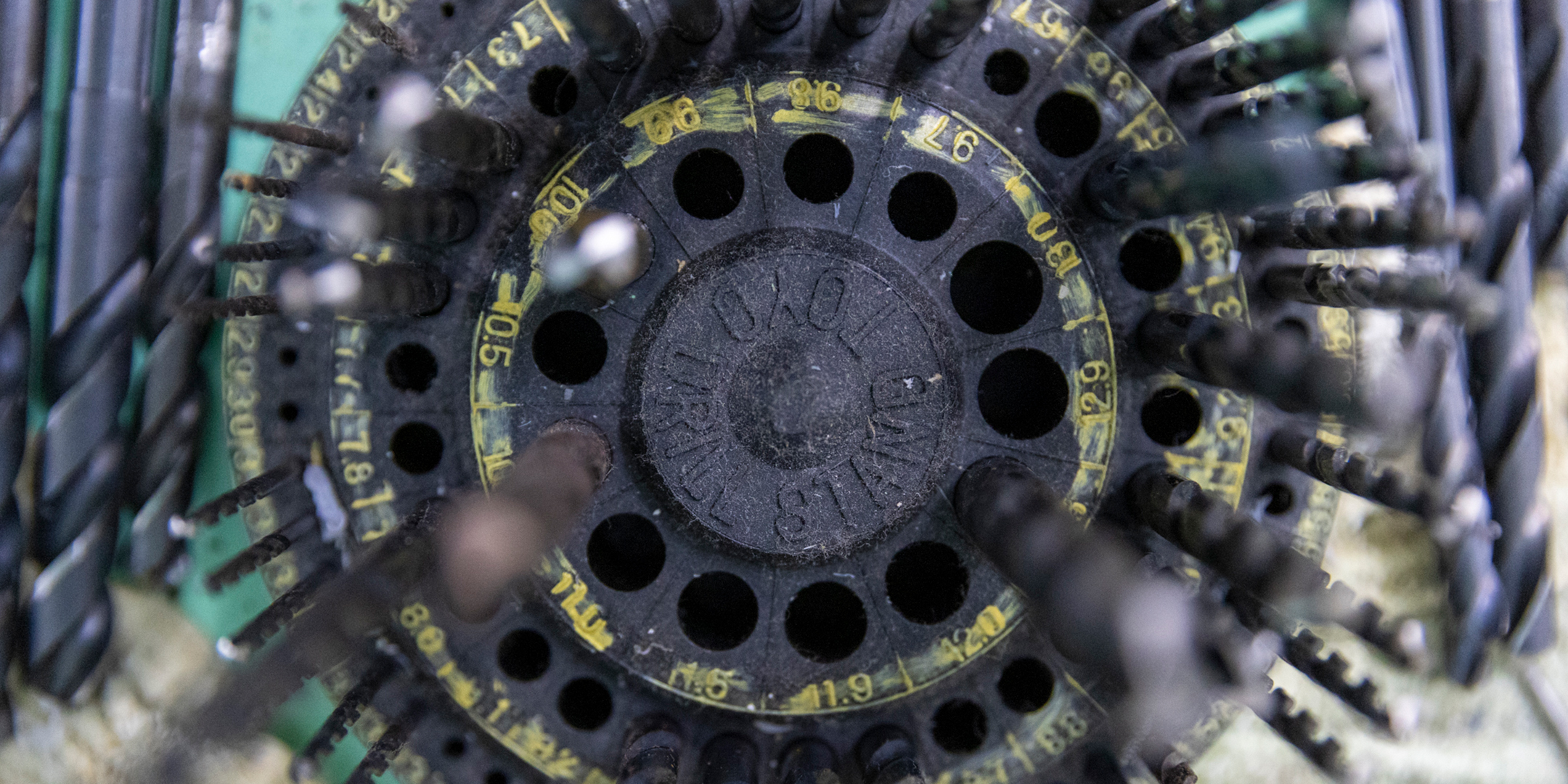
2. NCルーターが描く「自由な外形」
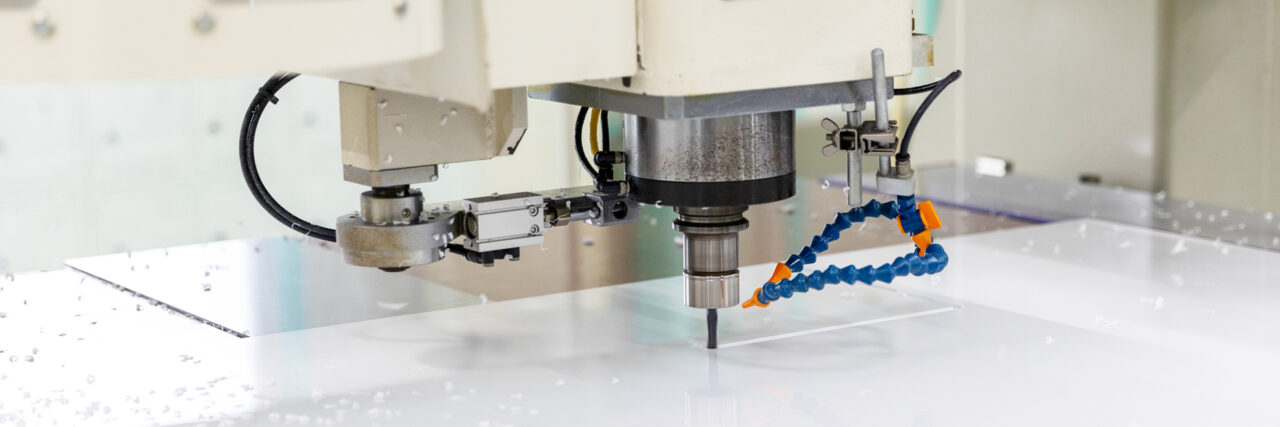
フラットで大判のプラスチック板材を効率よく加工するために欠かせないのが、NCルーターです。とりわけアクリルやPVCのように、レーザー加工では歪みや焦げが生じやすい素材に対して、熱影響を最小限に抑えながら精度良くカットできる点が大きな強みとなります。
当社のNCルーター加工には、次のような特徴があります。
- 真空吸着+定圧チャックによる高精度な材料固定
- ATC(自動ツールチェンジャー)による一連工程の効率化
- CAMソフトと連携した加工設計による自由曲面や複雑輪郭の再現性の高さ
これらによって、従来は複数工程に分けていた「粗取り→開口→面取り→ザグリ」までをワンチャックで実行できます。段取りミスや精度低下のリスクを抑え、加工コストと納期のバランスを最適化しています。
さらに、R形状や波型、非対称輪郭などの加工実績も多数あり、装置設計の初期段階から設計者と連携し、図面データをもとに工具選定や回転数などを最適化するフィードバックも行っています。
食品、医療、精密装置といった分野では、意匠性と機能性の両立が求められます。その要求に応えるために、NCルーターは今後ますます重要な役割を果たすと考えています。
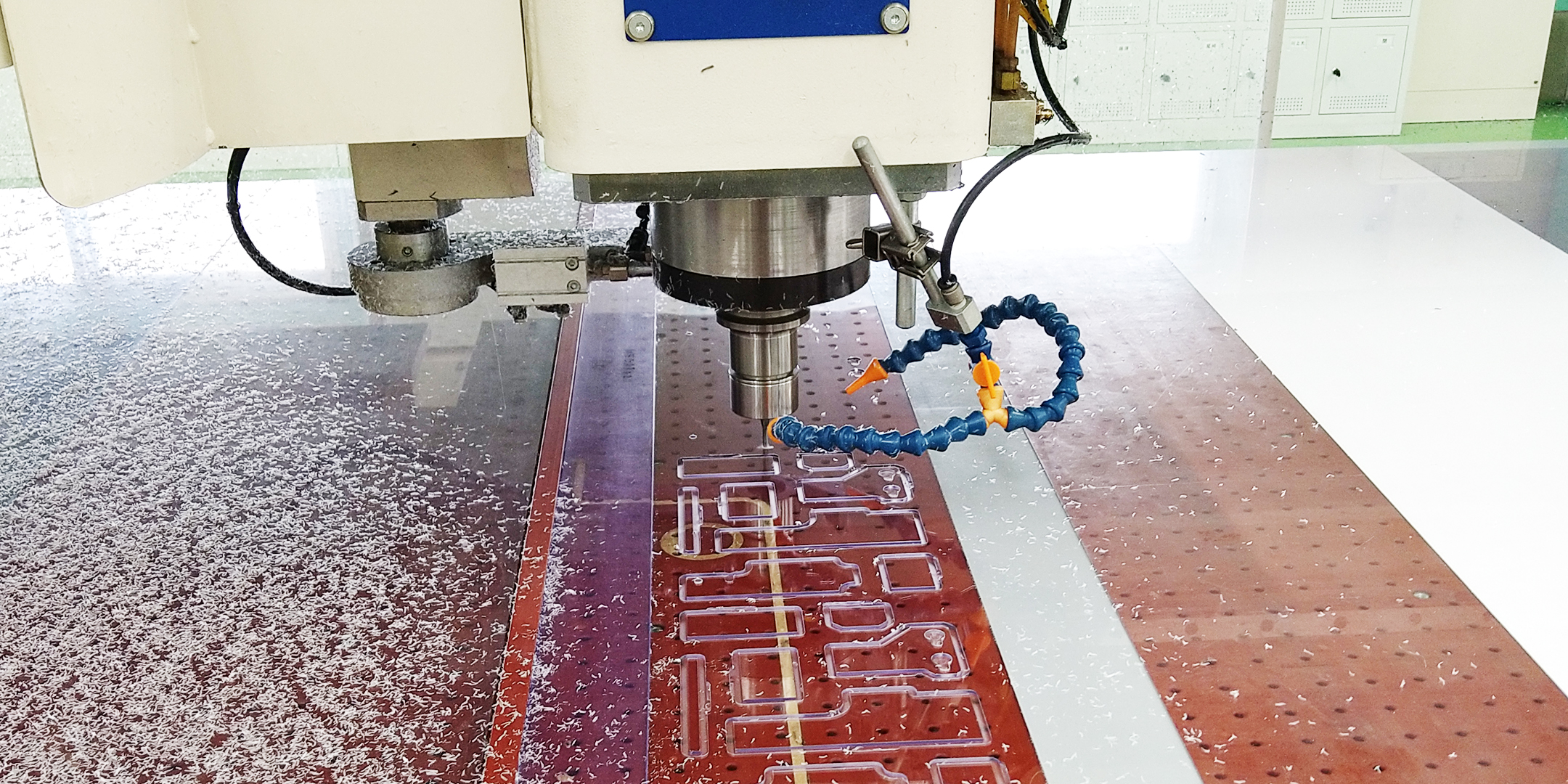
3. マシニングセンタが実現する「精度と持続性」
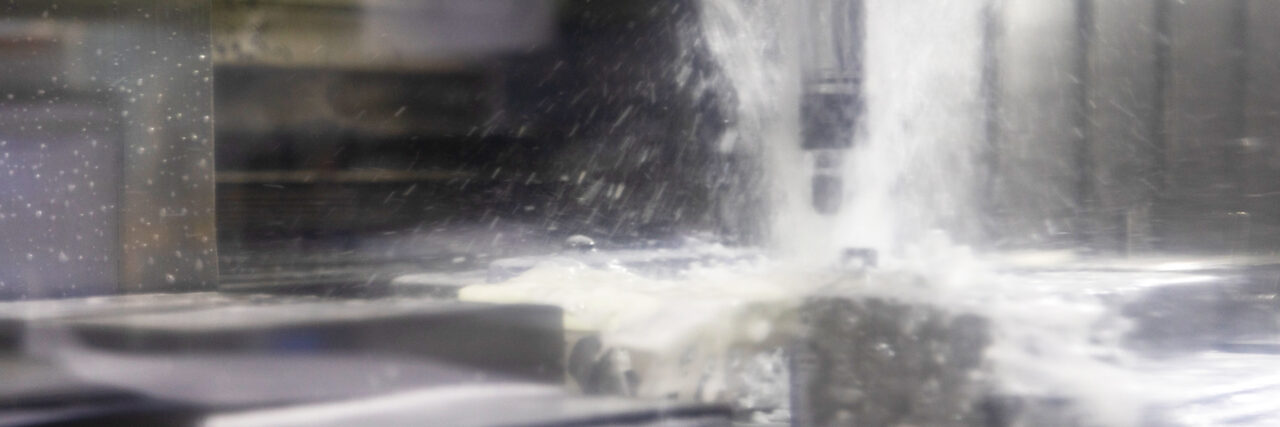
寸法精度だけでなく、その状態を長期間にわたって維持することが求められる場面では、マシニングセンタが不可欠な存在となります。特にエンジニアリングプラスチックは、温度や湿度、内部応力の影響を受けやすく、単に図面通りに削るだけでは実用上の精度を確保できない場合も多くあります。
当社では、次のような方法で実用精度の安定を図っています。
- 素材別の物性データベースに基づいた寸法補正の設計
- エンドミル摩耗や送り速度に対応するリアルタイムな条件最適化
- エアブローとミストクーラントによる熱対策の徹底
さらに、POMのように寸法変化が大きい素材に対しては、クランプ条件や加工経路を工程ごとに調整することで、バラつきを±0.1mm以内に抑える対応を行っています。加工後の測定や確認も、量産を見据えた基準で品質を確認する運用を重視しています。
このように、マシニング加工は素材の性質と継続的に向き合いながら最適化する工程であり、数値制御に加えて現場での知見と分析力を活かすことが求められます。
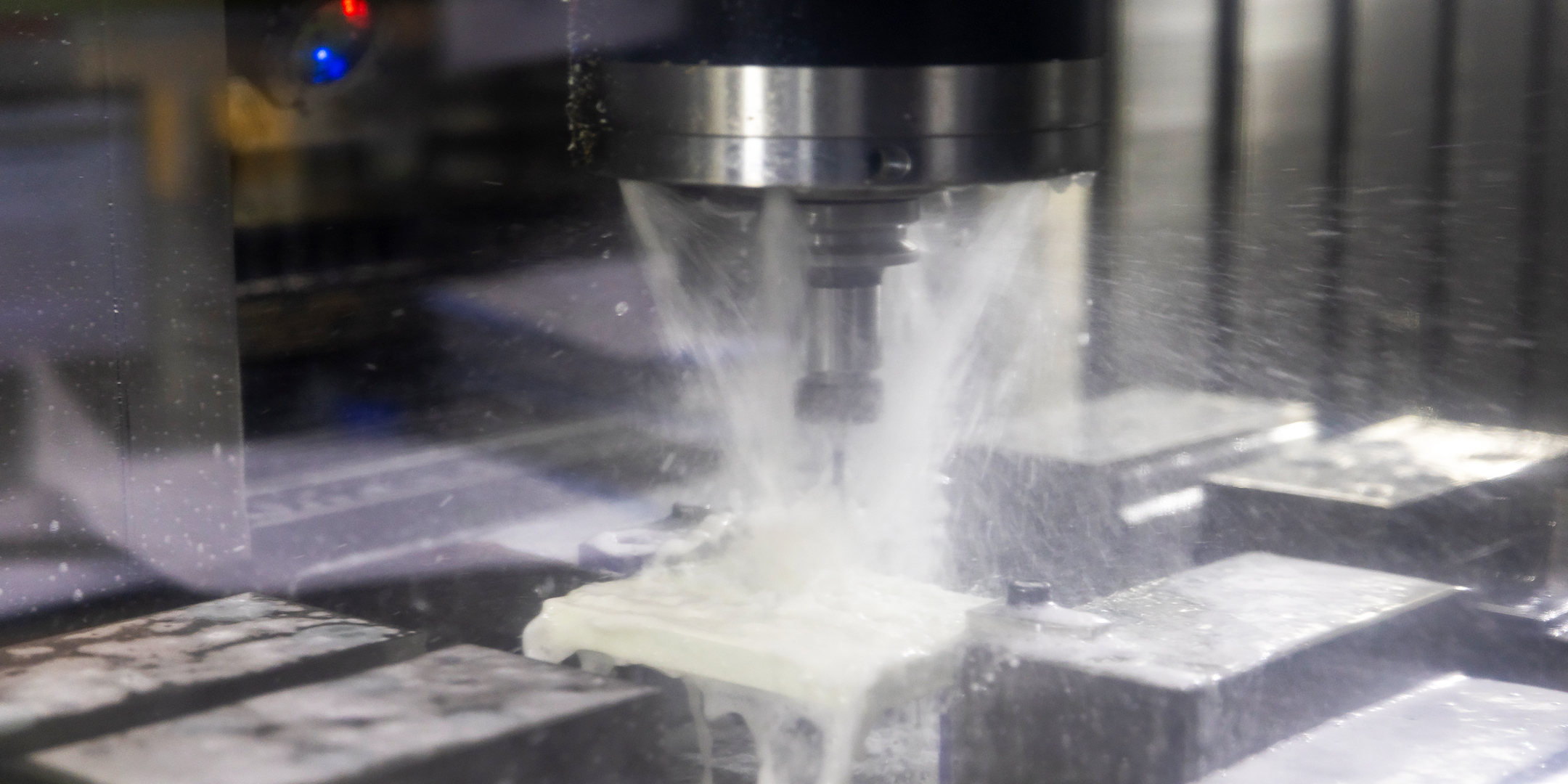
4. NC旋盤で担う「ねじと嵌合の信頼性」
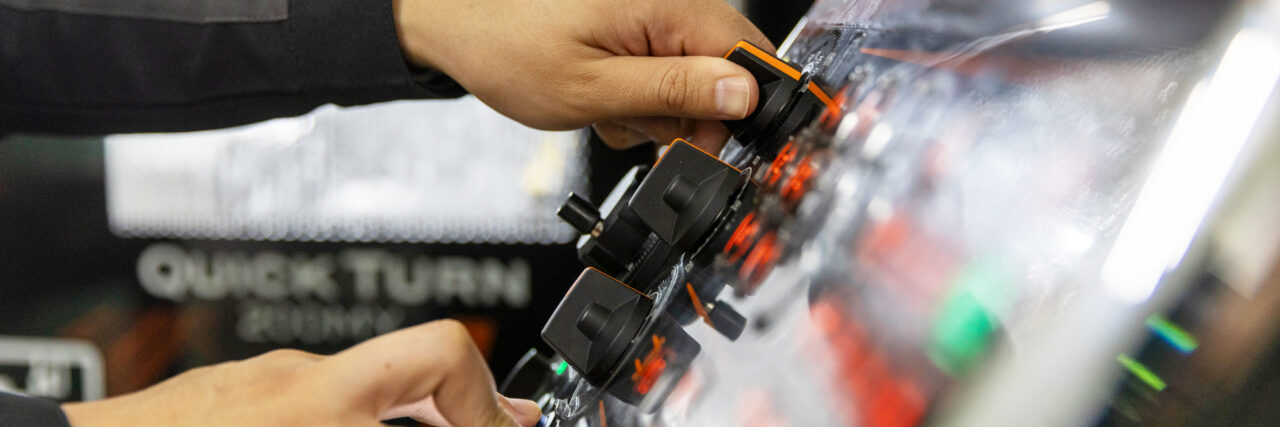
回転対称形状を持つ部品、特にねじやブッシュなどの嵌合部品には、寸法や表面品質だけでなく、使用時の「手応え」や「密着感」といった感覚的な性能も求められます。こうした要素は製品の信頼性と直結しており、NC旋盤にはより繊細な品質設計が必要です。
当社のNC旋盤加工では、以下のような点を重視しています。
- 単刃・小R工具での高送り加工によるバリの抑制
- 背面突っ切り時の送り速度制御による端面溶着の防止
- クランプ圧の最適化と変形防止の治具工夫
また、PEやPVCなどの熱に弱い素材に対しては、冷却効率を高める専用チャートを用意し、熱溜まりを防ぐよう工夫しています。工具の摩耗によって公差が逸脱しないよう、ロットごとの工具形状チェックも徹底しています。
医療機器に使われるネジ部品のように、外観・手触り・トルクのすべてにおいて高い品質が求められる場合でも、設計意図を的確にNC制御へと反映する加工力によって、それに応えています。

5. 木工機械の「スピード対応力」と実証効果
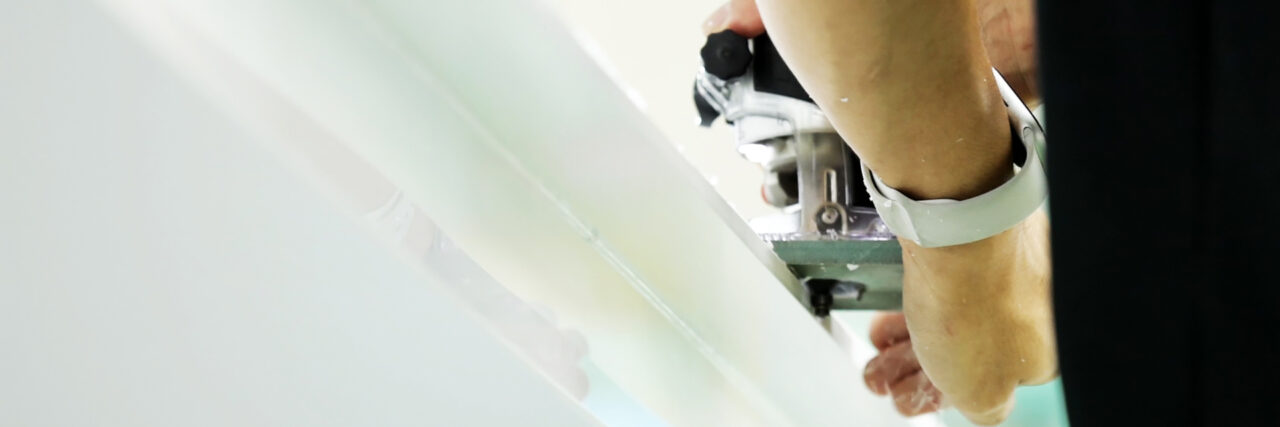
試作や仕様変更への対応を迅速に進めるうえで、木工機械の機動力は当社にとって欠かせない存在です。
当社では、パネルソーやルーター、手押しかんななどの木工機械を活用し、角度切りやR形状に対応した専用治具や当て板を、必要なタイミングで社内製作しています。
その理由は、「早い」「柔軟」「安価」という特性にあります。たとえば以下のような利点があります。
- 加工担当者自身が、現場判断で専用治具の製作・調整を即時に実施
- PVC素材を用いた仮加工や組付け確認により、実際の本番工程とのギャップを事前に把握可能
- 都度の段取りや外注手配を不要とすることで、リードタイムを最小化
角度付きや曲線部など、一般的に治具の手配や加工に時間がかかる場面でも、社内完結で迅速に対応できる体制が整っており、
製品検証や設計フィードバックのサイクルを必要なタイミングで即回せる柔軟性を生み出しています。
木工機械は、単なる補助的な機器ではなく、当社の「現場主導型スピード対応」の中核を担う実践設備です。
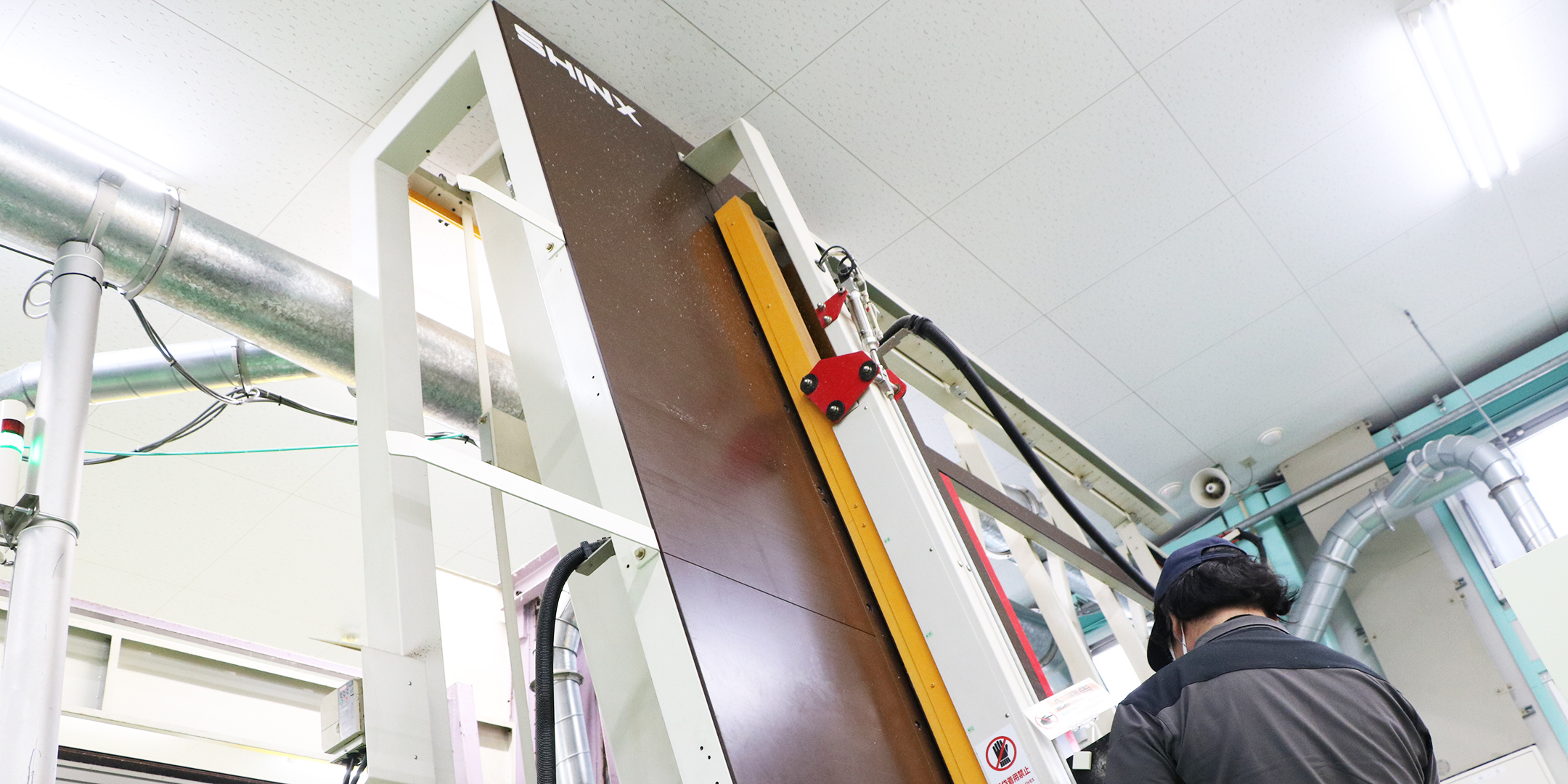
6. 曲げ加工が生み出す「形状のなめらかさと清掃性」
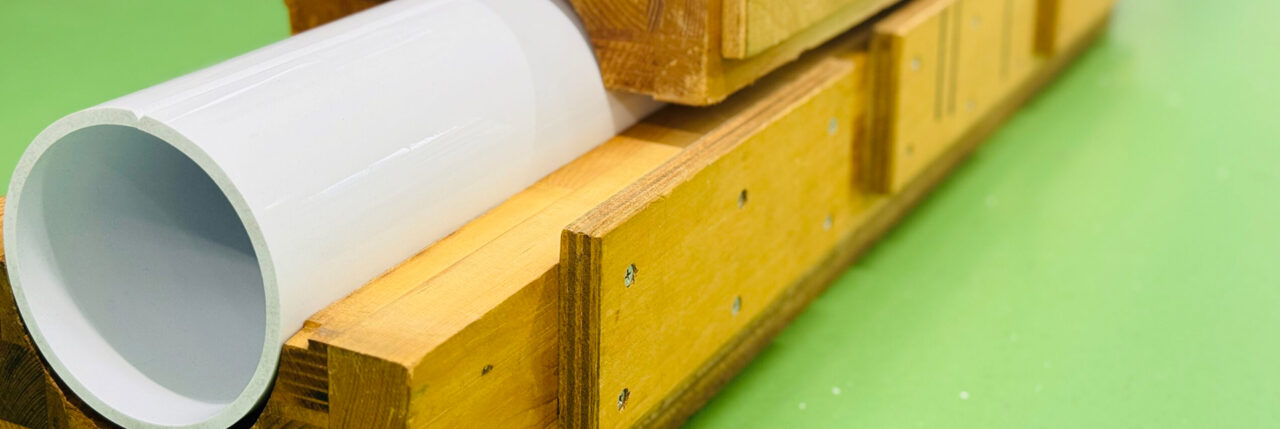
立体構造を形成するうえで、切削と並んで重要な役割を担うのが「熱曲げ加工」です。曲げ加工は、プラスチック素材に熱を加えて軟化させ、専用の治具や定規に沿って意図した角度に変形させる加工法であり、当社では主にPVCやアクリル、PPといった素材に適用しています。
この技術の最大の利点は、一体構造を維持したまま形状を変化させられることにあります。接合部を設けずに成形することで、水や薬液の流れを妨げる段差や隙間が発生せず、洗浄性・衛生性の向上に直結します。たとえば食品製造ラインのホッパーや排水トラフでは、内部に段差がない「なめらかな構造」を実現することで異物滞留のリスクを抑え、HACCP対応にもつながります。
- 一体成形による衛生性と洗浄性の向上
- 接液部の段差レス設計による機能性向上
- 強度・清掃性・美観を兼ね備えた完成度の高い製品提供
当社では、素材ごとの軟化温度・加熱時間・冷却条件をあらかじめデータベース化しており、治具設計から最終工程までを見越した曲げ加工の標準化を行っています。また、反りや歪みが生じやすい厚板や大判部材に対しては、二次熱処理や冷却治具によって寸法安定性を担保する工程管理も徹底しています。
さらに、曲げ加工と溶接を組み合わせた「連携設計」も多くの現場で実践しています。たとえば、L字形に曲げたパネルと底面板を溶接することで、接合点を最小限に抑えつつ、剛性と水密性の両立を図った構造体を実現できます。こうした一貫対応によって、製品の耐久性・意匠性・清掃性のすべてにおいて高い評価を得ています。
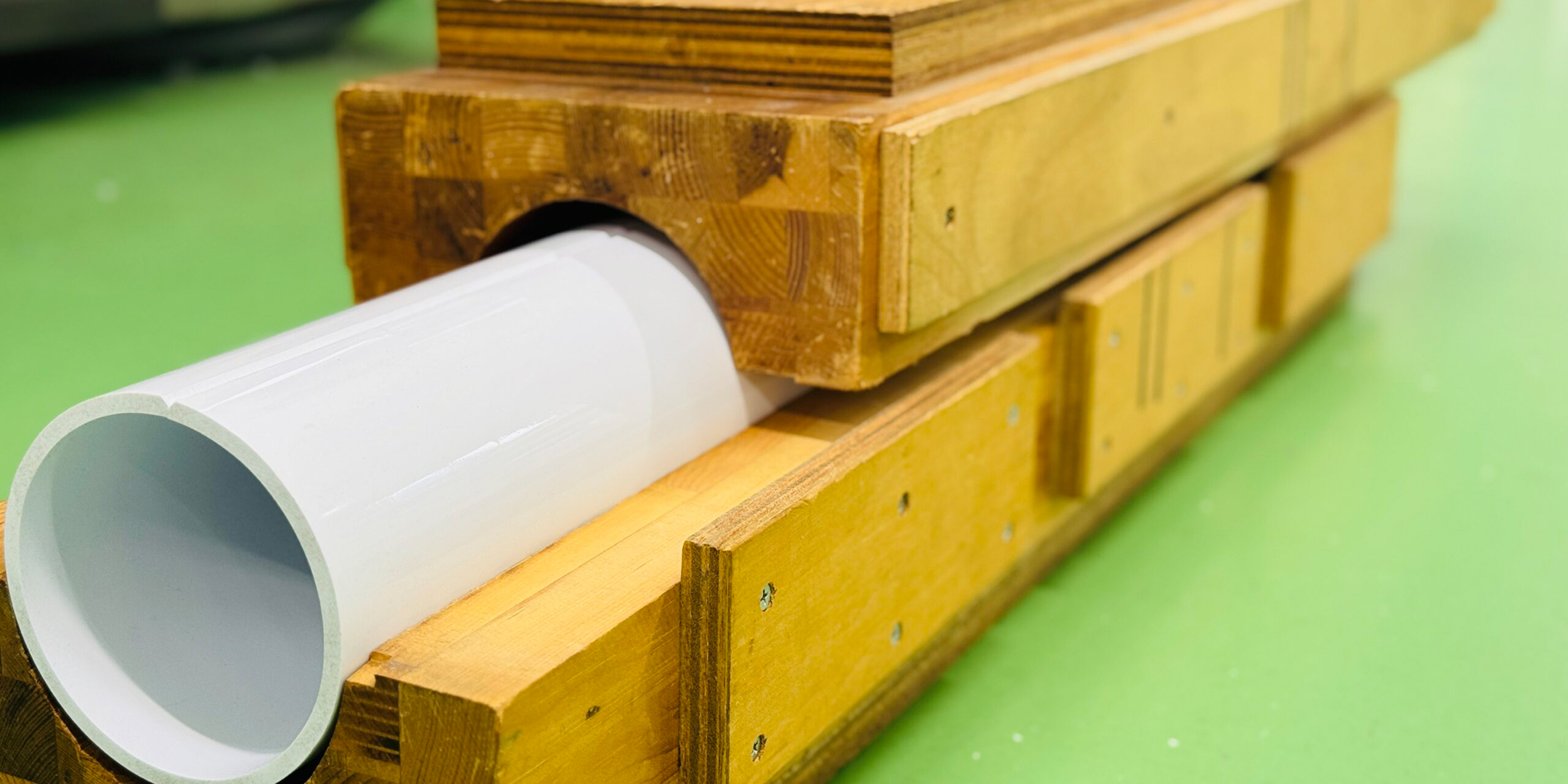
7. プラスチック溶接が「設計自由度と機能性」を担保する
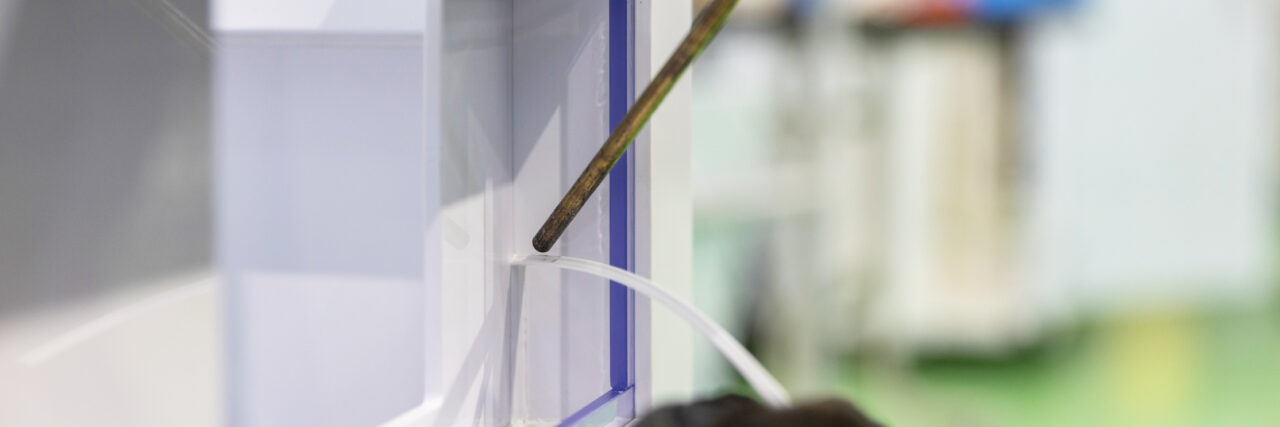
当社の加工技術の中で、唯一「形をつくる」工程といえるのが、プラスチック溶接です。切削や曲げが寸法や形状の一部を形成する技術であるのに対し、溶接はそれらを「つなぎ合わせて構造体を完成させる」工程です。
フジワラケミカルエンジニアリングが行う溶接加工には、次のような特長があります。
- 金型不要で、1個から自由形状に対応できる柔軟性
- 水密・気密性能に優れる強固な接合部
- 6m超の筐体にも対応可能な大型構造への適応力
たとえば、半導体装置向けの洗浄槽では、曲げ加工したPVC板を精密に溶接し、内部空間の水密性と耐薬品性を確保しています。さらに、洗浄時の作業性を考慮して接合部の内R(アール)もコントロールし、清掃性の高い内部構造を実現しています。
溶接による接合は、切削加工だけでは実現できない三次構造や密閉空間の形成を可能にし、意匠性と機能性の両立を支えています。また、酸・アルカリ・有機溶剤といった幅広い薬液に対しても、素材選定と溶接条件の最適化によって対応できるため、耐薬品性の向上にも大きく寄与します。
こうした特性を活かし、当社では装置の設計自由度を最大化しつつ、機能性と信頼性を高次元で両立する加工を実現しています。
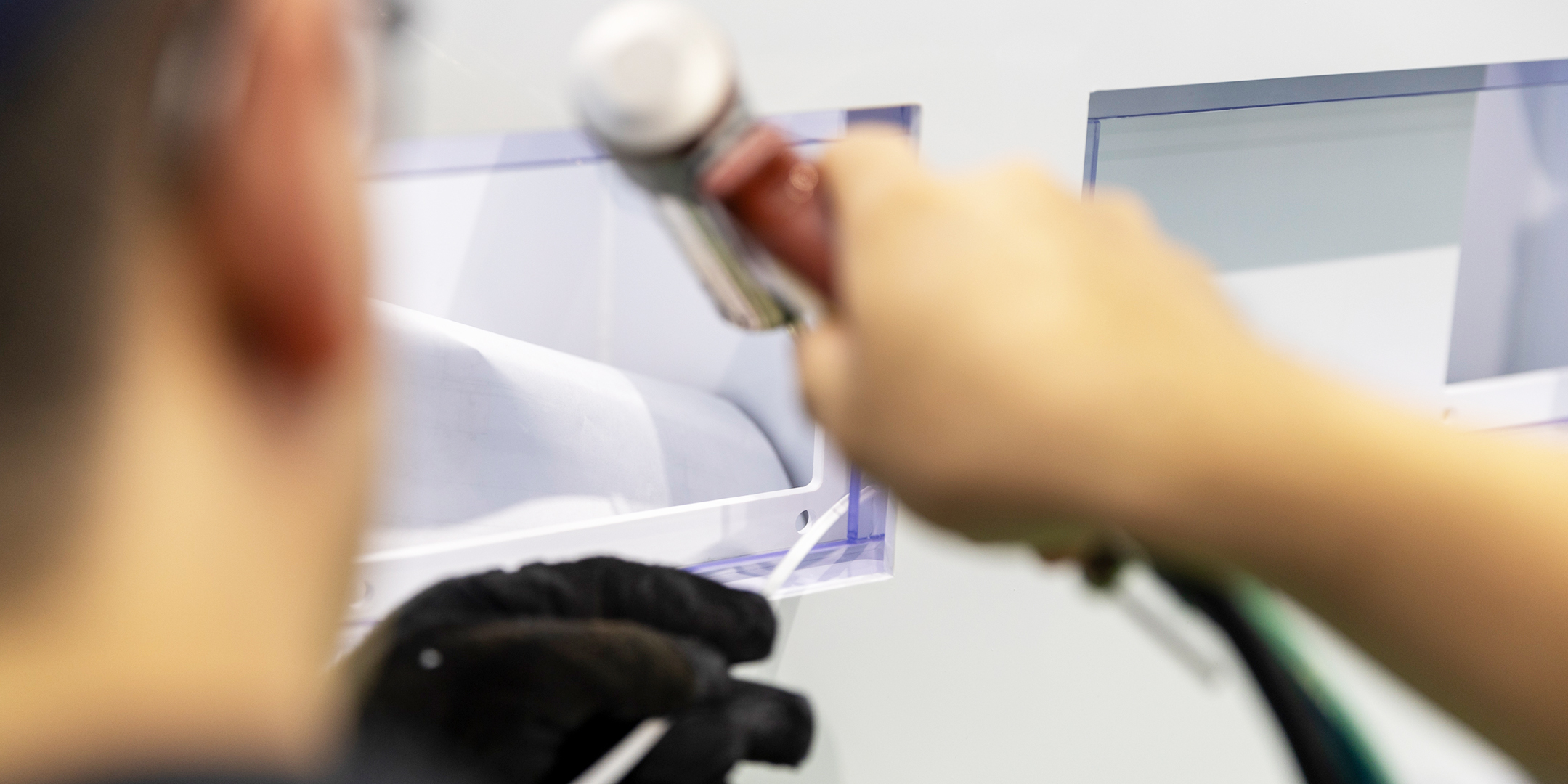
8. 「工程全体を設計」するという考え方
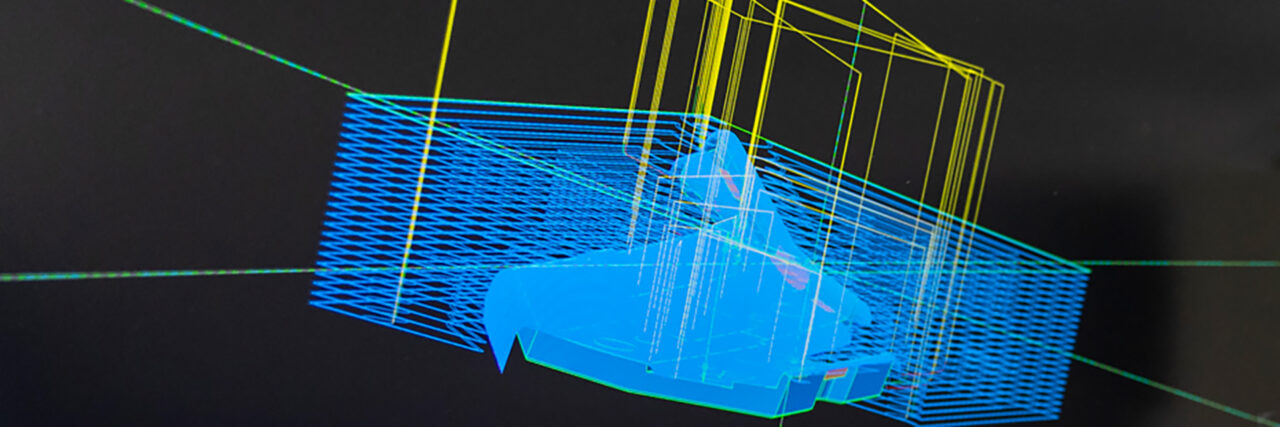
ここまで紹介してきた各加工工程は、いずれも高精度かつ安定した品質を発揮する技術ですが、フジワラケミカルエンジニアリングの最大の強みは、それらを単独で活用するのではなく、工程全体を見渡して最適な加工・組み立てフローを設計できる点にあります。
たとえば、ルーターで大判材を切り出し、必要に応じて木工機械で仮治具を作成、マシニングセンタで開口部や精密形状を加工し、NC旋盤でねじなどの機能部を成形。さらに、曲げや溶接によって立体構造を構成し、最終的にはそれらを組み上げて完成形の筐体を構築する。こうした一連のプロセスを、当社はすべて自社内で一貫対応しています。
このように、各設備の特性を最大限に活かしながら、製品仕様や納期、数量などの条件に合わせて加工と組み立てを統合的に設計する力が、当社の競争力の源泉となっています。
- 各加工工程(切削、旋盤、ルーター、木工、溶接など)を単独でなく連携して活用できる設計力
- 工程全体を見渡して、加工から組み立てまでを含めた最適なフローを構築
- 用途・ロット・コストに応じて柔軟に工程を設計・運用できる体制
- 製品仕様・納期・数量などに合わせて、設備特性を活かした統合設計が可能
9. 品質保証と組織力による「総合対応力」
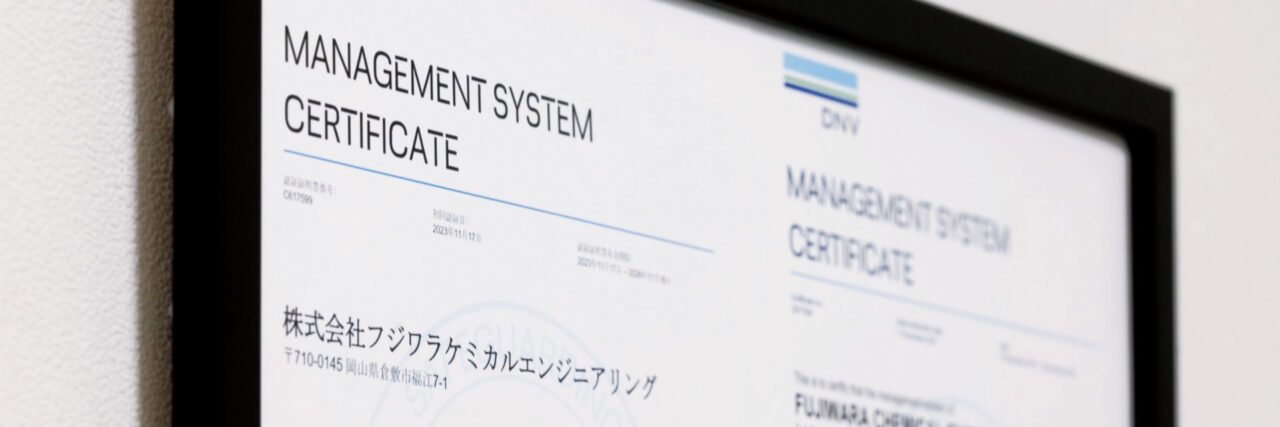
当社では、ISO 9001:2015に基づいた品質管理体制を構築し、「加工→組み立て→検査→記録→出荷」までの各工程において明確なトレーサビリティを確保しています。受発注情報は一元管理しており、加工履歴、検査成績書、使用工具の情報などをすぐに確認できる環境を整えています。
工程管理において特に重視しているのは、次の3点です。
- 初品・中間・最終の3段階QCチェックポイントの設定
- 作業者の教育履歴・技能資格のデジタル管理
- 改訂図面との照合による変更対応の強化
これらの管理によって、量産品・試作品・特注品を問わず、安定した品質保証と短納期体制を同時に成立させています。
終章:すべての設計自由は「加工と組み立てのつなぎ方」から始まる
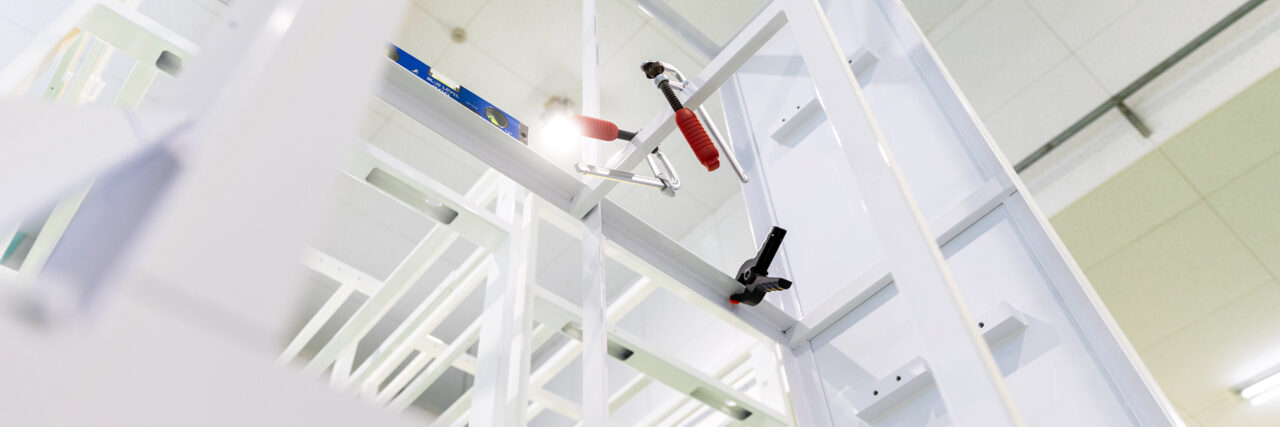
部品の精度や仕上がりの美しさだけでなく、組み立てや洗浄、設置といった使用フェーズを含めて評価される時代が来ています。こうした中で、真に求められるのは「加工と組み立ての自由度」であり、それを担保するのが「工程の設計力」です。
フジワラケミカルエンジニアリングでは、治具設計、切削、曲げ、溶接を含めた組立までを一貫して対応することで、お客様の設計意図をそのまま形にできる体制を整えています。
「他では断られた形状」「納期に間に合わない仕様」「図面化しづらいイメージ」。そうした課題に対しても、まず相談できる存在として、これからも「加工と組み立てを設計する企業」としてものづくりを支えていきます。