プラスチック溶接の基礎と応用:熱風溶接(ホットジェット溶接)の実際
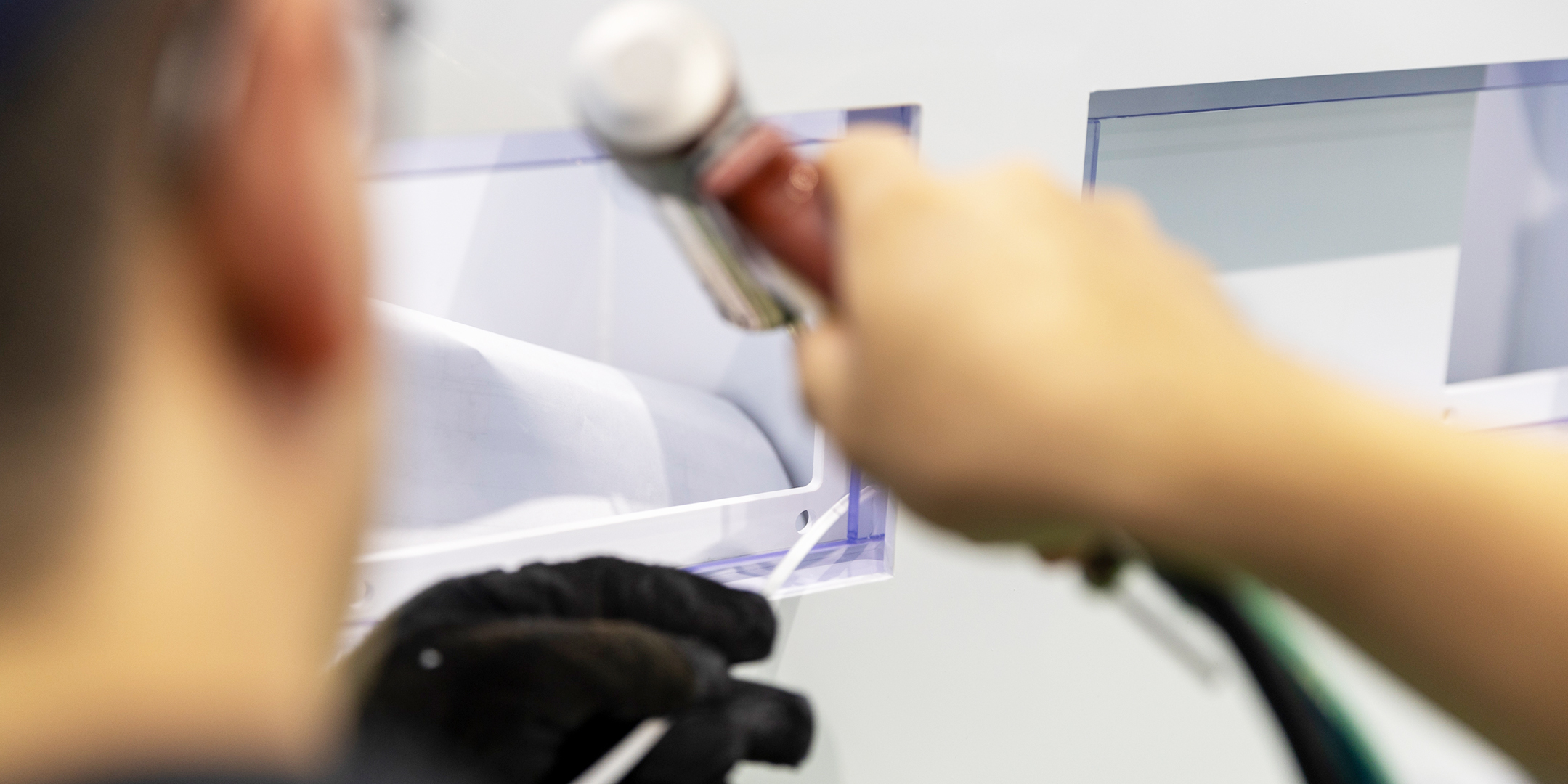
プラスチック製品の製造方法には、主に「成形」「切削」「溶接組立」の3つがあります。
成形は型を用いるため初期投資が必要ですが、大量生産に適しており、コストダウンが見込めます。
切削は平板や丸棒などをルータやマシニングセンタ、旋盤などで削り出す方法で、高い精度や少量生産に適しています。
溶接組立は、切削によって加工された板などを熱によって接合するため、成形や切削だけでは製作しづらい複雑な形状や大型製品にも対応可能です。
このページでは、プラスチック溶接に関する基本的な知識から、実際に使用されている溶接方法、フジワラケミカルで対応可能な材質や実績、溶接技術のメリットとデメリット、安全性の注意点、さらに活用されている具体的な分野について詳しく紹介します。これにより、プラスチック溶接の全体像を理解していただける内容となっています。
プラスチック溶接と金属溶接の違い
「溶接」と聞くと、金属を接合する金属溶接を思い浮かべる方が多いかもしれません。このコラムではプラスチック溶接を中心に取り扱うため、まず金属溶接とプラスチック溶接の違いを表にまとめました。
特徴 | 金属溶接 | プラスチック溶接 |
---|---|---|
材料 | 鉄、アルミなどの金属 | PVC、PPなどの熱可塑性樹脂 |
方法 | アーク溶接、TIG/MIG溶接など | 熱風溶接(ホットジェット溶接)、超音波溶接など |
融点 | 高い | 低い |
強度 | 高い | 接合条件に依存 |
適用分野 | 建設、車両、航空 | 医療、化学、電子 |
特筆すべきなのは、適用分野の違いです。金属溶接とプラスチック溶接は、それぞれの材料特性に基づき、異なる使用環境でその特性を発揮します。
金属溶接は、鉄やアルミニウムなどの金属を高温で溶融し接合する方法で、耐久性や機械的強度が求められる分野で広く活用されています。特に航空機や車両、建設業など、高温や高圧がかかる過酷な条件下で使用されています。
一方、プラスチック溶接は、化学的腐食に対する耐性や軽量性が求められる分野で重要な役割を果たします。熱可塑性樹脂を比較的低温で加熱・溶融して接合することで、半導体製造装置、医療機器、電子機器、化学薬品タンクなど、腐食環境や軽量化が求められる製品に適用されています。
このように、金属溶接とプラスチック溶接は、それぞれの材料特性に基づいて適切に使い分けられています。
- 高温や高圧、摩耗が発生する環境に適する。
- 使用例:航空機、車両、建設業
- 化学的腐食が懸念される環境や、軽量性が求められる分野に適する。
- 使用例:半導体製造装置、医療機器、電子機器、化学薬品タンク
以上、金属溶接とプラスチック溶接の違いを踏まえた上で、プラスチック溶接の具体的な方法と応用について詳しく解説します。
プラスチック溶接の種類
プラスチックの工業的な接合方法には、溶剤を使う接着と、熱による溶接があります。
溶接のなかでも、とくに「熱風溶接(ホットジェット溶接)」が一般的です。
以下に主な溶接方法を挙げます。
- 熱風溶接(ホットジェット溶接):ノズルから高温の熱風を吹き付けて接合する溶接方法。加工の柔軟性が高く、さまざまな分野で広く使用される。
- 熱板溶接:加熱した金属板を接合部に挟んで溶かし、圧力をかけて接合する溶接方法。
- 摩擦溶接:部材同士を回転や振動で摩擦させ、摩擦熱で接合する溶接方法。
- インパルスシール溶接:電熱線に電流を流して発熱させ、加熱と圧力を利用して接合する溶接方法です。包装材や薄いプラスチック素材の接合によく用いられる。
- 火炎溶接:ガスバーナーなどを使用して火炎を直接当てて接合する溶接方法。
- 高周波溶接:高周波電磁波で誘電加熱を行い、接合部を溶かして圧着する溶接方法。
- 超音波溶接:高周波の振動エネルギーで接合部を加熱・溶融し、圧力を加えて接合する溶接方法。
当社では、主に熱風溶接と溶剤による接着を行っています。なお、接合以外にも、切削加工や電気炉を利用した曲げ加工など、さまざまな加工方法に対応しています。
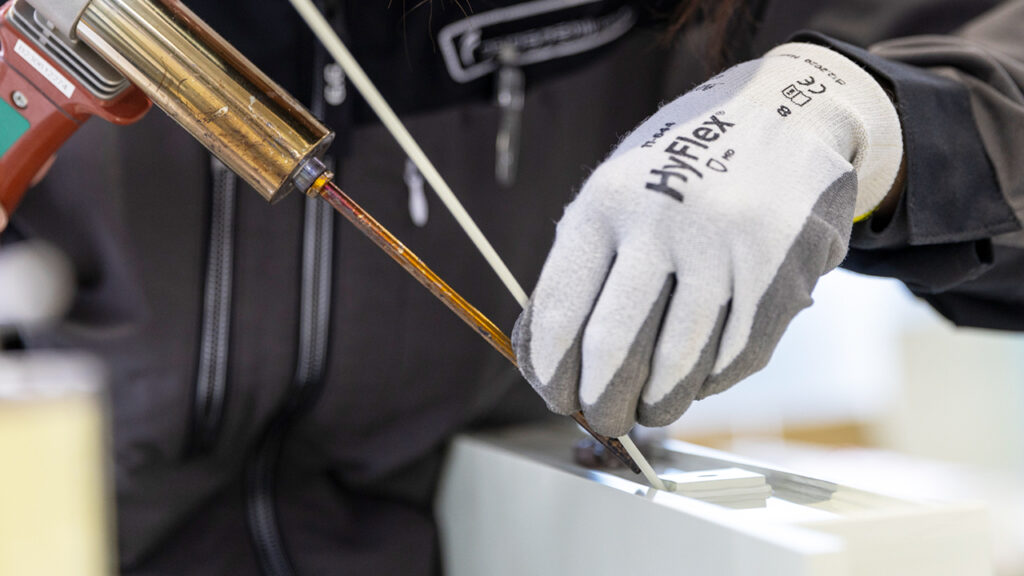
熱風溶接
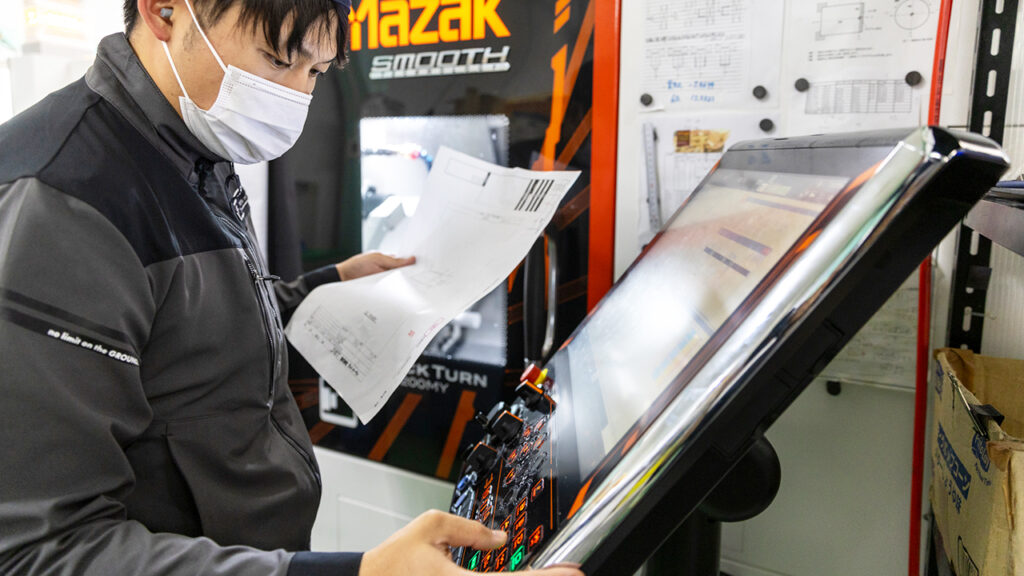
NC旋盤
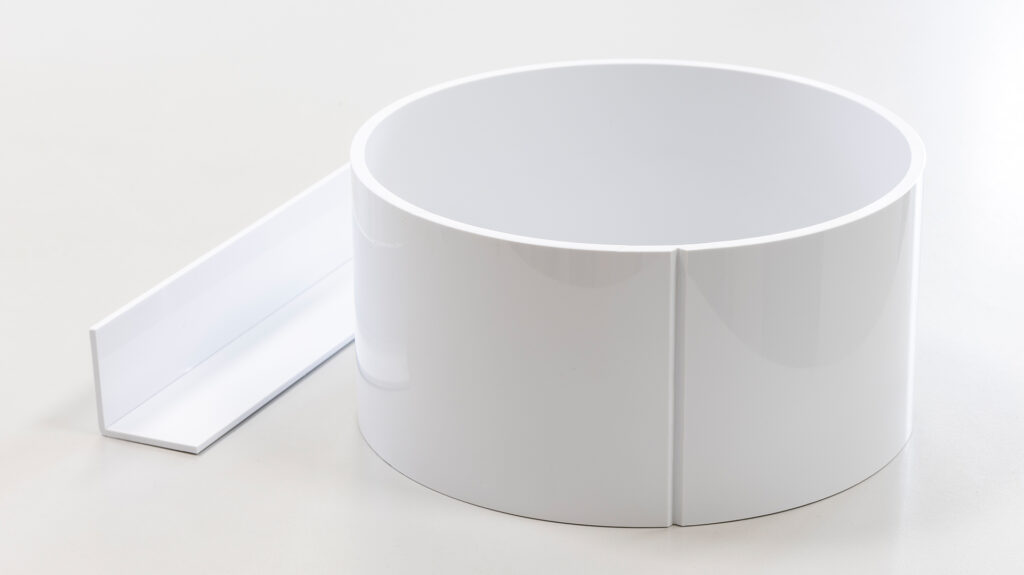
曲げ加工パーツ
フジワラケミカルエンジニアリングでの溶接可能な材質と製品例
当社では、PVC(ポリ塩化ビニル)を中心にプラスチック溶接を行っています。PVCは半導体系の装置筐体で多く使われており、当社でも大型筐体の製作実績があります。
また、たいていの場合は金属フレームにPVCを巻く(ライニング)加工になりますが、金属フレームも協力企業から調達可能です。
溶接可能な材質
当社での溶接実績があるプラスチック素材は、下記のとおりです。
- PVC(ポリ塩化ビニル)
- PP(ポリプロピレン)
- PVDF(ポリフッ化ビニリデン)
- PMP(ポリメチルペンテン)
- PMMA(ポリメチルメタクリレート、通称アクリル)
- PE(ポリエチレン)
製品例
当社は半導体製造装置・機器の分野を得意としており豊富な実績があります。
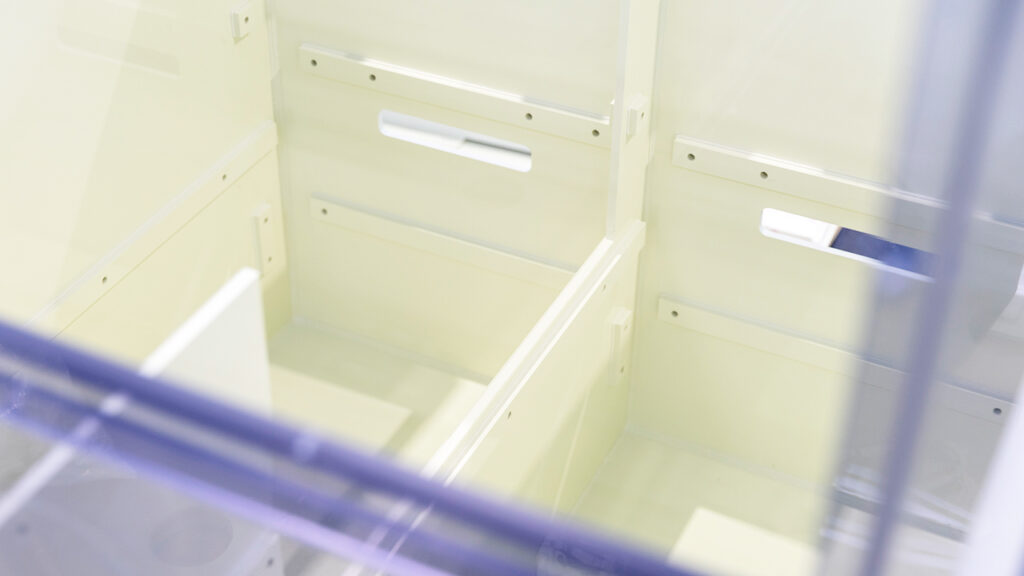
半導体洗浄浴槽
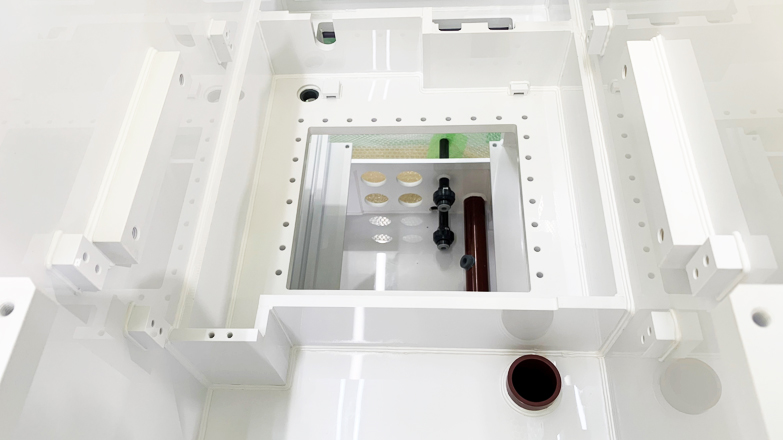
薬液供給ユニット
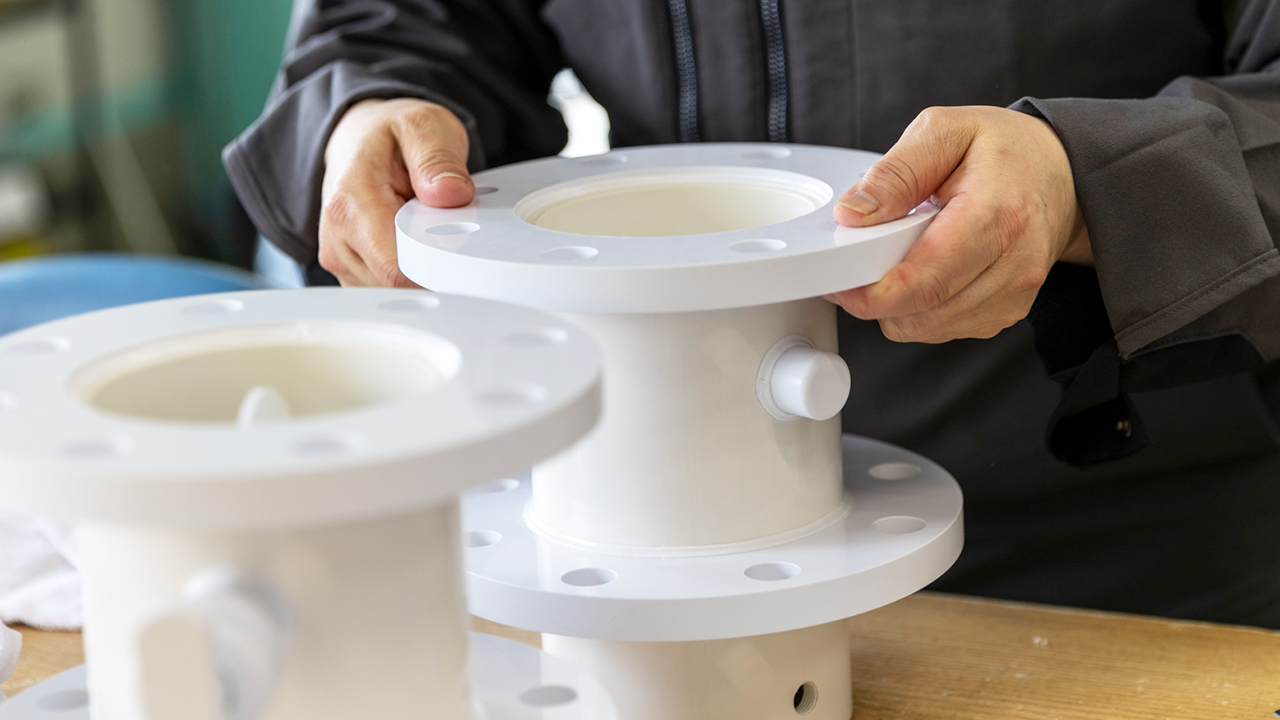
溶接フランジ部品
その他の製品例については以下のページをご覧ください。
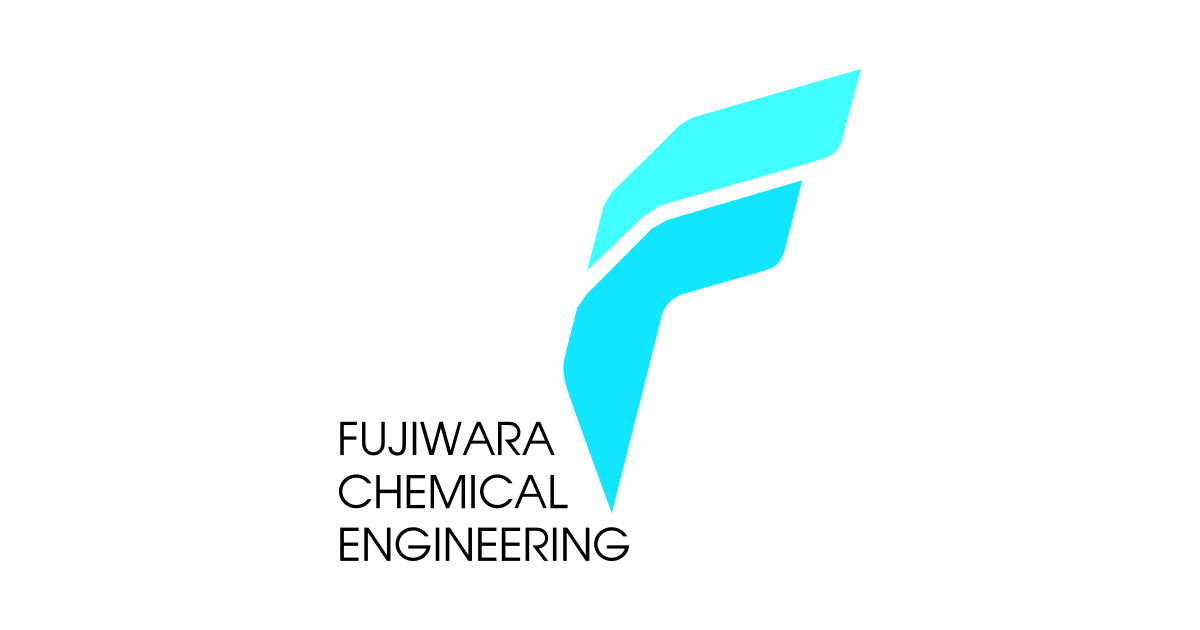
プラスチック溶接のメリット・デメリット
プラスチック溶接は、上記のような幅広い材質に対応可能であり、さまざまな用途に適しています。しかし、この技術には独自の利点と課題も存在します。次に、プラスチック溶接のメリットとデメリットについて詳しく解説します。
- 複雑形状や大型の形状が製作可能:成形や切削加工では難しい形状も、溶接によって自由度の高いものが作れる。
- 耐薬液性・軽量化・透明性が期待:金属からプラスチックに代替することで、薬液への耐性や軽量化、さらには透明化などの特性を活かせる。
- 溶接熱による歪み:プラスチックは金属に比べて耐熱温度が低いため、溶接時の熱の影響を受けやすく、歪みや変形が生じることがある。
- 引張強度の低さによる耐久性への注意:金属よりも引張強度が低いため、使用条件によっては破損や劣化につながる可能性がある。
これらのメリット・デメリットを踏まえ、当社では組み立てや溶接の観点から、より高品質な製品を実現するための部品設計に関するアドバイスを行っています。溶接方法や材質の選定、接合部の構造設計など、製品の機能性や耐久性を最大限に引き出すための提案をさせていただきます。お客様のニーズに合わせた最適な設計をサポートすることで、長期的な信頼性とコストパフォーマンスの向上に貢献します。
熱風溶接(ホットジェット溶接)と接着の安全性
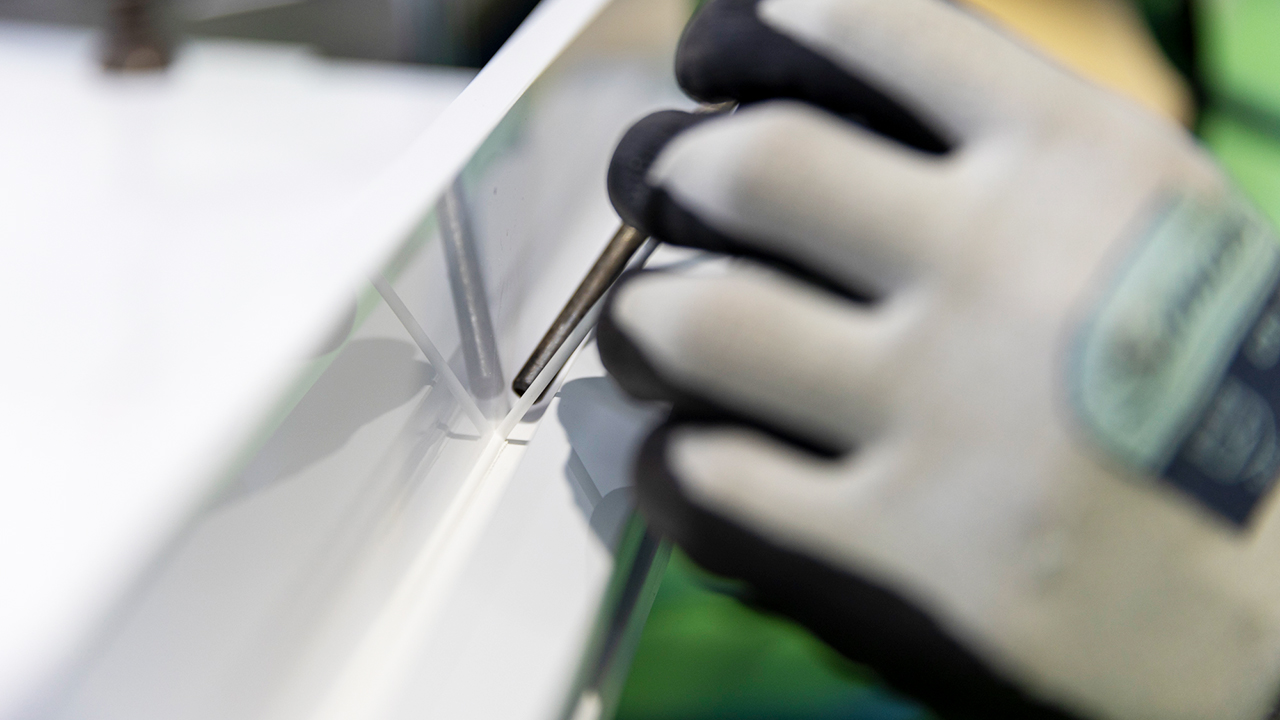
プラスチック溶接に用いるホットジェットガンのノズル先端から出る熱風温度は、材質によって調整しますが、PVCの場合はおよそ260~280℃ほどです。これは金属溶接と比べるとかなり低温であり、火傷のリスクは比較的少ないとされています。また、金属溶接時に問題となる溶接ヒュームや有害ガスも、プラスチック溶接では大部分が発生しません。ただし、フッ素樹脂の溶接では有害ガス(フッ化水素ガスなど)が発生する可能性があるため、作業環境の換気や防毒マスクの使用といった安全対策が必須です。
また、接着に用いる有機溶剤については、呼吸器からの吸入や皮膚からの吸収が起こりやすいため、特に注意が必要です。これらのリスクに対処するため、当社では独自の安全基準を策定し、換気設備の整備、作業者への保護具の支給、安全教育の徹底を行っています。有害ガスや溶剤の影響を最小限に抑えるための具体的な対策を講じ、事故や健康被害の未然防止に努めています。
このように、作業環境と作業者の安全性を確保するため、全ての工程において厳格な管理を行い、高い安全基準を維持しています。
プラスチック溶接が使われている分野
半導体製造設備・機器やプリント基板製造設備、理化学機器やメッキ設備、各種プラントの空調ダクト・排気ダクトなどに使用されています。
- 半導体製造装置・機器:高精度が求められる装置や部品が多く、外観美・仕上がりも重視される。
- プリント基板製造設備:耐薬液性や軽量化が必要な電子部品製造設備に多く利用されている。
- 理化学機器:実験や分析に必要な機器で、耐薬液性や精密さが重要。
- メッキ設備:金属表面処理装置として、耐腐食性や耐薬品性を備えた部品が必要。
- プラントの空調ダクト・排気ダクト:化学プラントや工場での排気ガス処理装置で、防錆・防湿性や軽量化が求められる。
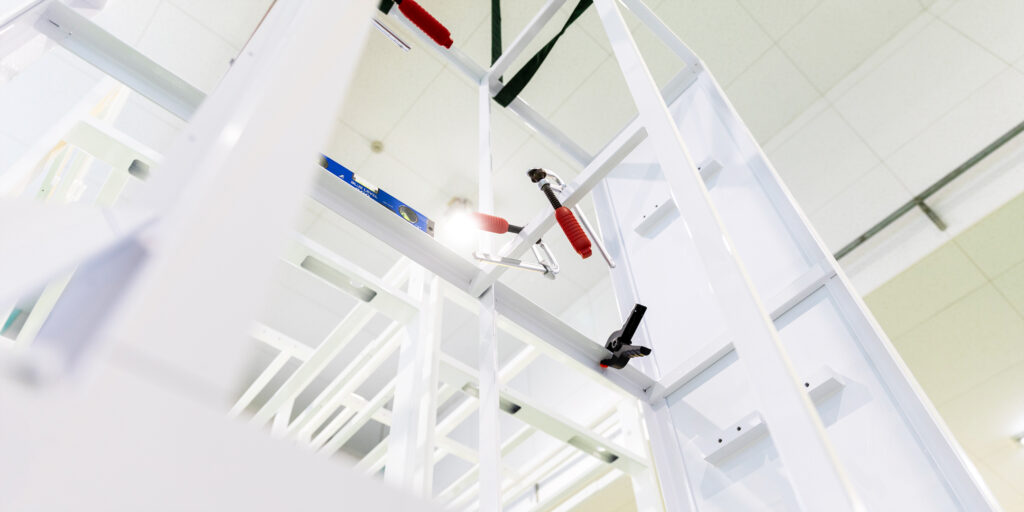
当社では、半導体製造装置・機器において豊富な実績を誇り、高精度が求められる分野でも確かな品質(ISO9001:2015対応)を実現します。
細かな傷や汚れが許されない厳しい基準にも対応し、美しい仕上がりを実現することでお客様のご要望にお応えしています。
まとめ
プラスチック溶接は、複雑形状や大型製品の製作、耐薬液性・軽量化・透明性の実現において重要な技術です。
本コラムでは、溶接方法の種類、対応可能な材質、メリット・デメリット、安全性の注意点、そして活用分野について解説しました。
特に「熱風溶接(ホットジェット溶接)」は汎用性が高く、フジワラケミカルエンジニアリングでも実績のある主要な技術です。この溶接技術を活用することで、成形や切削加工だけでは難しい製品の製作が可能になります。
当社では、半導体製造装置などの高精度が求められる分野にも対応しており、プラスチック溶接に関するご相談やお見積もりを随時受け付けております。お気軽にお問い合わせください。